射出成形とは?
射出成形とは、プラスチック部品を大量に生産するために広く用いられている製造プロセスです。このプロセスでは、射出成形機を使って材料を溶かし、圧力をかけて金型に注入し、冷却後に希望の形状の部品を作り出します
日常生活におけるプラスチック部品の大部分は射出成形で作られています。これらの部品としては、歯ブラシ、車の部品、台所用品のハウジングなどが挙げられます。
射出成形は、単価が安く、複雑な形状を安定した品質で製造できるため、広く普及しています。プラスチック、主に熱可塑性ポリマーが原料として使用され、着色したり添加物を充填したりすることができます。
高度な設計上の柔軟性が求められます。射出成形は、CNC機械加工のような他の製造プロセスと比較して、表面のテクスチャーや素材のバリエーションが非常に豊富です。
射出成形設備
技術的な面では、射出成形プロセスには射出成形機と、製造する部品のために専用に作られた金型が必要です。
射出成形機
射出成形機は、射出装置、金型、型締ユニットまたは突出ユニットの3つの主要部品で構成されています。
射出ユニット内では、ホッパーが射出ラムまたはスクリュー式プランジャーと加熱ユニットにプラスチックを供給します。必要量の溶融プラスチックが溜まったら、射出プロセスに入ります。
材料は熱/せん断によって溶解され、高圧で金型に注入されます。そこで射出成形部品が形成されます。
型締ユニットまたは突出ユニットは、金型の開閉と成形品の突出を行います。トグルタイプの型締ユニットが最も一般的で、金型を保持するプラテンで構成されています。これらのプラテンは通常、射出成形機のフレーム上に垂直に配置され、強力な型締力を発揮する内部プレスに例えることができます。あるいは、ストレート油圧式型締装置では、油圧シリンダーを使用して金型に型締力を与えます。
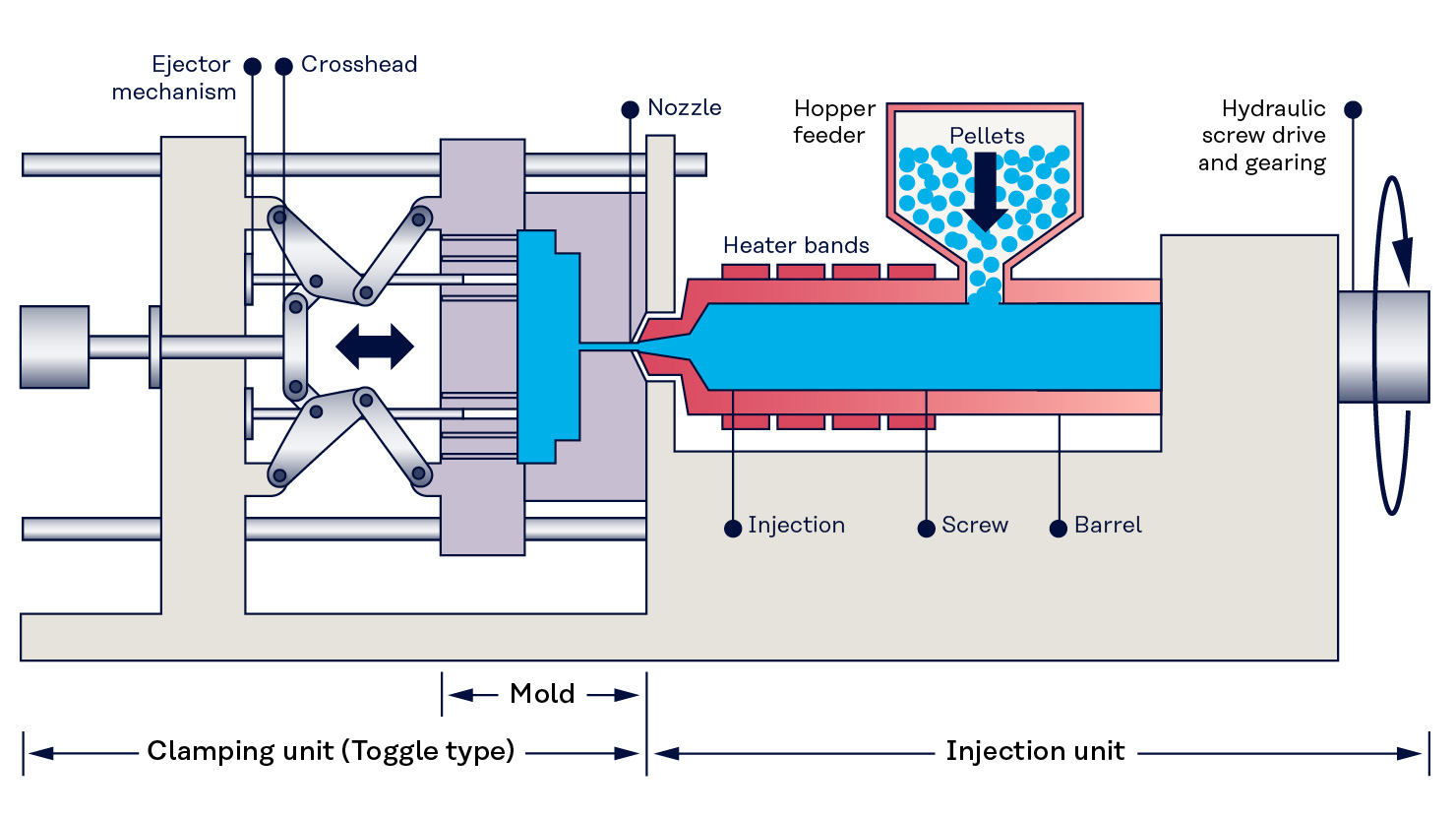
型締力
型締力は数トンから数千トンに及びます。このような広い範囲から、プレス機は一般的に、機械が発揮できる型締力のトン数で分類されます。特定の部品を成形するのに必要なトン数は、その型打ち面積によって決まります。
