O que é moldagem por injeção?
A moldagem por injeção é um processo de fabricação amplamente utilizado para a produção de peças plásticas em grandes quantidades. O processo envolve o uso de uma máquina de moldagem por injeção para fundir o material, injetá-lo em um molde sob pressão e produzir componentes na forma desejada após o resfriamento.
Uma grande parte das peças plásticas do dia a dia é produzida por moldagem por injeção. Esses componentes incluem itens como escovas de dentes, peças de automóveis e carcaças de eletrodomésticos.
A moldagem por injeção é popular devido ao seu baixo custo unitário e à capacidade de fabricar formas complexas com qualidade consistente. Plásticos, principalmente polímeros termoplásticos, são usados como matéria-prima e podem ser coloridos ou preenchidos com aditivos.
É necessário um alto grau de flexibilidade no design. Comparado a outros processos de fabricação, como usinagem CNC, a moldagem por injeção permite uma variedade significativamente maior de texturas superficiais e materiais.
Equipamento de moldagem por injeção
Do ponto de vista técnico, o processo de moldagem por injeção requer uma máquina de moldagem por injeção e um molde especificamente feito para a peça a ser produzida.
Máquina de moldagem por injeção
Uma máquina de moldagem por injeção consiste em três partes principais: a unidade de injeção, o molde e a unidade de fechamento ou ejeção.
Dentro da unidade de injeção, um funil alimenta o plástico para um êmbolo de injeção ou parafusos do tipo rosca e unidade de aquecimento. Quando a quantidade necessária de plástico fundido é acumulada, o processo de injeção é iniciado.
O material é fundido por calor/cisalhamento e injetado no molde sob alta pressão. É lá que as peças moldadas por injeção são formadas.
A unidade de fechamento ou unidade de ejeção tem a função de abrir e fechar o molde e ejetar os produtos moldados. As unidades de fechamento tipo alavanca são as mais comuns e consistem em placas para segurar o molde. Essas placas, geralmente dispostas verticalmente na estrutura do equipamento, podem ser comparadas a uma prensa interna que exerce uma forte força de fixação. Alternativamente, as unidades de fechamento do tipo hidráulico direto usam um cilindro hidráulico para exercer a força de fixação no molde.
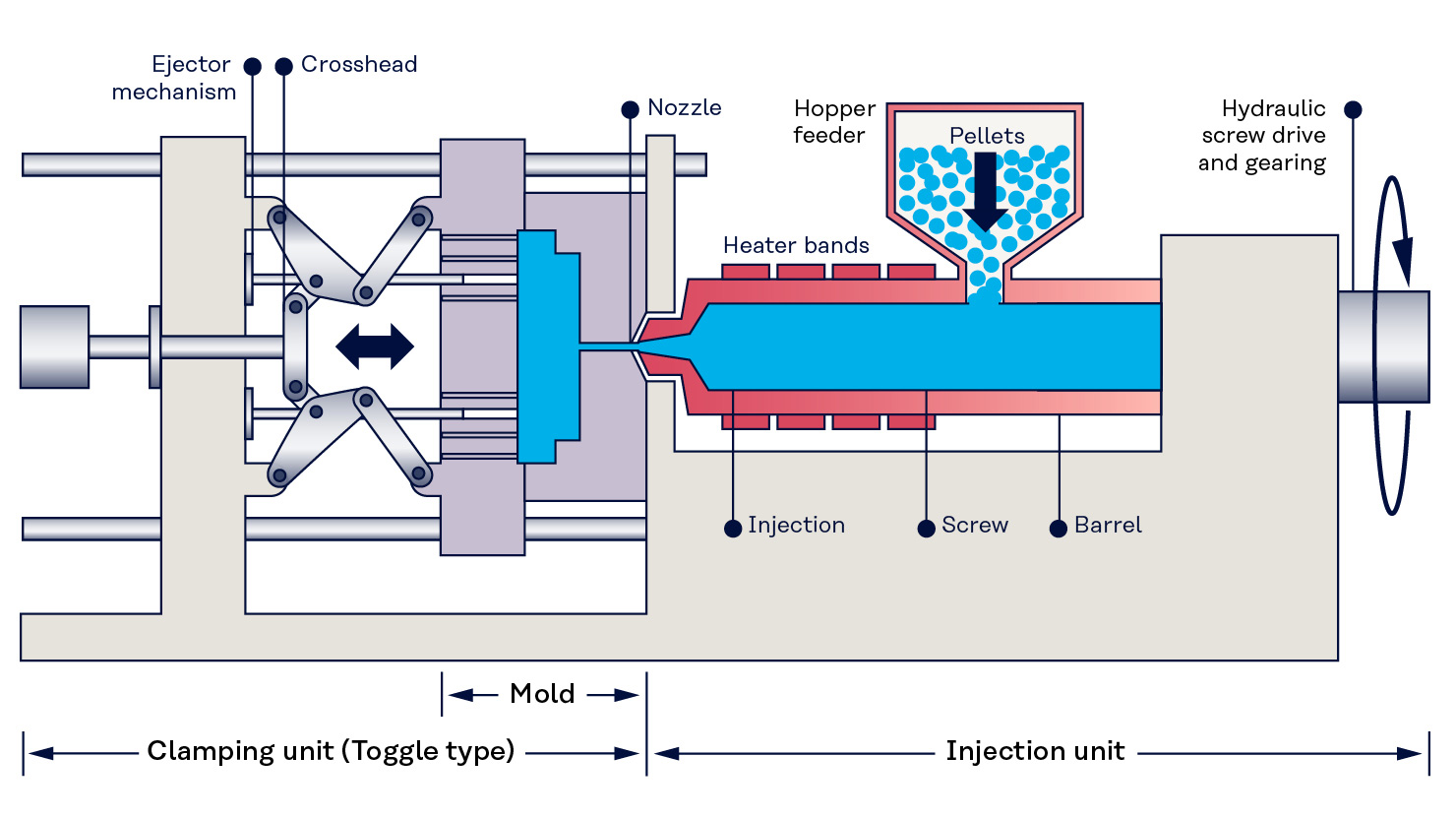
Força de fechamento
A força de fixação pode variar de algumas toneladas a milhares de toneladas. Devido a esse amplo espectro, as prensas são comumente classificadas por sua tonelagem, que indica a força de fixação que a máquina pode exercer. A tonelagem necessária para moldar uma peça específica depende da sua área projetada.
A regra geral é de aproximadamente 5 toneladas por polegada quadrada para a maioria dos produtos. No entanto, há exceções para materiais plásticos muito rígidos, que exigem uma pressão de injeção e força de fechamento mais altas para manter o molde fechado. Peças maiores também requerem uma força de fechamento maior.
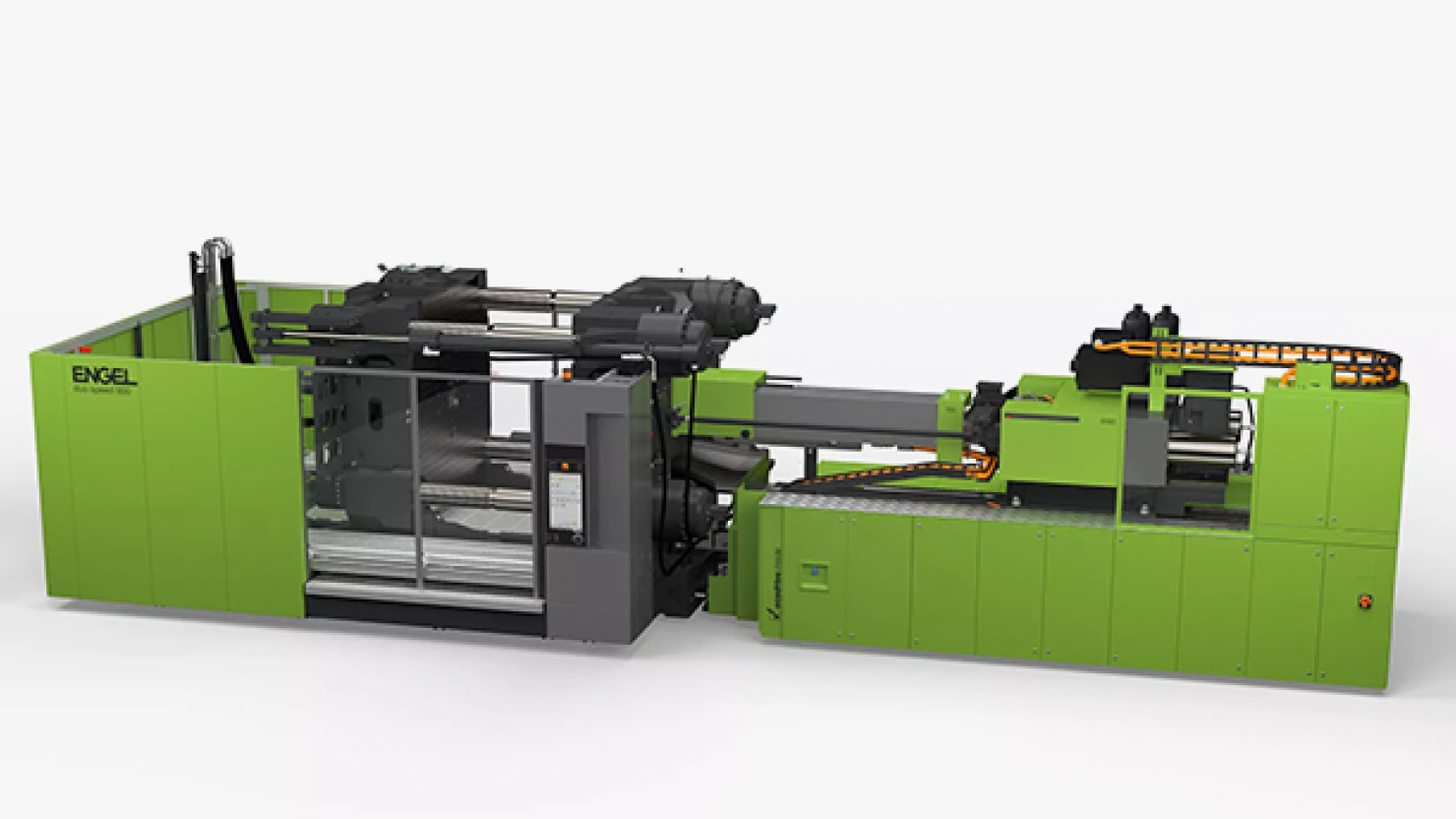
Molde
O molde, às vezes chamado simplesmente de “ferramenta”, é o coração de todo o processo. Trata-se de um bloco metálico oco no qual o plástico fundido é injetado para criar a forma desejada. O molde possui vários furos para controle de temperatura e ventilação. A temperatura é controlada utilizando água, óleo ou aquecedores.
Na sua forma mais simples, o molde consiste em duas metades:
- A cavidade (a parte frontal) e
- o núcleo (a parte traseira).
Por outro lado, as peças moldadas por injeção geralmente têm dois lados:
- O lado A da peça, normalmente o que apresenta melhor acabemento superficial, que fica voltado para a cavidade.
- O lado B, também chamado de lado funcional, geralmente contém os elementos estruturais ocultos da peça. Sua superfície é, portanto, muitas vezes áspera e apresenta marcas dos pinos ejetores.
O plástico fundido flui através de um canal de injeção para o molde e preenche suas cavidades. Após o resfriamento e solidificação, que normalmente correspondem a cerca de metade do ciclo de moldagem por injeção, o molde é aberto e as peças moldadas são ejetadas.