経験則では、ほとんどの製品で1平方インチあたり通常5トンです。ただし、硬度が非常に高いプラスチック材料の場合は例外で、金型を閉じた状態に保つためにより高い射出圧力と型締力が必要になります。大きな部品には、より大きな型締力が必要です。
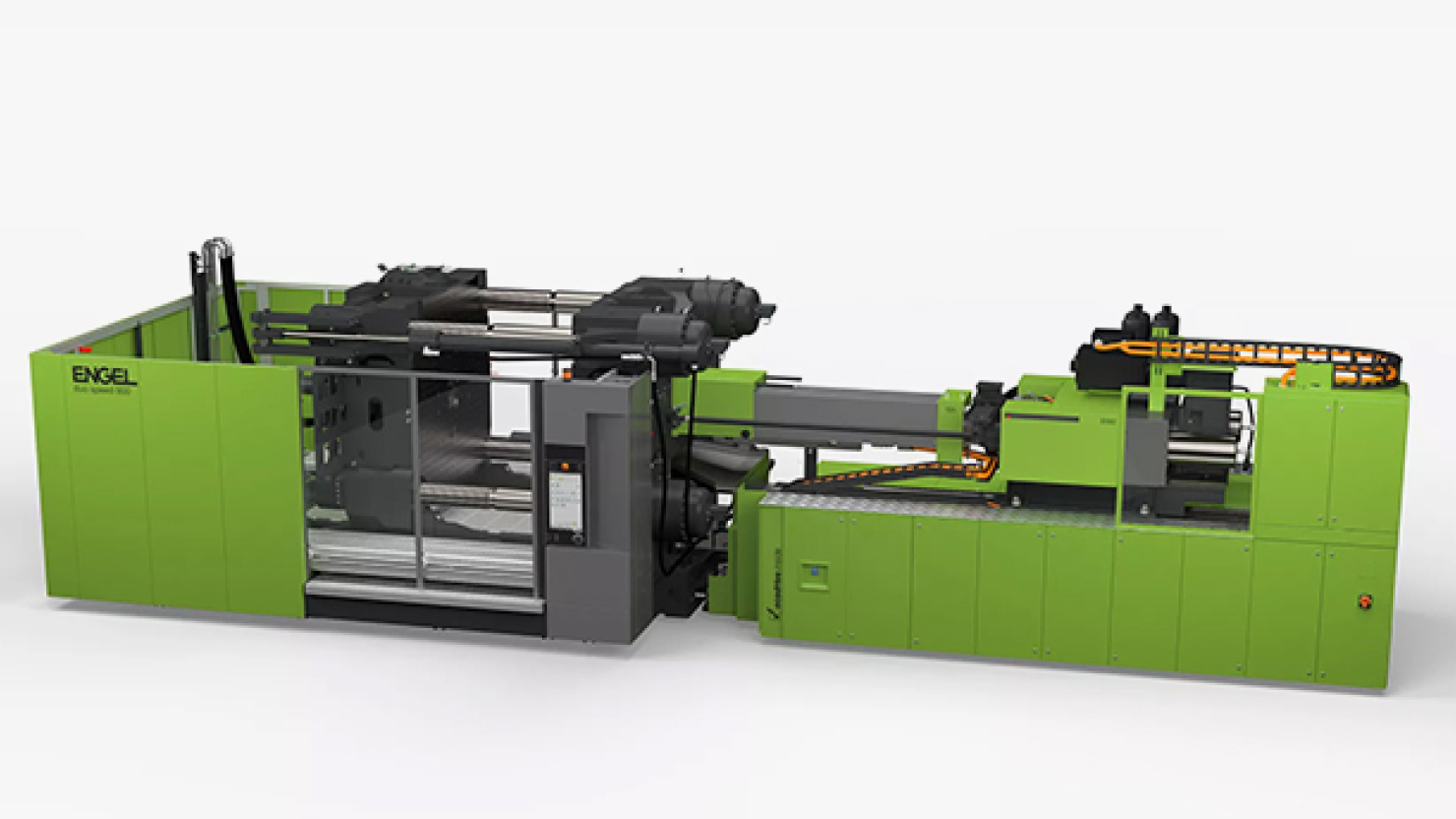
金型
金型は、単に「ツール」と呼ばれる場合もあり、プロセス全体の心臓部です。これは中空になった金属ブロックで、そこに溶融プラスチックを注入して目的の形状を作ります。金型には、温度調節とガス抜きのために多数の穴が開いています。温度は、水、オイル、ヒーターを使って制御します。
最も単純な形では、金型は2つの部分で構成されます。
- キャビティ(正面)と
- コア(背面)。
一方、射出成形部品には通常2つの面があります。
- 部品のA面は、通常、見た目が良い方が空洞に面しています