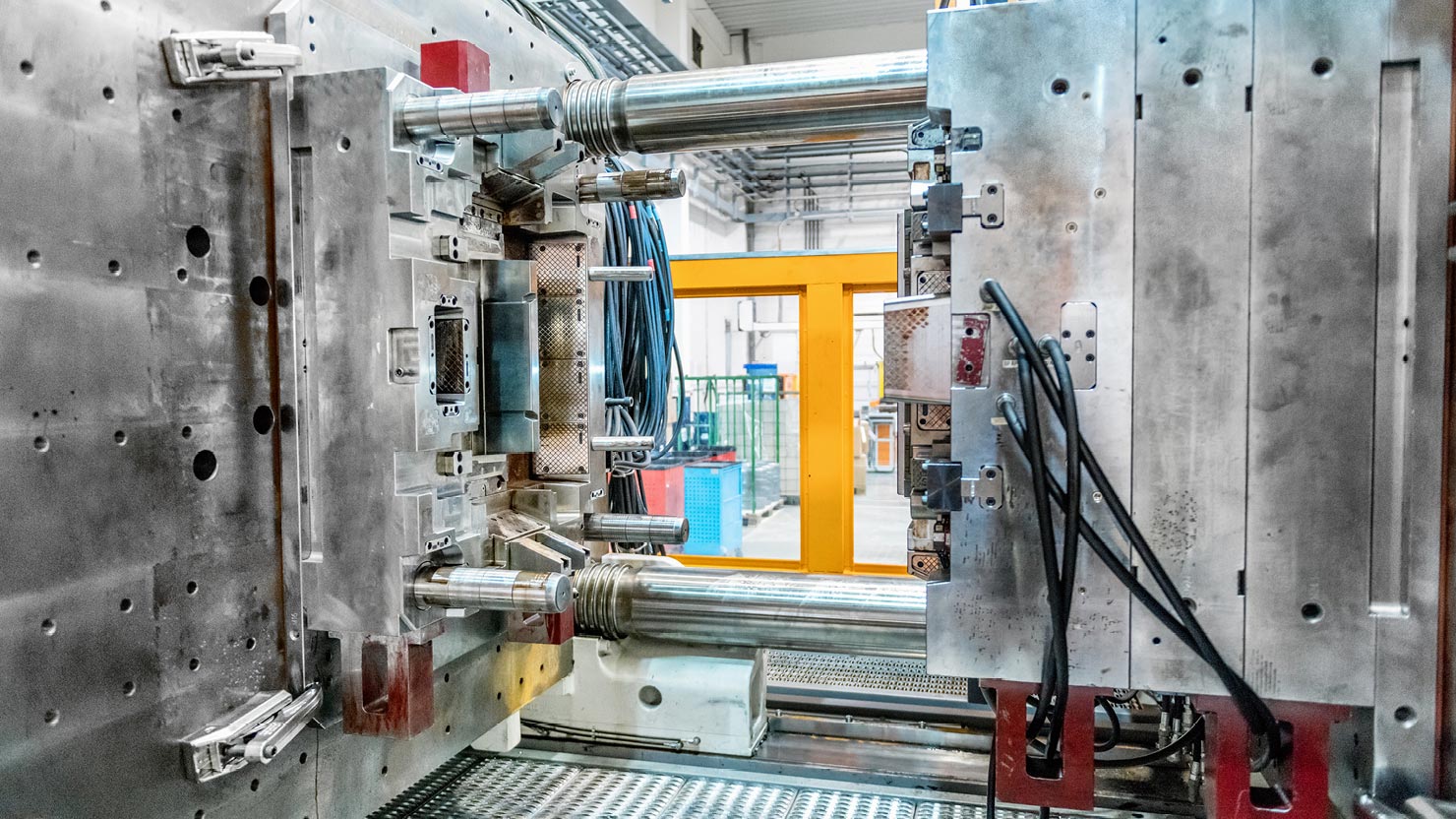
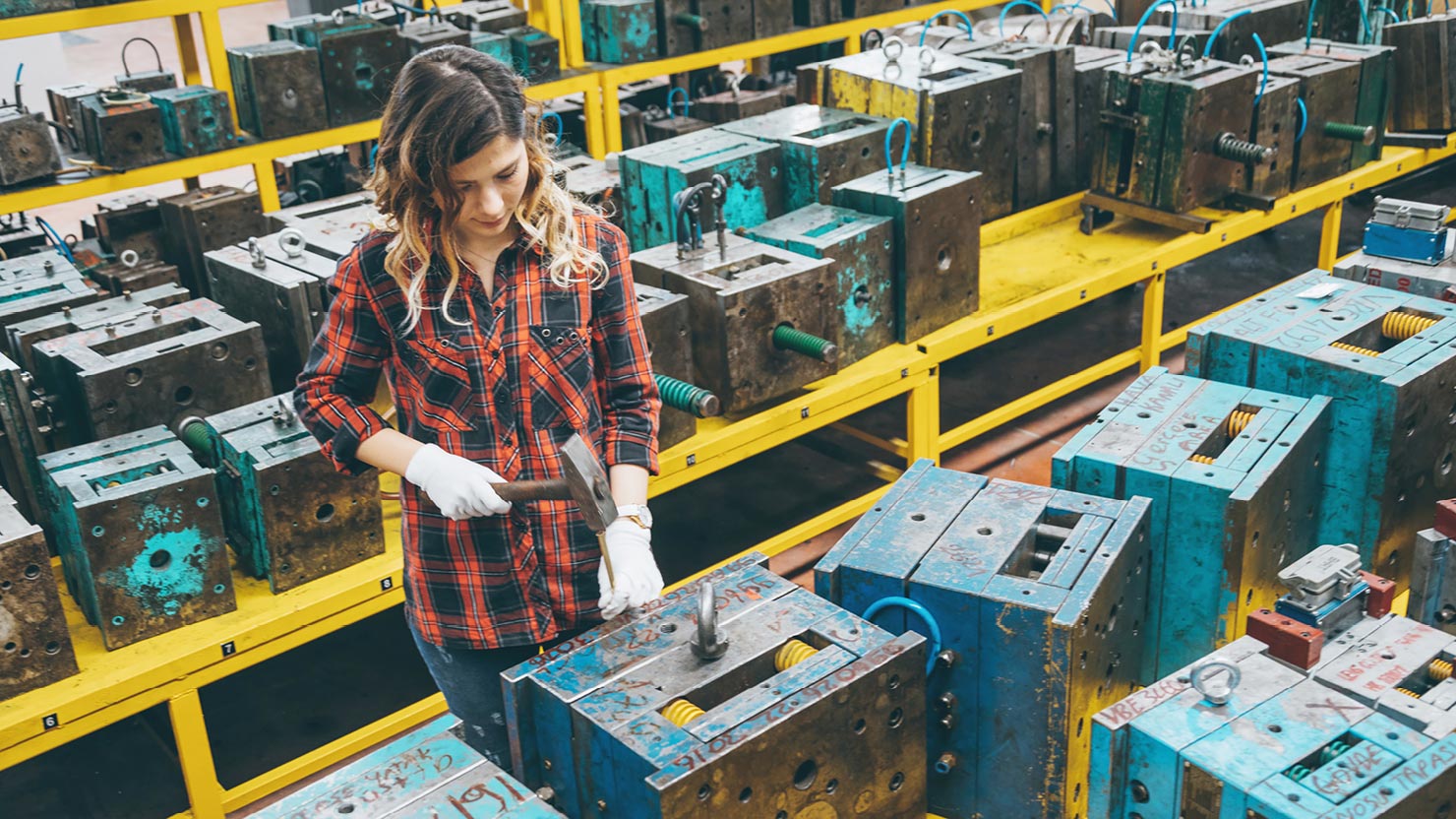
Bom saber
Os moldes são caros de fabricar e, por esse motivo, são utilizados para produção em massa de milhares a milhões de peças. Eles são normalmente feitos de aço temperado ou pré-temperado, mas também podem ser feitos de alumínio e/ou liga de cobre-berílio.
Material do molde
Os moldes de aço são mais caros de produzir, mas também duram mais. Se um grande número de peças puder ser produzido, o custo do molde de aço pode justificar o custo adicional. Os moldes de aço temperado são superiores em resistência ao desgaste e durabilidade. Já os moldes de aço pré-temperado são menos resistentes ao desgaste e são utilizados para quantidades menores ou peças de maior tamanho.
Os moldes de alumínio, que são mais baratos, podem ser econômicos para a fabricação de dezenas ou até centenas de milhares de peças. A liga de cobre-berílio é usada onde é necessária uma rápida dissipação de calor ou onde há alto calor por cisalhamento.
Projeto de molde
O molde pode ser comparado ao negativo de uma foto, onde a estrutura superficial e a geometria do molde são transferidas para a peça final. Ele também inclui características como o sistema de canais para o fluxo do material e canais de resfriamento interno.
Para produzir milhares ou mesmo milhões de peças com precisão e repetibilidade, os fabricantes de moldes precisam de uma enorme experiência. Isso ocorre porque um molde pode ser muito complexo com diversas considerações, como espessura da parede, cantos, nervuras, recortes e roscas. O elevado esforço de desenvolvimento é também a razão pela qual o molde normalmente representa a maior parte dos custos iniciais na moldagem por injeção.
O custo dos moldes pode variar muito: Moldes simples com geometrias básica para produções de pequena escala, são relativamente fáceis de desenvolver e custam alguns milhares de dólares. Moldes mais avançados para produções de grande escala e com geometrias complexas têm um custo muito mais elevado, pois exigem núcleos retráteis ou inserts. Esses elementos móveis são inseridos no molde de cima ou de baixo para produzir peças com saliências, como uma abertura ou cavidade.
O projeto do molde geralmente é feito internamente por fabricantes de máquinas ou empresas especializadas e requer consideração de matérias-primas e o uso de análise de elementos finitos. Os fabricantes de moldes, ou fabricantes de ferramentas, fabricam os moldes de metal, geralmente aço ou alumínio, e usinam precisamente em CNC para modelar as características desejadas. Avanços recentes em materiais para impressão 3D permitem a produção de moldes para lotes menores a um custo mais baixo em comparação com métodos tradicionais.
O sistema de canais, também conhecido como sistema de alimentação, controla o fluxo e a pressão, canalizando o plástico fundido para dentro do molde. O plástico fundido percorre os seguintes canais ao entrar no molde:
- O canal principal (ou bucha de injeção)
- o canal de alimentação principal,
- o canal de alimentação sedundário e
- o ponto de injeção ou entrada, que é o canal estreito entre o canal secundário e a cavidade do molde.
Além disso, um poço frio comumente coleta o fluxo de material frio no processo de moldagem por injeção para evitar bloqueio no canal secundário ou entrada, permitindo que o material quente restante flua para a cavidade do molde sem complicações.
A produção de múltiplas peças frequentemente requer múltiplos canais de injeção (sprues). Os sistemas de canais são separados das peças após a ejeção. A moldagem por injeção é um método de fabricação com baixo desperdício, sendo os sistemas de canais o único material desperdiçado. Parte desse resíduo pode até ser reciclada ou reutilizada, dependendo do material.
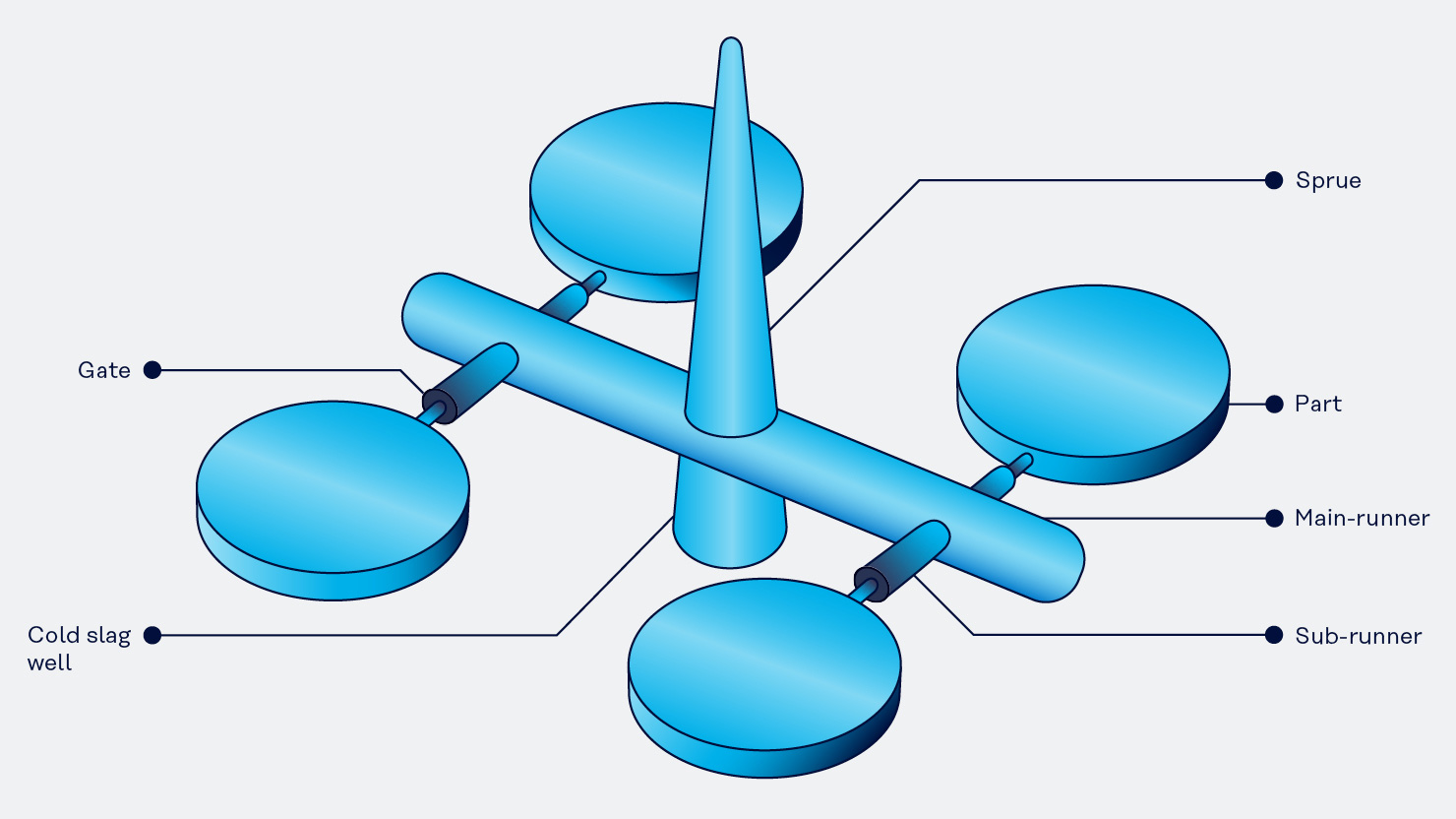
Os fabricantes de moldes podem escolher entre vários tipos de canais de entrada (gates), considerando fatores como orientação da peça (lado A vs. lado B), facilidade de produção do molde, seleção de material, fluxo do material, tamanho da peça, comportamento de corte e custo do refugo. Para obter mais informações, consulte o guia de injeção para moldagem por injeção da Basilius.
Os moldes também incluem um sistema de fechamento com duas finalidades principais:
- Mantenha as duas partes do molde firmemente fechadas durante a injeção
- Empurrar a peça moldada para fora do molde após a abertura.
A peça ejetada cai em uma esteira transportadora ou em um contêiner e é armazenada ou montada.
Devido ao fato de que as diversas partes móveis do molde nunca podem ser 100% alinhadas, dois defeitos podem ser vistos em quase todas as peças moldadas por injeção:
- Linhas de separação, que são visíveis onde as duas metades do molde se encontram
- Marcas do ejetor, que são causadas pelos pinos ejetores.