- B面は機能面とも呼ばれ、通常、部品の隠れた構造要素が含まれています。そのため表面は粗く、突き出しピンの跡が残っている場合も多いです。
溶解したプラスチックはスプルーを通って金型に流れ込み、キャビティに充填されます。通常、射出成形サイクルの約半分を占める冷却と固化の後に、金型が開かれ、成形された部品が排出されます。
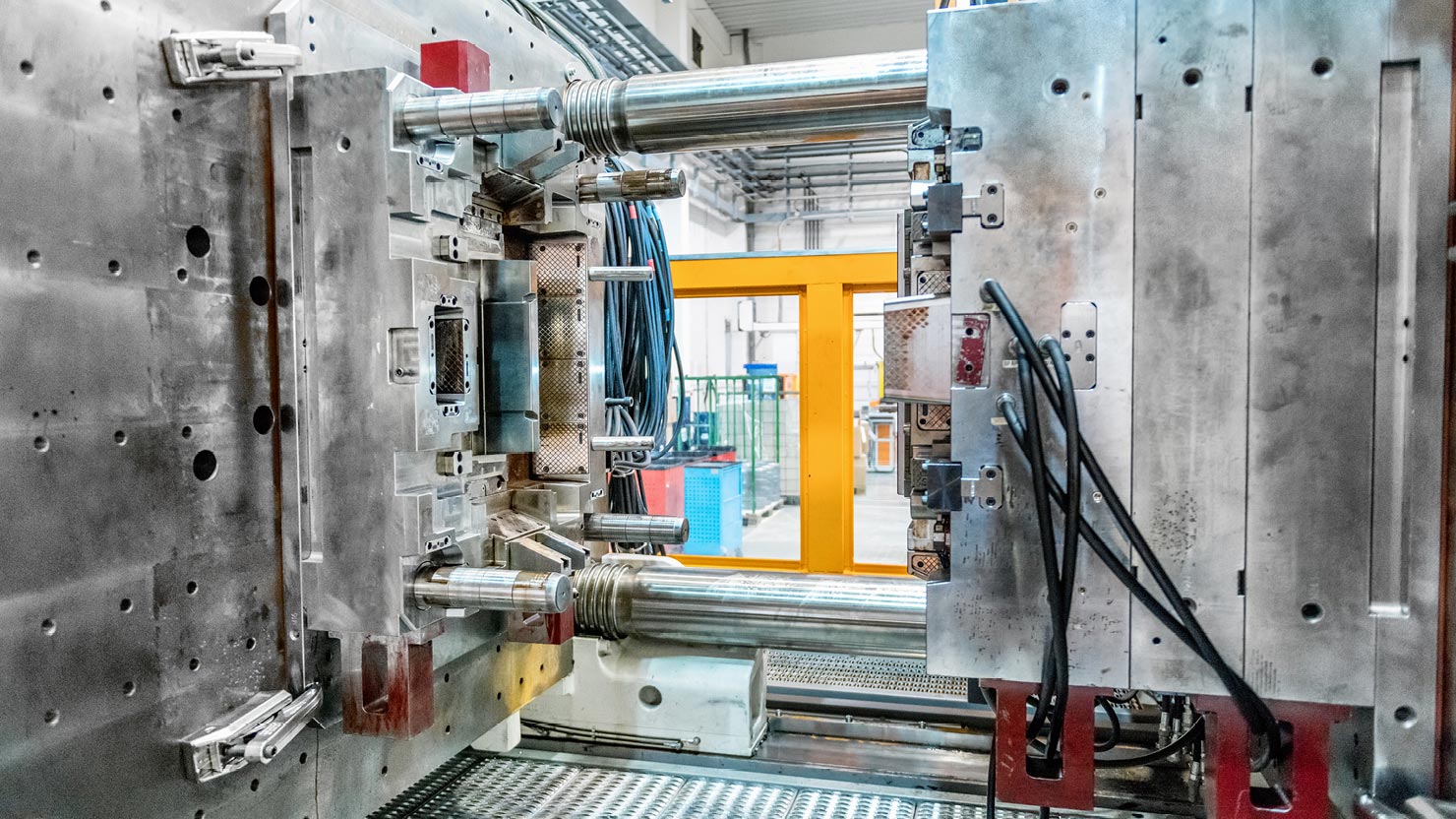
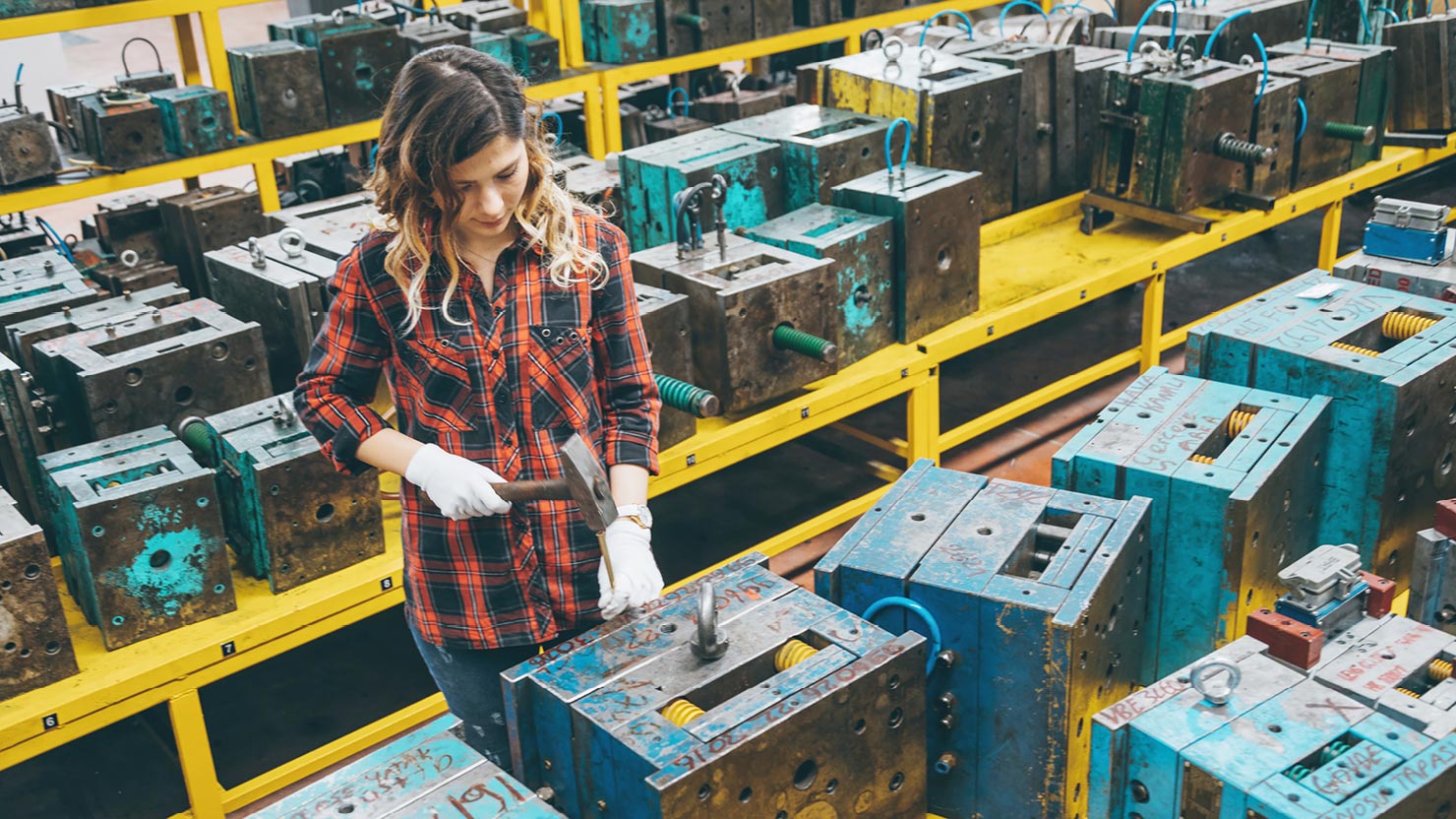
参考情報
金型は製造コストが高く、そのため、数千から数百万個の部品を大量生産する場合に使用されます。通常、硬化鋼またはプリハードン鋼で製作されますが、アルミニウムやベリリウム銅合金で作ることもできます。
金型材料
スチール製の金型は製造コストがかかりますが、寿命も長いです。より多くの部品を生産できるのであれば、スチール製の金型にかかるコストは、追加費用を十分に相殺することができます。硬化鋼の金型は耐摩耗性と耐久性に優れています。プリハードン鋼金型は耐摩耗性が低く、少量の部品または大きな部品に使用されます。