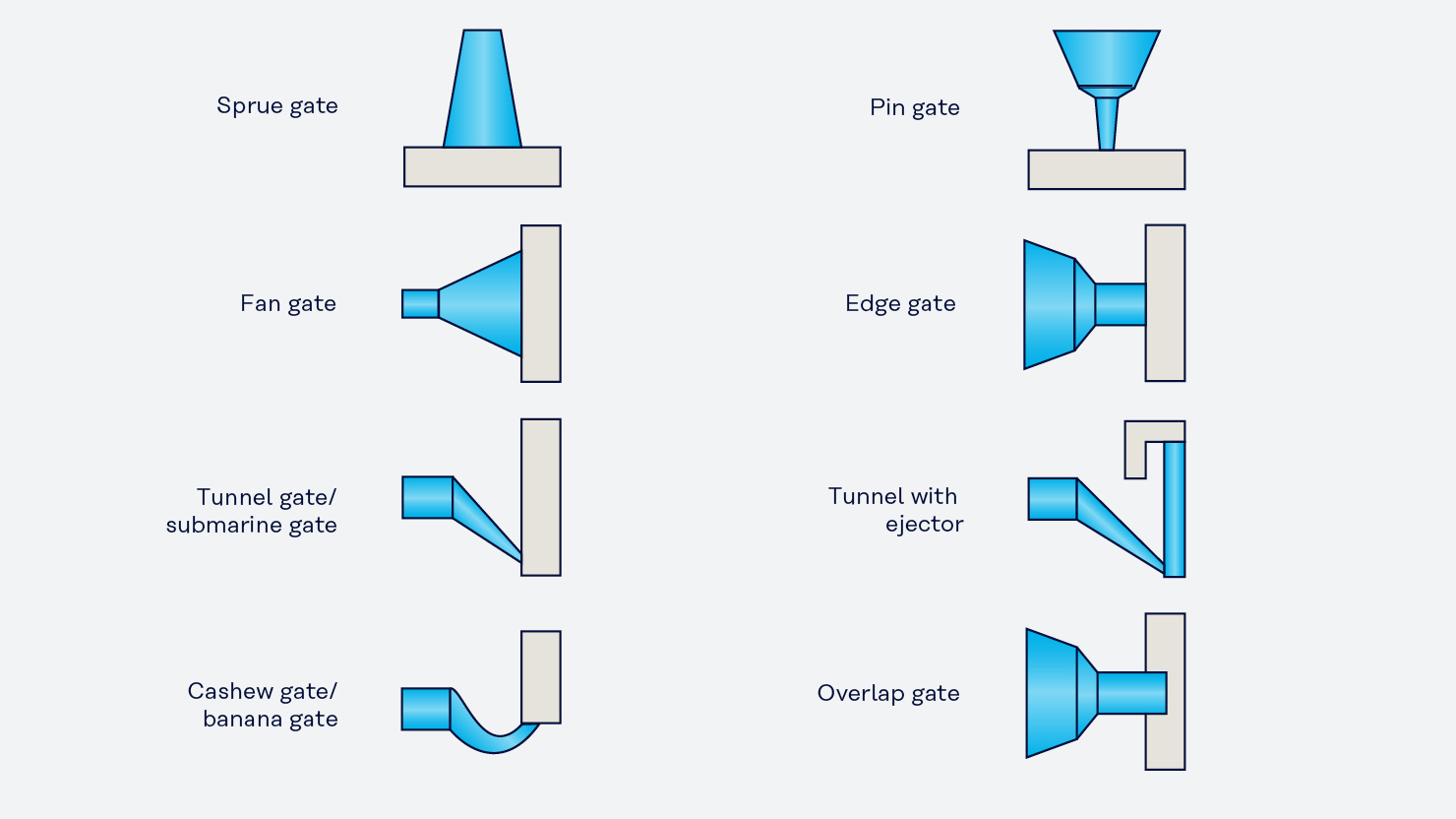
Moldagem
O termo “moldagem” refere-se ao material que preenche o canal de entrada, o poço frio, os canais de distribuição, os canais de entrada e a seção da cavidade do molde que forma as peças, tudo combinado.
Dependendo do material, o conteúdo dos canais de injeção, poços frio, canais de distribuição e canais de entrada pode ser descartado ou moído e reutilizado em outro ciclo de moldagem por injeção.
Características do processo
O ciclo do processo para moldagem por injeção é muito curto e leva entre alguns segundos e dois minutos, dependendo do tamanho da peça. O processo pode ser dividido em quatro etapas principais: Fixação, injeção, resfriamento e ejeção.
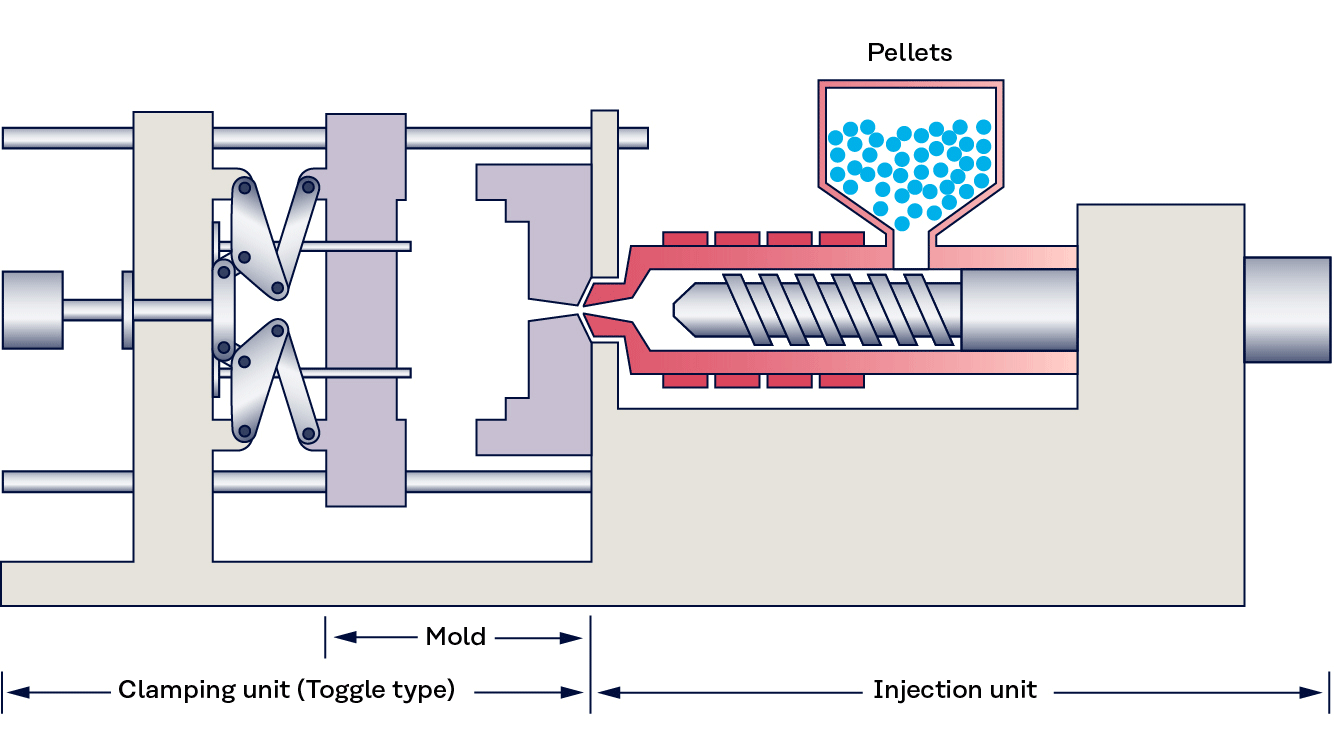
Etapa 1: Fechamento
Antes que o material seja injetado no molde, as duas metades do molde devem ser fechadas com segurança pela unidade de fechamento. A unidade de fechamento pressiona firmemente as metades do molde enquanto o material é injetado. Máquinas maiores com forças de fechamento mais altas exigem mais tempo para fechar.
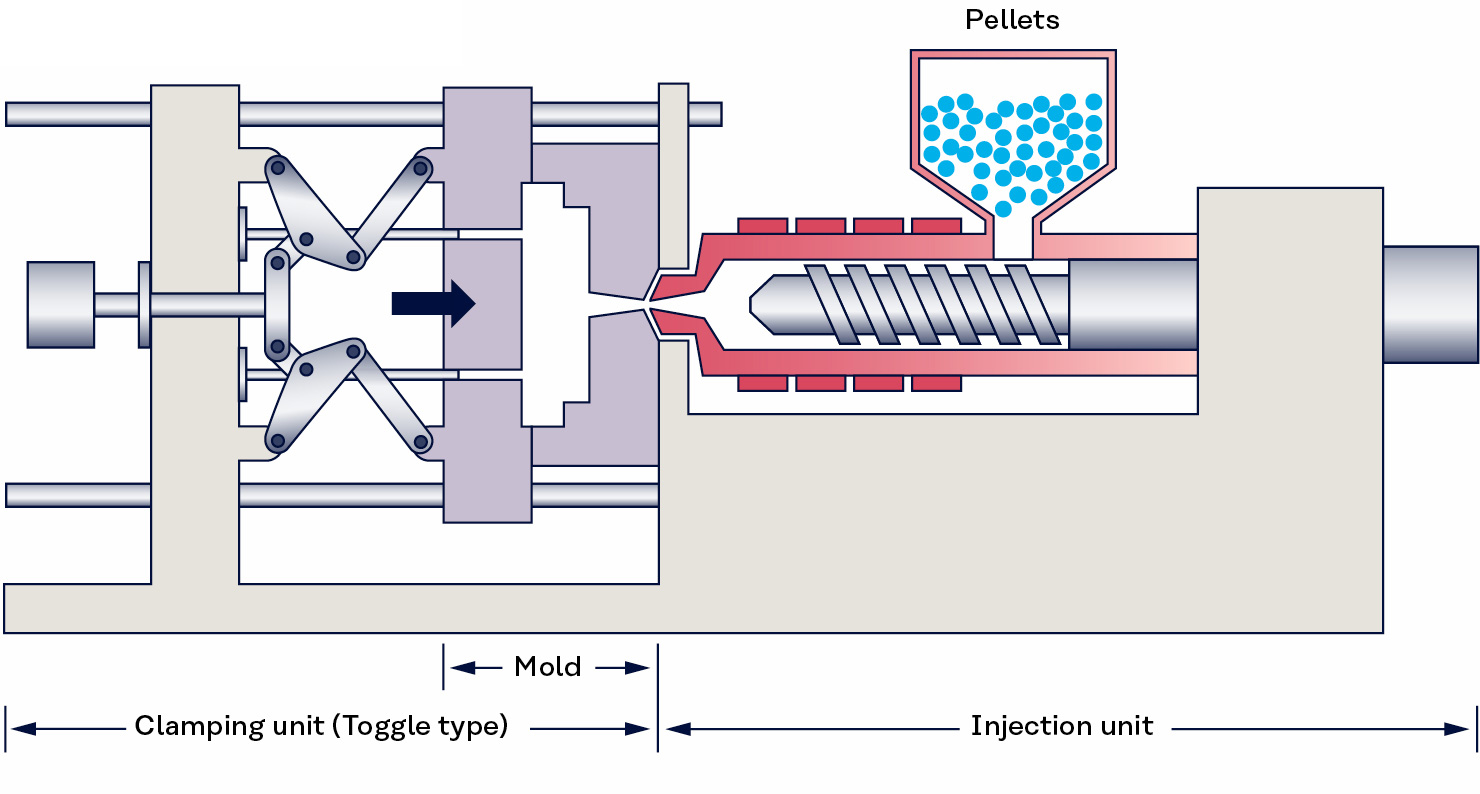
Etapa 2: Injeção
A matéria-prima, geralmente grânulos de plástico, é transportada da unidade de injeção para o molde, sendo derretida por calor e pressão. O plástico fundido, conhecido como “shot”, é então injetado através do sistema de canais de injeção no molde, preenchendo toda a cavidade.
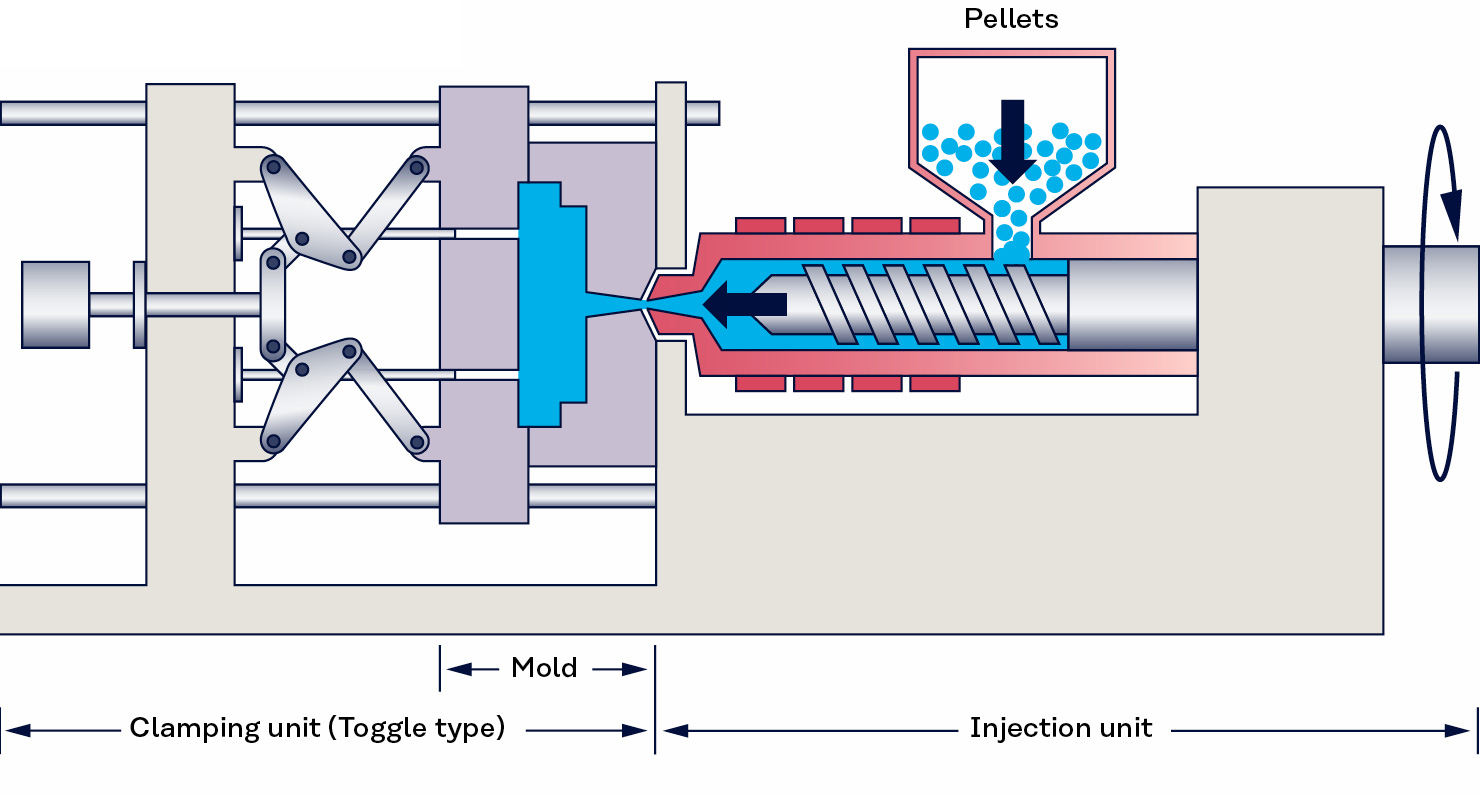
Etapa 3: Resfriamento
Dentro do molde, o plástico fundido começa a resfriar assim que entra em contato com as superfícies internas do molde. À medida que o material resfria, ele se solidifica novamente e assume a forma desejada. O molde permanece fechado até que o tempo necessário de resfriamento tenha sido alcançado.
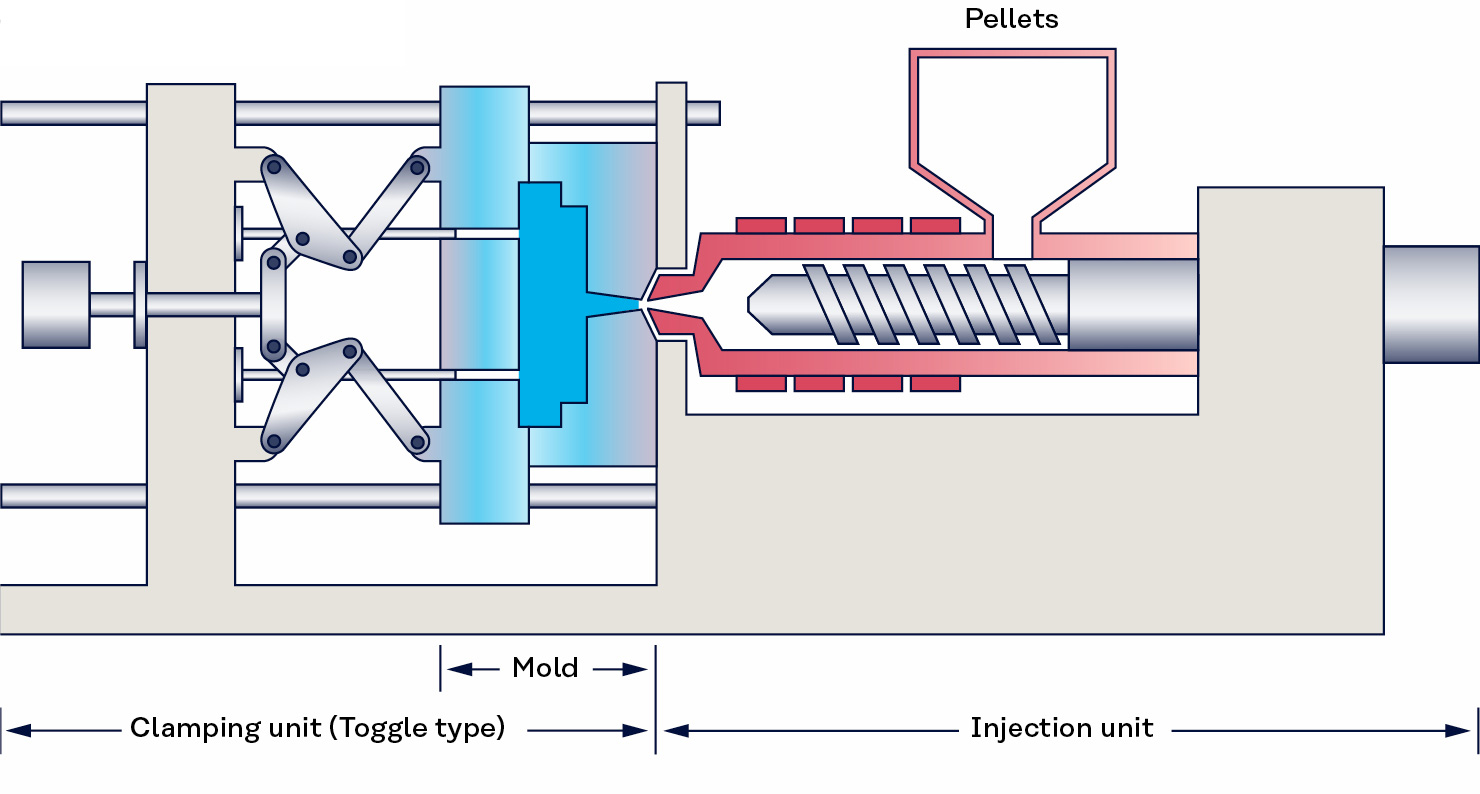
Etapa 4: Ejeção
A peça resfriada é ejetada do molde usando o sistema de ejetores: Quando o molde é aberto, a peça moldada é empurrada para fora do molde por um mecanismo. Dependendo do design do canal de entrada, a peça é separada automaticamente do restante da moldagem ou por corte.
Após a ejeção, uma esteira transportadora move a peça moldada para armazenamento, montagem ou pós-processamento. Simultaneamente, o molde é fechado novamente para o próximo ciclo, e o processo de moldagem por injeção se repete. Em alguns casos, as peças moldadas por injeção estão prontas para uso imediato, enquanto outras requerem diferentes graus de pós-processamento.
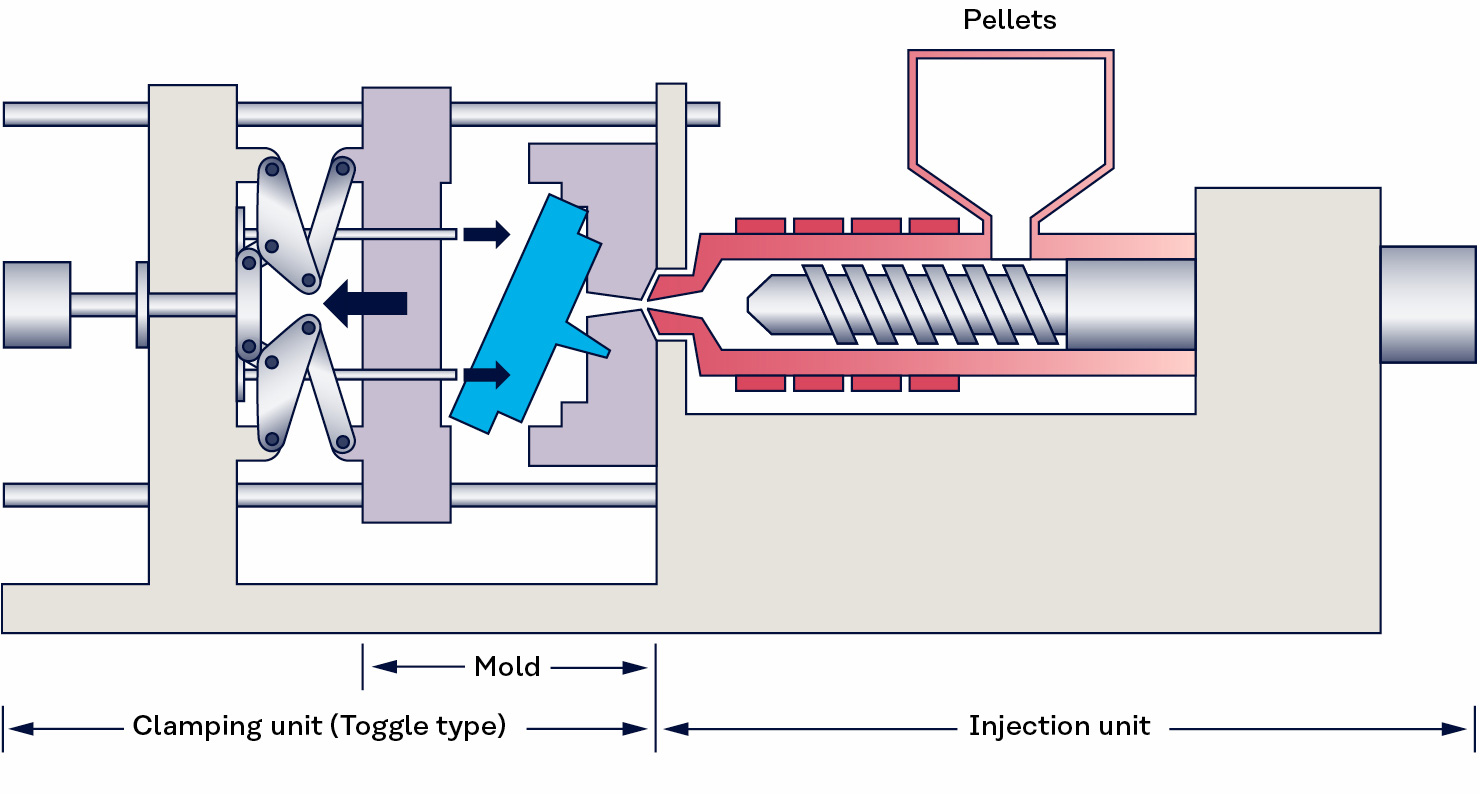
Tipos de moldagem por injeção
Moldagem por injeção tradicional vs. desacoplada
Na moldagem por injeção tradicional, a injeção é realizada a uma pressão constante para preencher e comprimir a cavidade do molde. No entanto, isso pode resultar em variações significativas nas dimensões das peças de um ciclo para o outro.
Na moldagem por injeção desacoplada, o processo de injeção é dividido em duas etapas para maior controle das dimensões das peças e consistência de ciclo a ciclo:
- Preencher a cavidade em cerca de 98% usando controle de velocidade
- Preencher os 2% restantes usando o controle de pressão.
A moldagem por injeção desacoplada também é chamada de moldagem por injeção científica.
Moldagem por injeção monocomponente e multicomponente
Na moldagem por injeção de plásticos, é feita uma distinção entre moldagem por injeção de componente único e moldagem por injeção de múltiplos componentes. Dependendo do número de materiais utilizados, a moldagem por injeção multicomponentes é diferenciada em moldagem 2K, 3K, etc.
O termo 2K refere-se à moldagem por injeção de dois componentes, onde um material macio (ex.: TPE) é moldado ao redor de um material duro (ex.: PP). O 3K é semelhante ao 2K, mas com uma camada ou componente extra.
Possíveis defeitos
Vários defeitos podem ocorrer no processo de moldagem por injeção: defeitos dependentes da máquina, do material ou de ambos.
A seção a seguir tenta categorizar os defeitos e apresentar alguns exemplos. Na prática, há tantas causas possíveis para defeitos em peças moldadas que seria irreal descrever todas em um artigo escrito.
Defeitos dependentes do equipamento
Os defeitos dependentes do equipamento são causados por razões técnicas. Por exemplo, o excesso de material fundido pode escapar do molde se a pressão de injeção for muito alta ou a força de fechamento do molde for muito baixa, um defeito conhecido como rebarba ou flash.
O resfriamento desigual pode fazer com que as peças se deformem. Se o design do molde ou o processo de moldagem não considerarem corretamente a contração que normalmente ocorre durante o resfriamento, as peças podem empenar.
Bolhas nas peças moldadas aparecem quando o molde ou o material estão muito quentes. Esse defeito geralmente está relacionado à máquina e é causado pela falta de resfriamento ao redor do molde ou por um aquecedor que não funciona conforme esperado.