安価なアルミ金型は、数万から数十万個の部品を製造するのに経済的でしょう。ベリリウム銅合金は、急速に放熱する必要がある場合や、せん断熱が高い場合に使用されます。
金型設計
金型は写真のネガに例えることができます。金型の表面構造と形状が完成部品に転写されます。また、材料フロー用のゲートシステムや内部冷却チャンネルなどの機能も備えています。
何千、何百万もの部品を高い精度と再現性で生産するためには、金型メーカーは膨大な専門知識を必要とします。なぜなら、金型は肉厚、コーナー、リブ、アンダーカット、スレッドなど、さまざまな検討事項があり、非常に複雑なものになることもあるからです。射出成形の立ち上げコストの大部分を金型が占めるのも、この開発費の高さが理由です。
金型のコストは大幅に変動する可能性があります。少量生産用の単純な形状のストレート抜き金型は、比較的簡単に開発でき、コストも数千ドルです。大規模生産用で複雑な形状を持つさらに高度な金型は、格納可能なコアやインサートを必要とするため、はるかに高いコストがかかりますこれらの可動要素は、開口部や空洞などのオーバーハングを持つ部品を製造するため、上方または下方から金型に挿入されます。
金型設計は、機械メーカーまたは専門業者が社内で行うことが多く、原材料の検討や有限要素解析の活用が必要となります。金型メーカー、またはツールメーカーは、通常スチールやアルミニウムなどの金属から金型を作り、CNCフライス盤で精密に削り出して目的の形状に仕上げます。最近の3Dプリンティング材料の進歩により、従来の方法よりも低コストで小ロット用の金型を製造できるようになりました。
ランナーシステムとも呼ばれるゲーティングシステムは、流れと圧力を制御し、溶融プラスチックを金型に送り込みます。溶融プラスチックは、金型に入ると次のような流路を流れていきます。
- スプルー、
- メインランナー
- サブランナー、および
- ゲート、または「投入口」で、これは、サブランナーと金型のキャビティの間にある細い溝です。