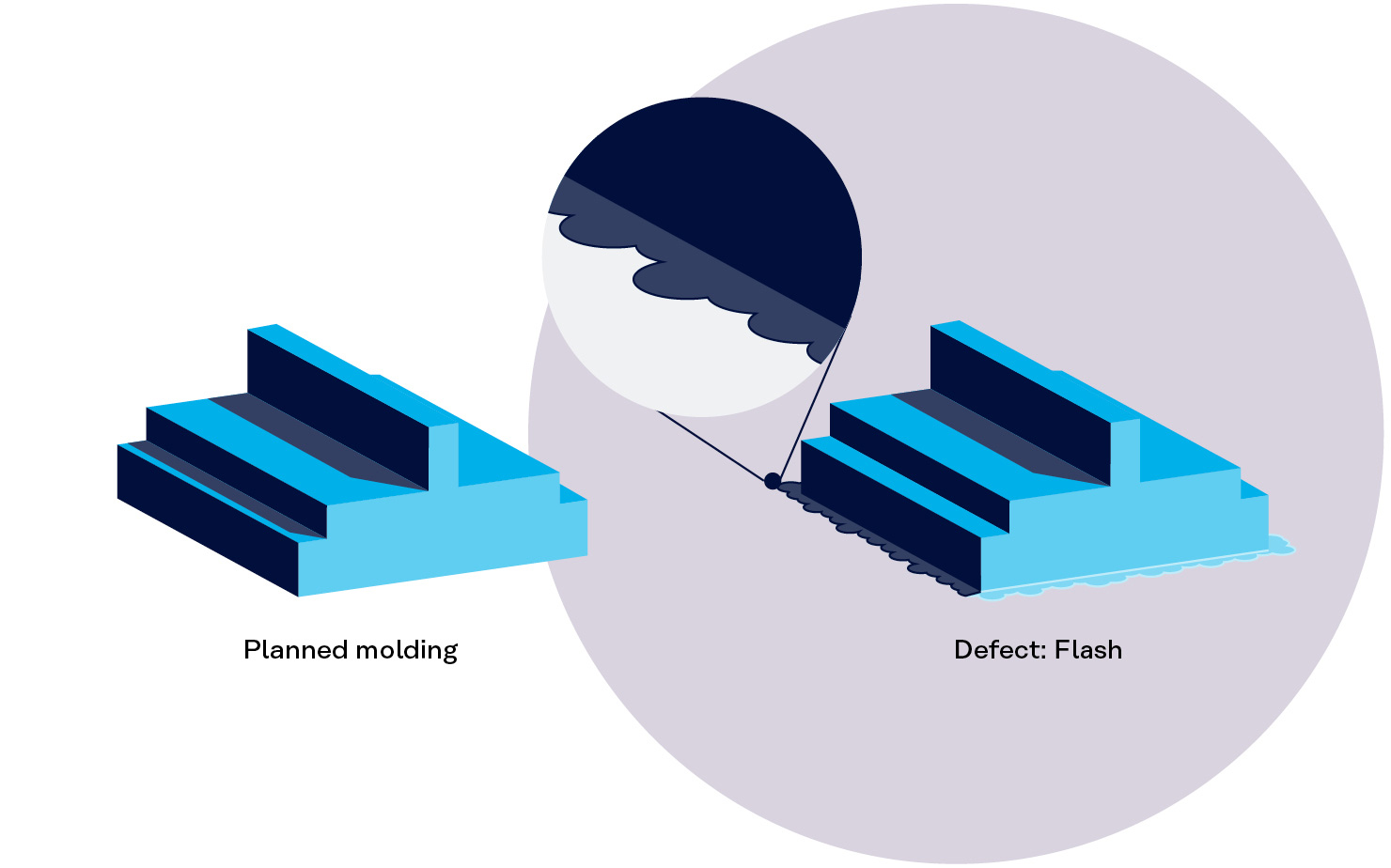
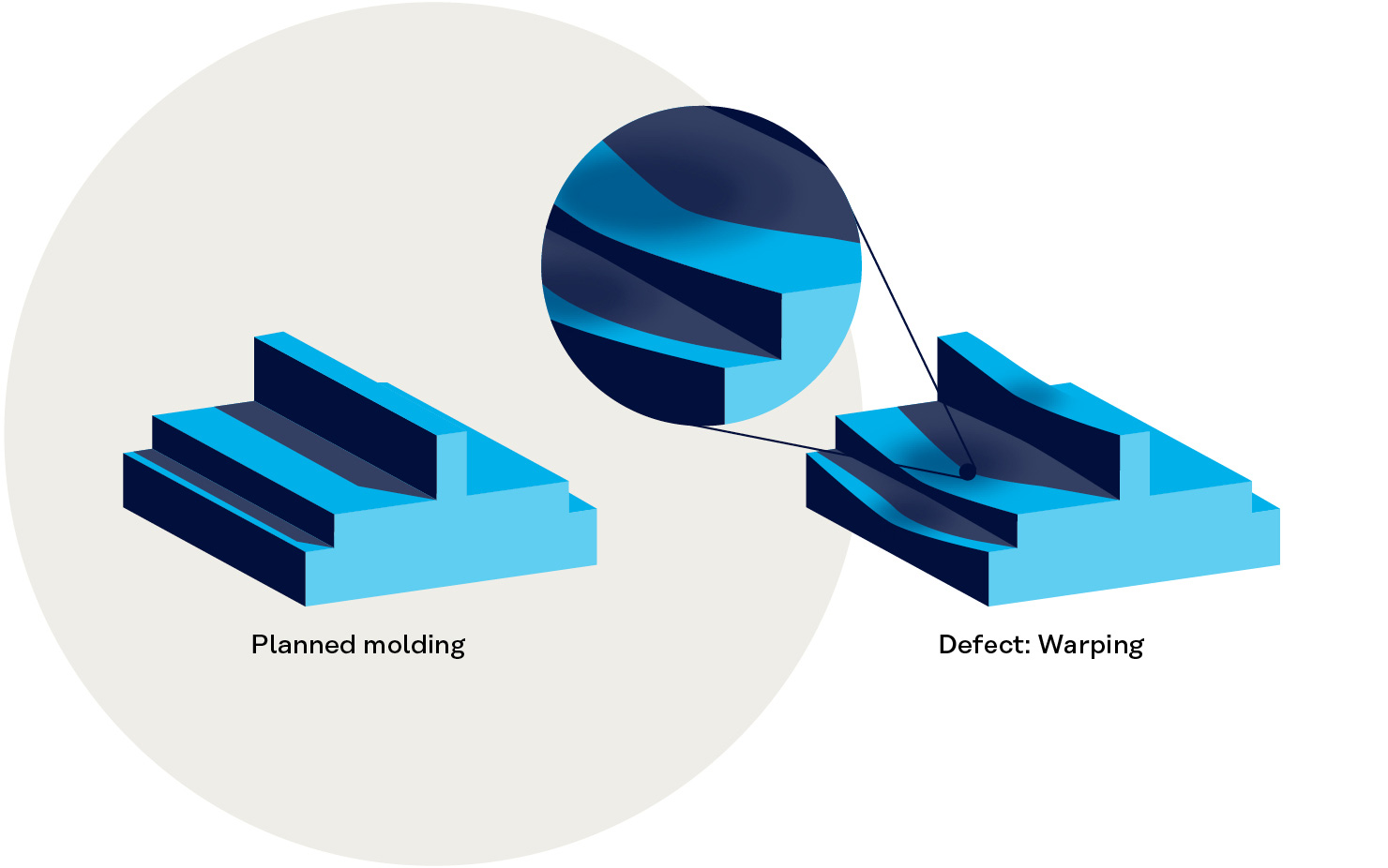
Defeitos dependentes de material
A degradação do polímero é um exemplo de defeito dependente do material. Se o material passou por hidrólise, oxidação ou outra causa de degradação do polímero, as peças moldadas podem apresentar rachaduras, descoloração ou defeitos semelhantes.
Outro defeito dependente do material são as falhas de preenchimento (short shots). Se não houver material suficiente na máquina de moldagem por injeção, a peça moldada terá seções não preenchidas. Alternativamente, isso também pode ser causado por uma taxa de fluxo insuficiente.
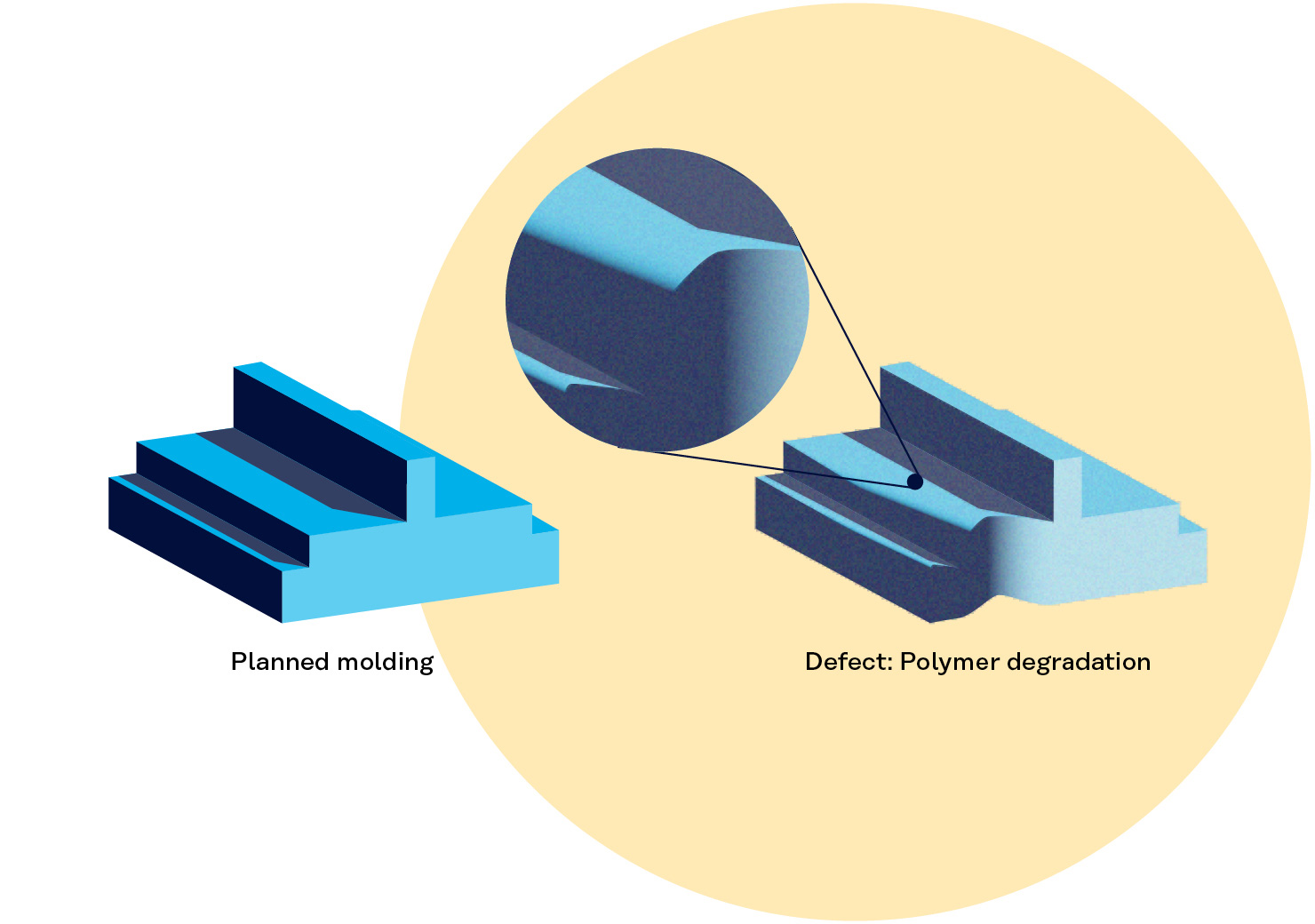
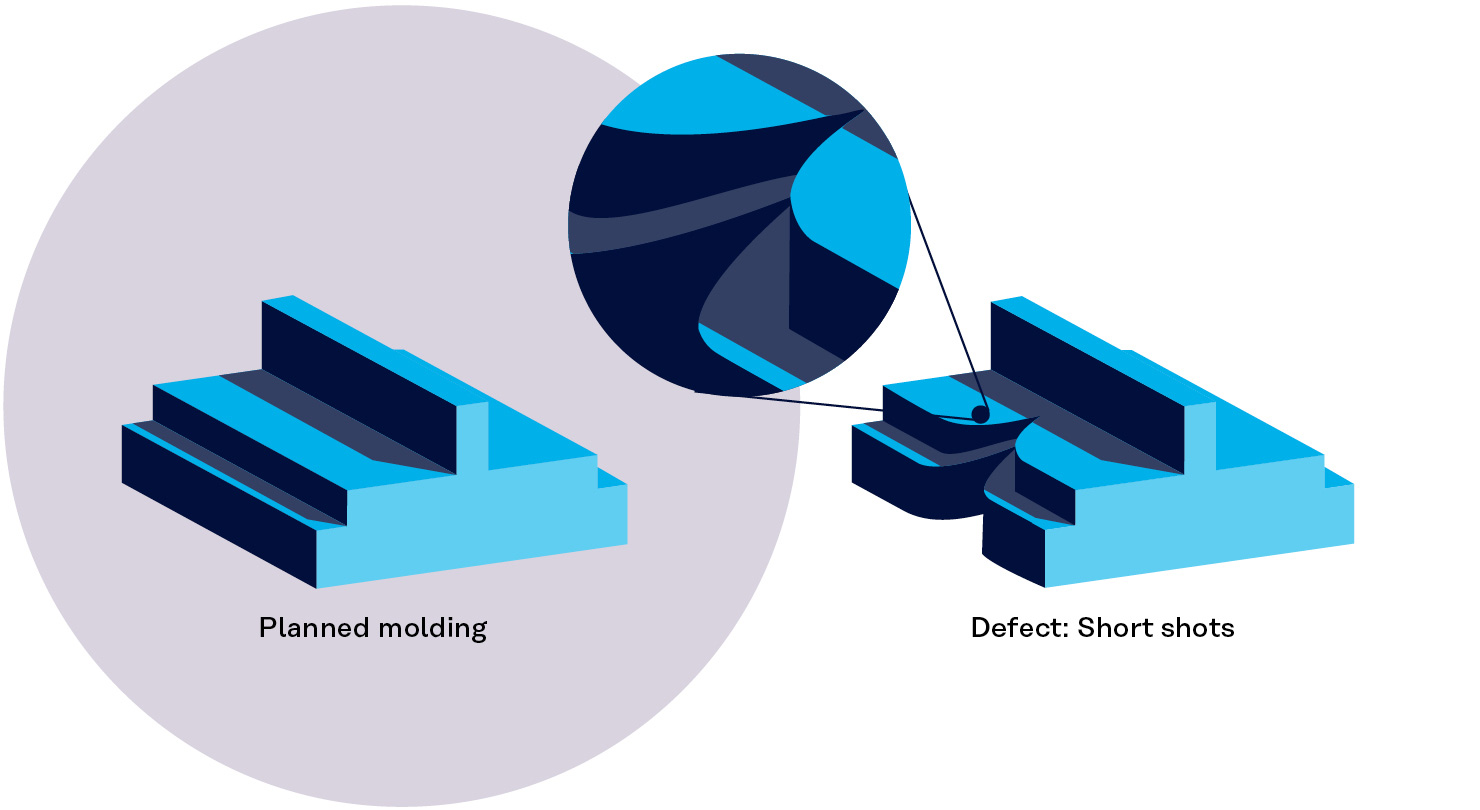
Defeitos dependentes de equipamentos e materiais
Como o equipamento e o material afetam um ao outro, é comum que ocorram defeitos causados por ambos. Por exemplo, as marcas de contração podem ser um defeito dependente do equipamento se a taxa de resfriamento for muito alta, fazendo com que a superfície da peça solidifique antes que o material no centro tenha tempo de fluir corretamente. Alternativamente, elas podem ser um defeito relacionado ao material, uma vez que alguns materiais, como resinas com cargas ou reforçadas, têm uma maior tendência a encolher e exibir marcas de contração.
Exemplos de defeitos relacionados ao equipamento que causam marcas do ejetor são projeto inadequado do molde (especialmente em relação aos canais de entrada), posicionamento inadequado dos pinos ejetores ou manutenção inadequada do molde. Por outro lado, defeitos relacionados ao material, como fragilidade ou baixa resistência ao impacto, também podem causar marcas no ejetor.
Novamente, esta lista de defeitos e suas razões está incompleta. Estamos apenas apresentando alguns exemplos.
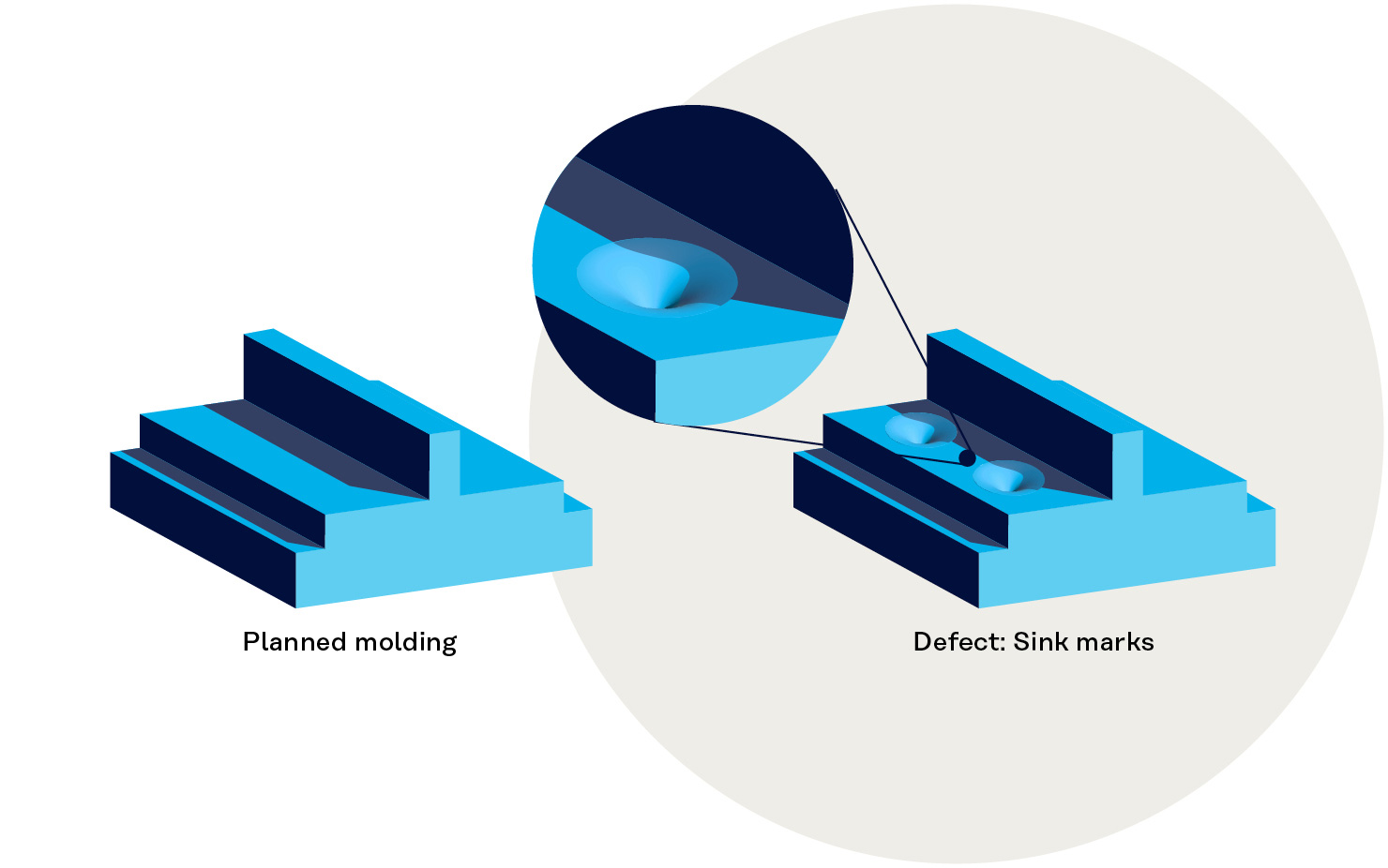
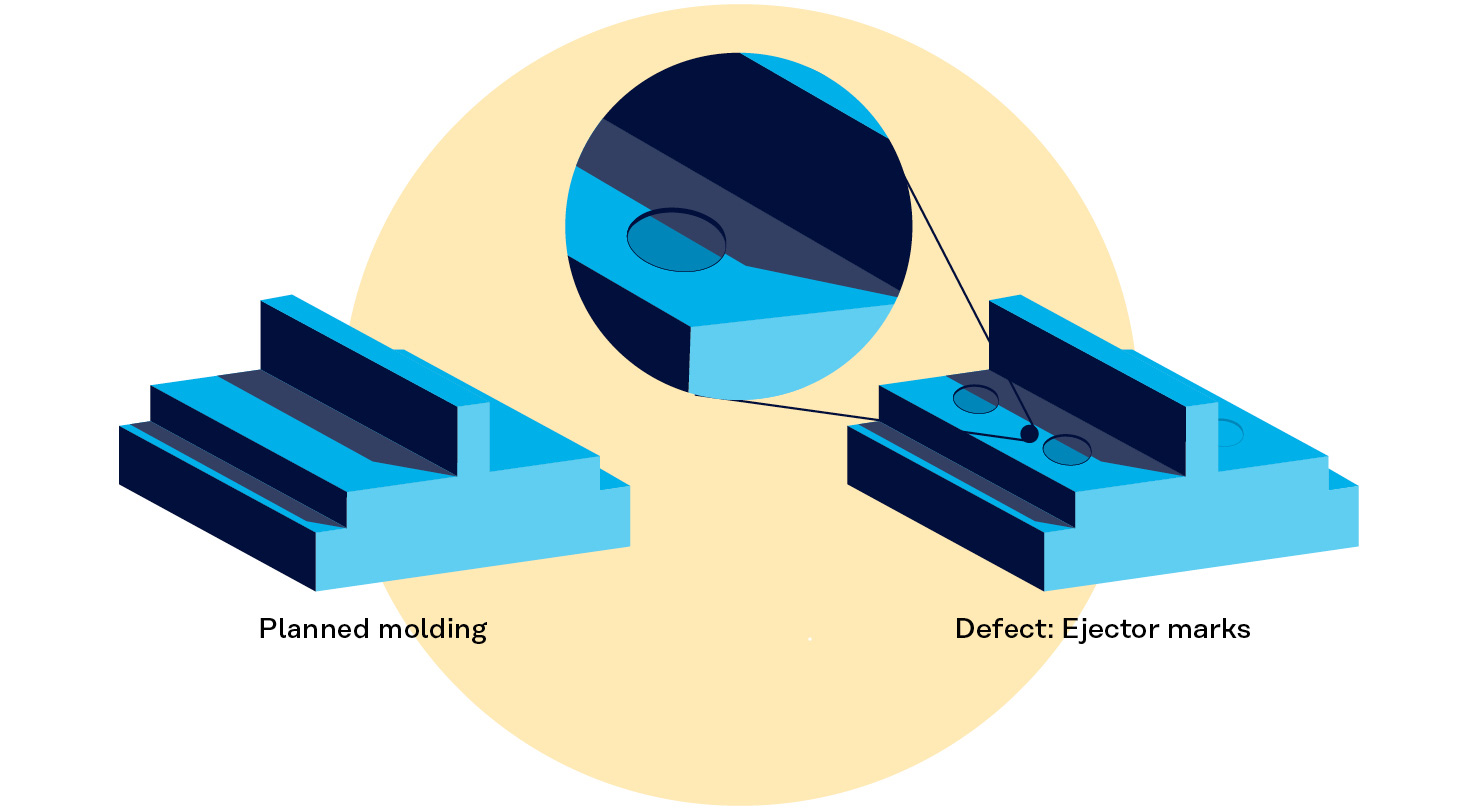
Bom saber
As matérias-primas da Kuraray são excelentes aditivos que podem ajudar a reduzir defeitos nas peças moldadas na moldagem por injeção. Eles podem melhorar propriedades importantes do material, como fluxo e retração.
Materiais para moldagem por injeção
Todos os termoplásticos, bem como alguns termofixos e elastômeros são materiais adequados para moldagem por injeção.
Os termoplásticos mais frequentemente utilizados na moldagem por injeção em todo o mundo são o polipropileno (PP), o acrilonitrila butadieno estireno (ABS), o polietileno (PE) e o poliestireno (PS).
Como “materiais macios” para moldagem por injeção 2K e 3K, os elastômeros termoplásticos (TPEs) são os mais comumente processados.
É bastante incomum que termofixos sejam usados em moldagem por injeção. Isto se deve à sua densidade de reticulação e à incapacidade de serem fundidos e remodelados. No entanto, alguns termofixos são usados como aditivos em certas aplicações, como para melhorar as propriedades de peças termoplásticas.
Os materiais estão geralmente disponíveis em pequenos pellets ou em pó fino. Em alguns casos, eles são líquidos. Ao adicionar vários aditivos, as propriedades das peças moldadas ou a processabilidade do material podem ser aprimoradas. Exemplos de aditivos incluem corantes para coloração ou fibra de vidro para maior rigidez. No entanto, também existem aditivos mais avançados, como os elastômeros especiais da Kuraray.
Cada material requer diferentes parâmetros durante o processamento para obter as peças moldadas desejadas. Estes incluem a temperatura e pressão de injeção, a temperatura do molde, bem como o tempo de ciclo. Dependendo de como esses parâmetros são definidos, a aparência, as dimensões e as propriedades mecânicas das peças moldadas mudam consideravelmente. Além da tecnologia apropriada, é necessário um grande conhecimento prático.
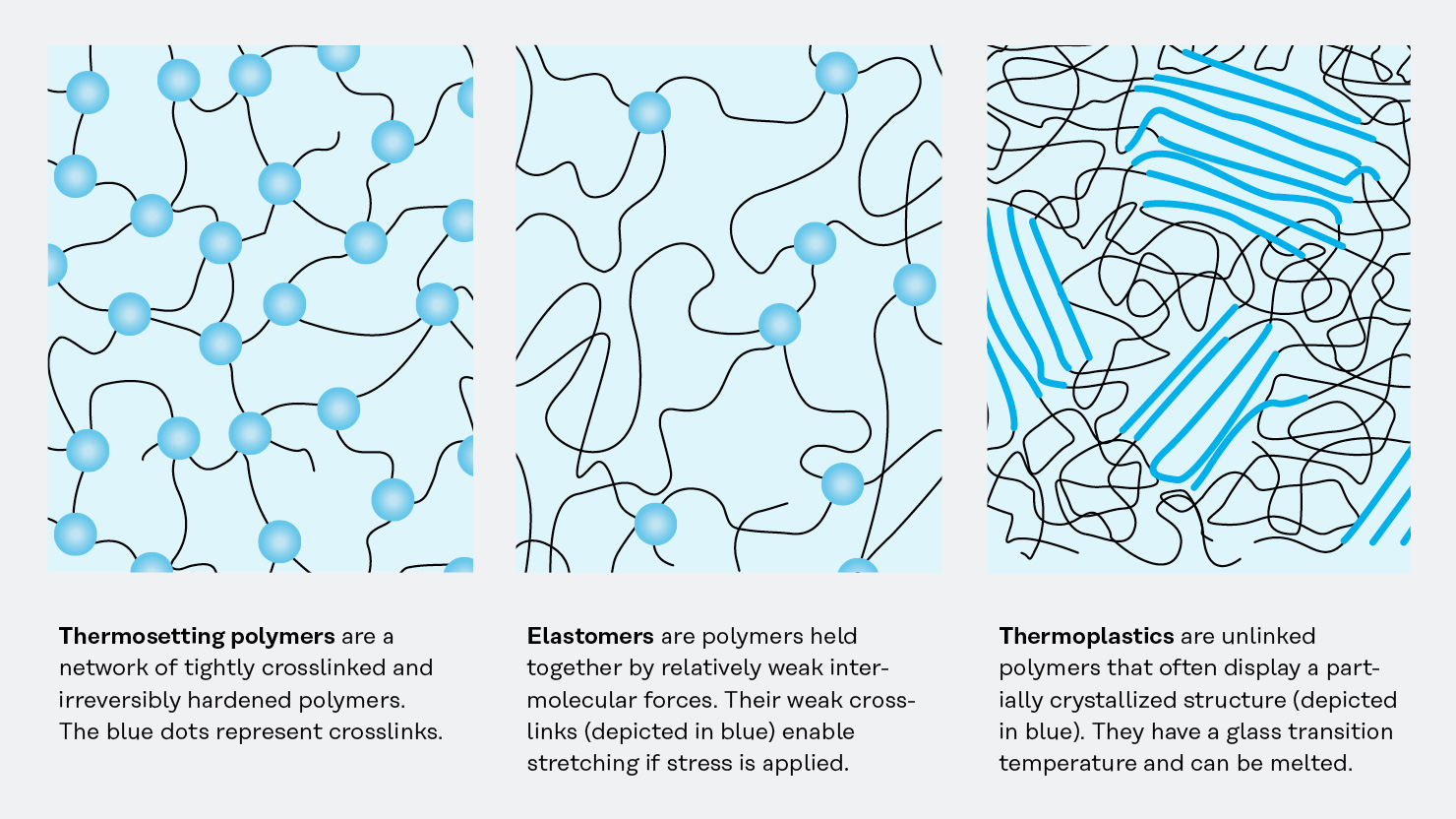
Elastômeros termoplásticos
Os elastômeros termoplásticos (TPEs) são materiais que combinam a elasticidade semelhante à da borracha com a processabilidade dos termoplásticos. Em outras palavras, eles podem ser esticados como um elástico e fundidos e moldados em uma ampla variedade de formas e tamanhos. Após o resfriamento, mantêm sua elasticidade. Se necessário, podem ser novamente fundidos e remodelados posteriormente, o que também implica em menos desperdício de material no processamento.
A processabilidade dos TPEs os torna um excelente material para moldagem por injeção. Ao contrário da borracha, eles não requerem vulcanização, que é um método de processamento demorado. Devido às suas diversas aplicações, são um material adequado para muitas indústrias e finalidades.
Para saber mais sobre as propriedades dos materiais de diferentes tipos de TPEs, consulte a tabela a seguir.