また、射出成形プロセスでは、一般にコールドスラグウェルがコールドスラグを回収し、サブランナーやゲートの閉塞を防いで、残った高温の材料処理を複雑にすることなく金型のキャビティに流入できるようにします。
複数のパーツを製造するには、複数のスプルーが必要になることが多いです。スプルーシステムは突出後にパーツから切り離されます。射出成形は廃棄物の少ない製造方法であり、スプルーシステムだけが唯一の材料廃棄物となります。この廃棄物の一部は、素材によってはリサイクルや再利用も可能です。
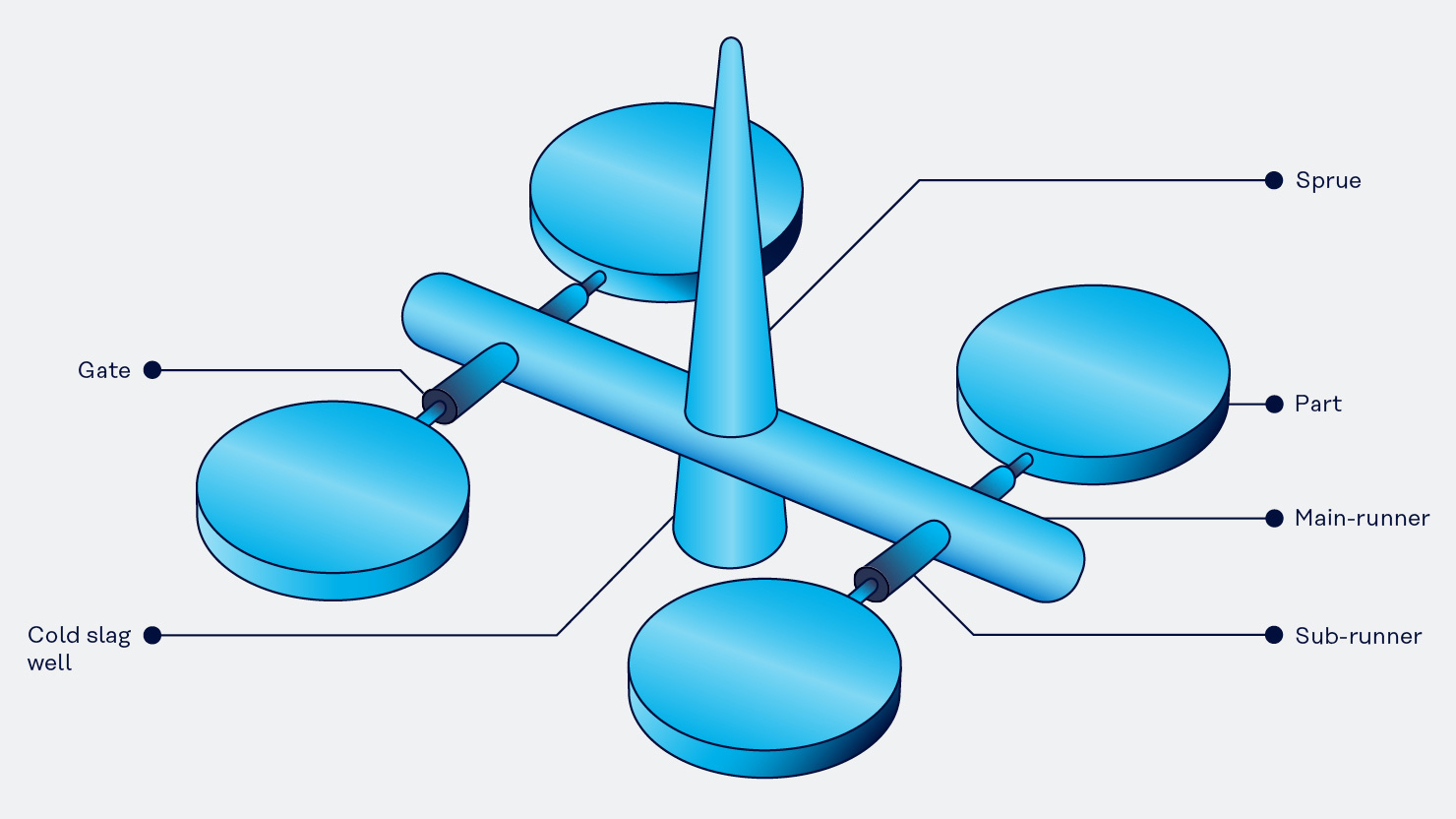
金型メーカーは、部品の向き(A面 対 B面)、金型製造の容易さ、材料の選択、材料の流れ、部品のサイズ、トリミングの挙動、スクラップ・コストなど、さまざまな考慮事項に応じて、数種類のゲートの中から選択することができます。詳しくはBasiliusの射出成形ゲートガイドをご覧ください。