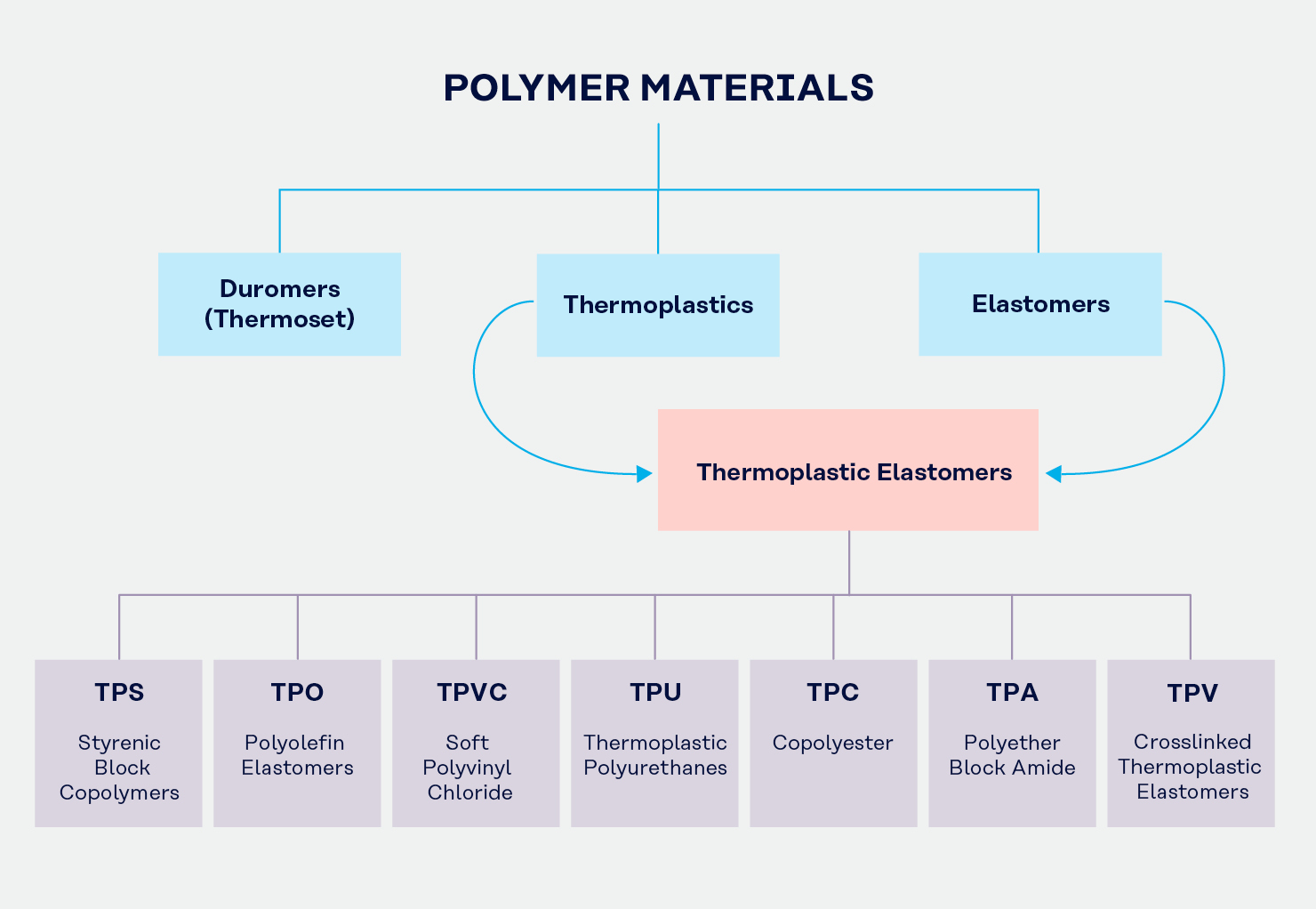
Properties/Materials | TPS | TPO | TPVC | TPU | TPC | TPA |
Shore Hardness | 30A 〜 70A | 60A 〜 95A | 40A 〜 70A | 80A 〜 80D | 90A 〜 70D | 40D 〜 65D |
Tensile strength (MPa) | 9.8 〜 34.3 | 2.9 〜 18.6 | 9.8 〜 19.6 | 29.4 〜 49 | 25.5 〜 39.2 | 11.8 〜 34.3 |
Elongation (%) | 500 〜 1,200 | 200 〜 600 | 400 〜 500 | 300 〜 800 | 350 〜 450 | 200 〜 400 |
Rebound resilience (%) | 45 〜 75 | 40 〜 60 | 30 〜 70 | 30 〜 70 | 60 〜 70 | 60 〜 70 |
Density (g/cm³) | 0.91 〜 0.95 | 0.88 | 1.2 〜 1.3 | 1.1 〜 1.25 | 1.17 〜 1.25 | 1.01 |
Abrasion resistance | Fair | Poor | Fair | Excellent | Fair | Good |
Bending resistance at room temperature | Good | Fair | Good | Good | Excellent | Excellent |
Heat resistance | 〜 80°C | 〜 120°C | 〜 100°C | 〜 100°C | 〜 140°C | 〜 100°C |
Oil resistance | Poor | Fair | Good | Excellent | Excellent | Excellent |
Weather resistance | Poor - good | Good | Fair - good | Fair - good | Fair | Good |
Brittleness temperature | < -70°C | < -70°C | -50°C 〜 -30°C | < -70°C | < -70°C | < -70°C |
Applications | Footwear, resin blends, adhesives, asphalt modification | Automotive hoses / tubes, consumer goods | Automotive, electric wires / cables, civil engineering / construction | Footwear, industrial goods, consumer goods, medical goods | Automobiles, electronics, industrial goods | Sporting goods, industrial goods |
Elastômeros termoplásticos da Kuraray
A Kuraray oferece plásticos de alto desempenho para moldagem por injeção para obter melhores propriedades do material. Seja para peças completas ou como substitutos flexíveis de PVC/borracha, as principais propriedades desses plásticos agregam valor real aos seus produtos e ajudam a tornar seus processos mais eficientes.
Os materiais da Kuraray facilitam a produção eficiente de componentes plásticos em larga escala. Para moldagem por injeção 2K, a Kuraray oferece TPEs de alto desempenho que podem servir como componentes funcionais macios.
SEPTON™
SEPTON™ é uma série de elastômeros termoplásticos estirênicos desenvolvidos pela Kuraray. Os Copolímeros em Bloco de Estireno Hidrogenado (HSBCs) consistem em blocos rígidos à base de estireno e um bloco flexíveis de dieno hidrogenado. Os HSBCs exibem elasticidade semelhante à borracha, uma vez que o bloco rígido atua como um ponto de reticulação abaixo da temperatura de transição vítrea do poliestireno e o bloco flexível fornece elasticidade. A hidrogenação gera excelente resistência ao calor e às intempéries.
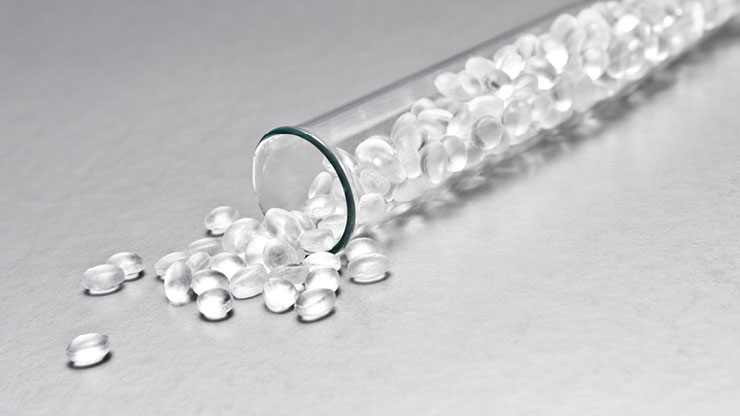
Benefícios
Ao adicionar SEPTON™ e plastificante a poliolefinas, é possível obter boa moldabilidade por injeção e peças moldadas flexíveis.
Ao usar grades SEEPS de SEPTON™, a transferibilidade do relevo é melhorada, assim como a adesão na moldagem por inserção.
SEPTON™ BIO-series
Com a linha SEPTON™ BIO-series, Kuraray oferece um copolímero de bloco de estireno farneseno hidrogenado (HSFC) exclusivo – tornando a Kuraray a primeira e única fabricante de materiais HSBC de origem biológica no mercado. O elastômero termoplástico SEPTON™ BIO-series representa uma nova solução para fabricantes, possibilitando novos compostos e usos finais com alto conteúdo biológico para expandir áreas de mercado existentes e abrir novas.
Para benefícios adicionais, consulte a seção anterior sobre SEPTON™ ou entre em contato com o departamento de vendas.
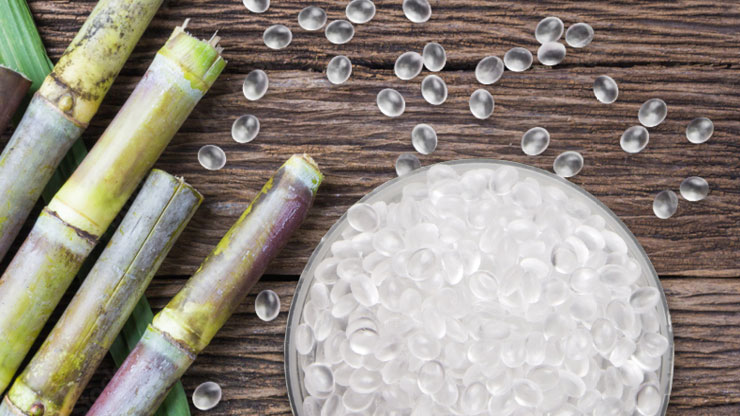
HYBRAR™
HYBRAR™ é um copolímero tribloco verdadeiramente único, composto de blocos terminais de poliestireno e um bloco intermediário de polidieno rico em vinil. Devido ao seu pico tan delta próximo à temperatura ambiente, o HYBRAR™ apresenta altas propriedades de amortecimento de vibração e absorção de choque – mesmo sem plastificante integrado. Esses TPEs estão disponíveis em versões hidrogenados e não hidrogenados.
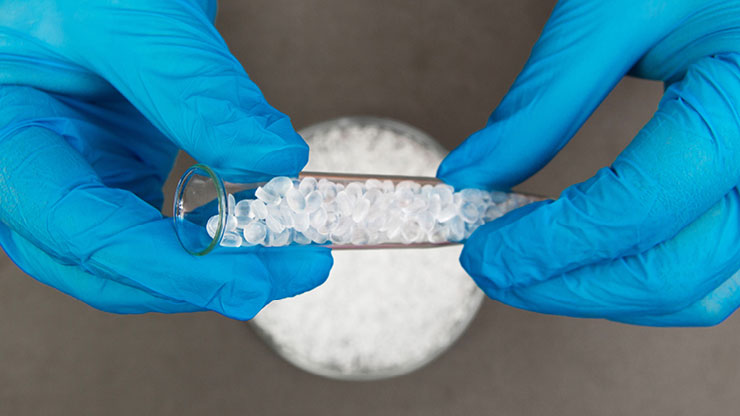
Benefícios
Ao adicionar uma pequena quantidade de HYBRAR™ ao polipropileno, a cristalinidade é reduzida e a transparência pode ser melhorada.
Borrachas líquidas
As borrachas líquidas são amplamente utilizadas como “plastificantes reativos” ou modificadores em borracha e plástico e também podem ser usadas na moldagem por injeção. As borrachas líquidas são polímeros líquidos de menor peso molecular e possuem a mesma estrutura química que uma borracha sólida.
As borrachas líquidas estão no estado líquido à temperatura ambiente, embora exibam propriedades semelhantes às da borracha após a reticulação. Exemplos de borrachas líquidas incluem:
- borrachas de dieno líquido, como borrachas de butadieno líquido, borrachas de isopreno líquido e borrachas de estireno-butadieno líquido
- borrachas de silicone líquido
- borrachas de olefina líquida
- borrachas de uretano líquido
KURARAY LIQUID RUBBER
KURARAY LIQUID RUBBER é uma borracha líquida reticulável. Ela é composta por borracha de butadieno líquido (L-BR), borracha de isopreno líquido (L-IR) e borracha de estireno-butadieno líquido (L-SBR). As borrachas líquidas são incolores, transparentes, quase totalmente inodoras e possuem baixos valores de VOC. Os polímeros de butadieno, isopreno e estireno têm baixo peso molecular, situando-se entre a borracha sólida e o plastificante.
Os produtos KURARAY LIQUID RUBBER são projetados como “plastificantes reativos“, o que significa que, no processo de mistura de borracha, que é demorado e trabalhoso, eles ajudam a reduzir a viscosidade de Mooney e facilitam o processo de mistura. Isto resulta em maior fluidez do composto, bem como em redução do tempo e custos de processamento.
Além disso, as KURARAY LIQUID RUBBER são co-vulcanizáveis com a borracha base para evitar a migração. A migração reduzida melhora significativamente a vida útil e a durabilidade dos produtos.
KURARAY LIQUID RUBBER é altamente adequada para a moldagem por injeção de compostos de borracha.
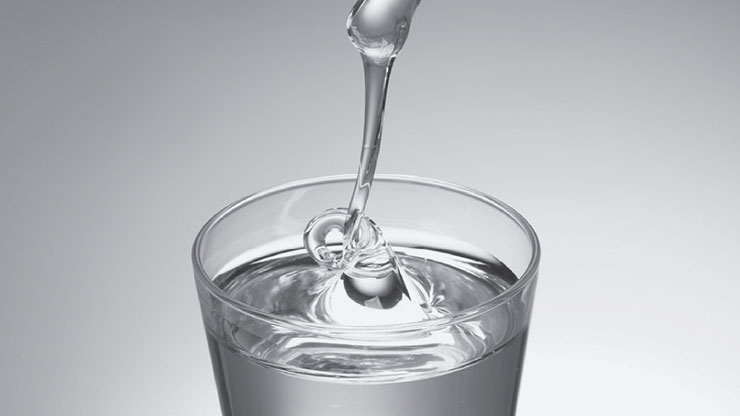
Benefícios
KURARAY LIQUID RUBBER pode melhorar o processo de moldagem por injeção de compostos de borracha de várias maneiras:
- Fluidez: Como auxiliar de processamento, reduz a viscosidade do fundido e torna os compostos de borracha mais fluidos e mais fáceis de injetar na cavidade do molde. Isto permite que o material alcance cantos estreitos do molde e melhore visivelmente a superfície, o que resulta em uma replicação mais precisa.
- Redução do consumo de energia: A melhor fluidez do composto aumenta significativamente a eficiência do processo de mistura e moldagem. KURARAY LIQUID RUBBER pode ajudar a reduzir a temperatura de moldagem, o que diminui o consumo de energia.
- Propriedades e desempenho: KURARAY LIQUID RUBBER pode aumentar as propriedades e o desempenho dos produtos finais de borracha, como a resistência à abrasão e a flexibilidade em baixas temperaturas. Além disso, KURARAY LIQUID RUBBER pode reduzir a migração e melhorar a vida útil e a durabilidade dos produtos finais de borracha, em comparação com plastificantes comuns.
Bom saber
A quantidade ideal de KURARAY LIQUID RUBBER a ser adicionada ao composto de borracha depende de vários fatores. Entre em contato conosco para saber mais obre como obter melhores resultados na moldagem por injeção com KURARAY LIQUID RUBBER!
Liquid farnesene rubber
Você valoriza a sustentabilidade?
A Liquid farnesene rubber (LFR) é baseada em matérias-primas naturais e renováveis: contém uma forma polimerizada de β-farneseno, um monômero renovável. Através de processos de fermentação estabelecidos, cepas de leveduras proprietárias convertem fontes de açúcar, como a cana-de-açúcar, em β-farneseno.
A Liquid farnesene rubber funciona como um plastificante reativo com um peso molecular maior do que o plastificante padrão. Ela é co-vulcanizável e reduz significativamente a migração, o que melhora a durabilidade dos compostos de borracha.
Gostaria de saber mais sobre nossos produtos e suas excelentes capacidades de processamento? Então entre em contato com seu representante Kuraray.
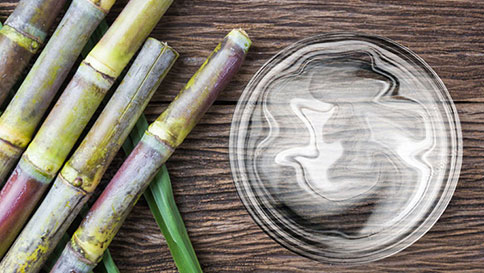
Outros materiais
Além dos plásticos, uma variedade de outros materiais pode ser usada na moldagem por injeção, como metais. No entanto, esse processo é comumente conhecido como fundição sob pressão.
Moldagem por injeção: Vantagens
A principal vantagem da moldagem por injeção é a produção de peças em grandes quantidades. A gama de aplicações varia desde pequenos lotes de algumas centenas de peças até a produção em massa de vários milhões de componentes.
Uma vez que o investimento inicial é amortizado, o preço unitário torna-se extremamente baixo com este processo de fabricação. À medida que o número de unidades aumenta, o custo unitário pode cair significativamente, tornando o processo altamente produtivo.
Outras vantagens da moldagem por injeção incluem alta repetibilidade e precisão, ampla gama de materiais, baixas taxas de desperdício e um excelente acabamento superficial.
Desvantagens
Uma grande desvantagem da moldagem por injeção são os altos custos iniciais associados à construção dos moldes.
Também pode ser caro se forem necessárias alterações no design dos moldes para adaptar o processo ou caso ocorram erros de design. Mesmo pequenos erros podem resultar em grandes custos.
Outras desvantagens incluem tempos de início mais longos e possíveis limitações com moldes maiores.
Aplicações
A moldagem por injeção é utilizada por diversas indústrias, incluindo produtos de consumo (escovas de dente), móveis (cadeiras), automotiva (painéis), eletrônica (carcaças de ferramentas elétricas), brinquedos (blocos de construção de plástico), saúde (seringas), embalagens (tampas de rosca) e muitos mais.
História
O inventor da moldagem por injeção é o americano John Wesley Hyatt. Ele patenteou a primeira máquina de moldagem por injeção junto com seu irmão Isaiah em 1871. Naquela época, era uma máquina relativamente simples, em que o plástico era injetado através de um cilindro aquecido em um molde com o auxílio de um pistão. Essa tecnologia foi usada para fabricar produtos como botões, pentes e bolas de bilhar.
Em 1903, os químicos alemães Arthur Eichengrün e Theodore Becker inventaram as primeiras formas solúveis de acetato de celulose que podiam ser facilmente moldadas por injeção em pó. Foi também Eichengrün quem desenvolveu a primeira prensa de moldagem por injeção em 1919 e patenteou a moldagem por injeção de acetato de celulose plastificado duas décadas depois.
Durante a Segunda Guerra Mundial, a indústria se expandiu fortemente devido à alta demanda por produtos de massa de baixo custo. Em 1946, o americano James Watson Hendry fez um avanço revolucionário ao desenvolver a primeira máquina de injeção de parafuso de extrusão. Essa inovação não apenas permitiu um controle muito mais preciso da velocidade de injeção e da qualidade das peças moldadas, mas também permitiu que o material fosse misturado antes da injeção.
Outra inovação de Hendry, na década de 1970, foi o processo de moldagem por injeção assistida por gás, que possibilitou a produção de artigos ocos e complexos, melhorando significativamente a possibilidade de design, a resistência e o acabamento superficial das peças moldadas por injeção.
Hoje, a moldagem por injeção é um mercado global com vendas anuais de centenas de bilhões de dólares. Mundialmente, cerca de 55 milhões de toneladas de plásticos são processadas por este método a cada ano.
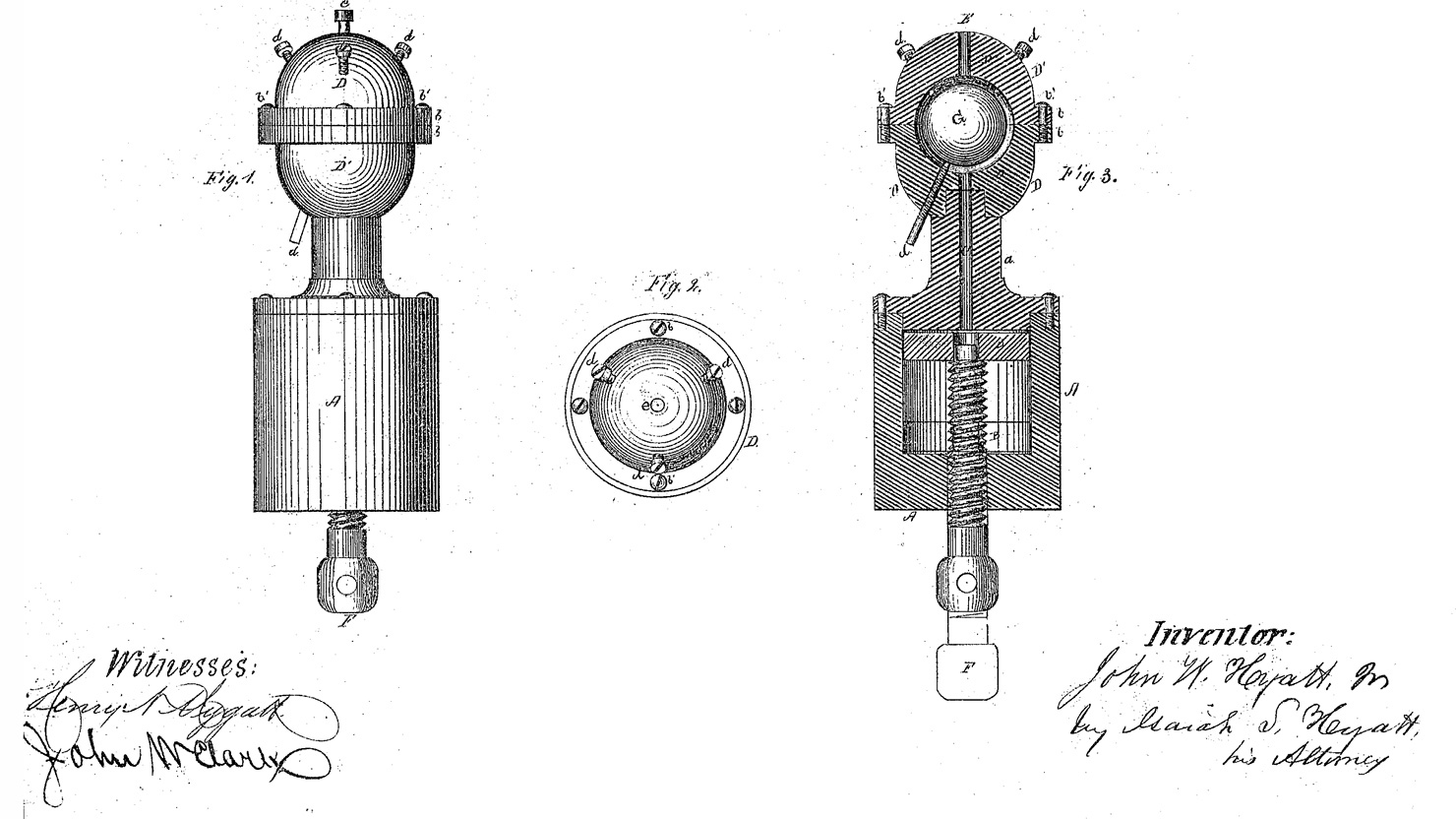
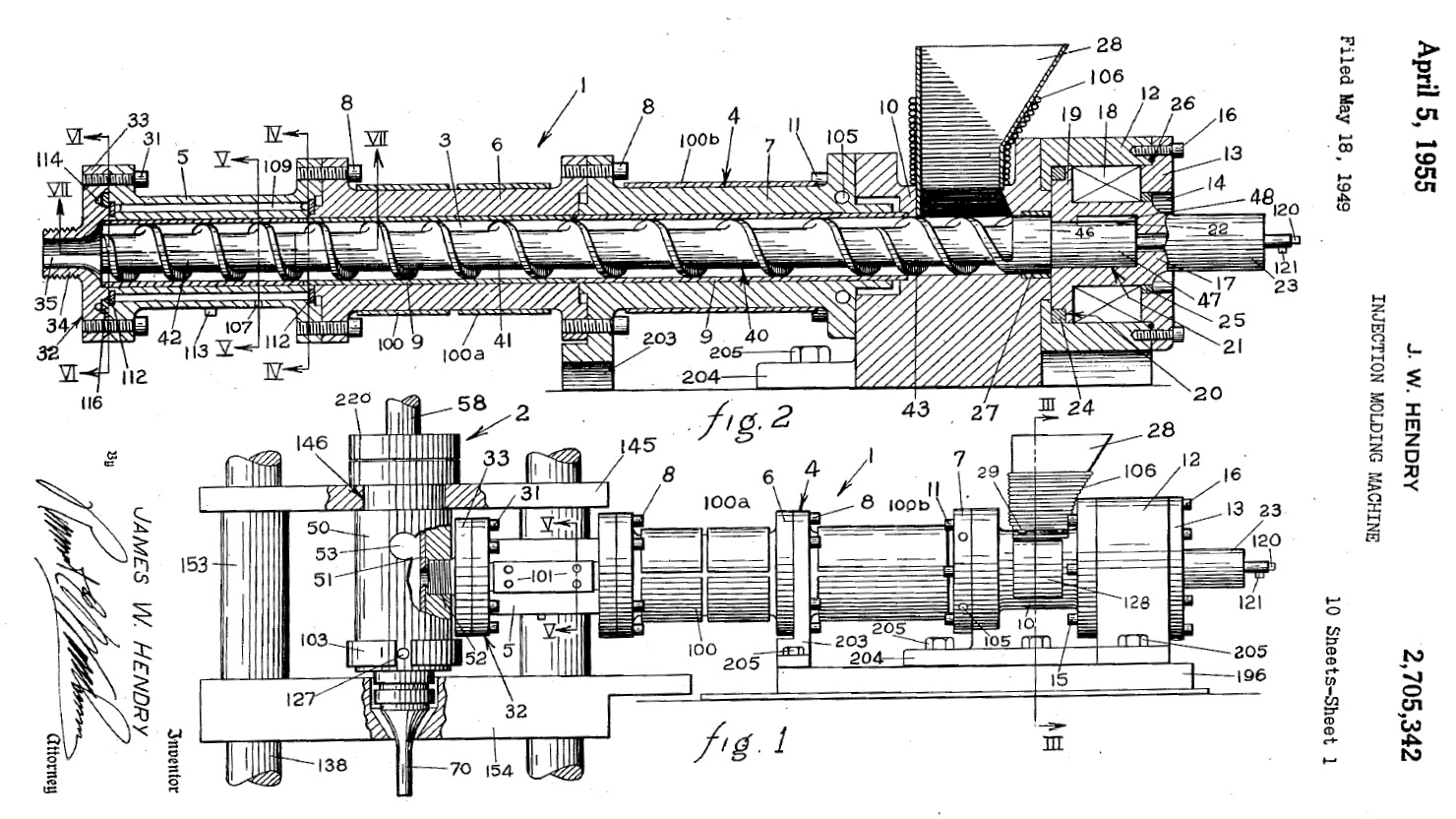
Normas e certificações
Existem diversas certificações que podem confirmar a qualificação do seu fornecedor de serviços de moldagem por injeção. De particular importância é a certificação ISO 9001.
A Society of the Plastics Industry (SPI) definiu, adicionalmente, padrões para a qualidade óptica dos plásticos para a indústria de plásticos dos Estados Unidos. Esses padrões determinam as qualidades de superfície das peças plásticas moldadas por injeção, diferenciando doze qualidades de superfície em quatro categorias.
Custos
A moldagem por injeção oferece vantagens significativas para a produção de peças moldadas em grandes volumes. No entanto, quem opta por esse processo deve estar ciente dos custos iniciais. O investimento inicial pode ser bastante elevado. Além da máquina de moldagem por injeção, os custos com moldes são especialmente significativos e podem, por vezes, chegar a milhões.
Isso pode ser de seu interesse: A Kuraray lhe dá suporte no desenvolvimento de compostos para tempos de ciclo mais rápidos e produção otimizada, visando a maior rentabilidade possível do processo de moldagem por injeção.
Você tem uma ideia clara do produto que deseja produzir, mas não tem certeza sobre a fomulação e a composição dos materiais? Então, entre em contato com o representante da Kuraray. Teremos prazer em ajudá-lo com nossa experiência em processos e materiais e apoiá-lo na organização de sua cadeia de suprimentos, se necessário.
Contato para negócios
Aguardamos a sua solicitação!
Contato