金型には、2つの主な目的を持つ閉鎖システムも含まれています。
- 1つめの目的は、射出中、金型の2つの部分をしっかりと閉じておくこと、
- 2つめは、射出成形品を金型から押し出すことです。
その後、排出された部品はベルトコンベアや容器に落下し、保管されたり、組み立てられたりします。
金型のさまざまな可動部分が100%揃うことはないため、射出成形されたほとんどすべての部品に以下の2種類の欠陥が見られます。
- 一つ目は分割線(金型の2つの半分が合わさる部分に現れる線)、
- 二つ目の蹴子痕は突き出しピンによって生じるものです。
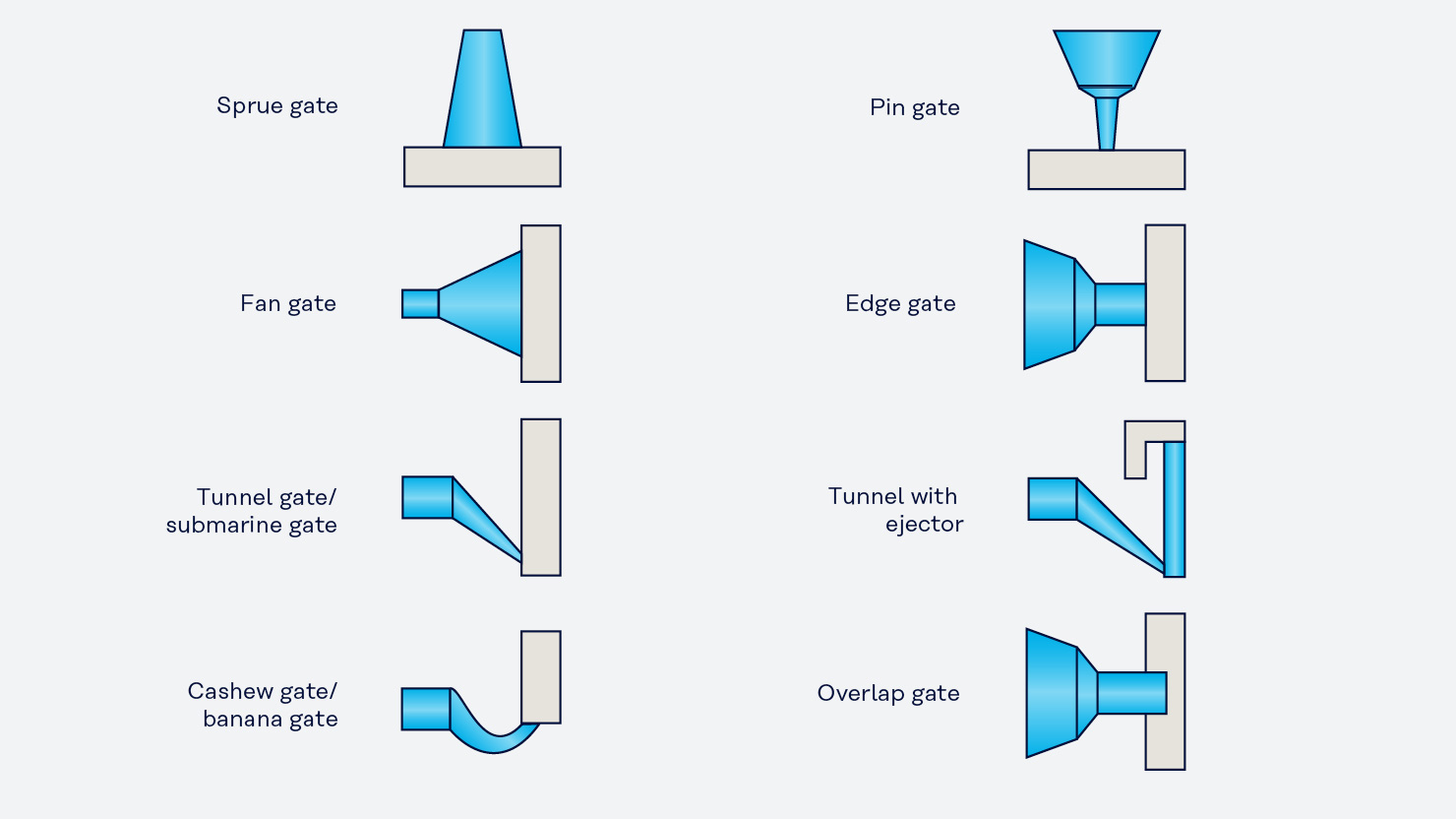
成形
「成形」という用語は、スプルー、コールドスラグウェル、ランナー、ゲート、およびパーツを形成する金型のキャビティ部分をすべて合わせたものに材料を充填することを指します。
材料によっては、スプルー、コールドスラグウェル、ランナー、ゲートの中身は廃棄されるか、あるいは再粉砕されて別の射出成形サイクルで再利用されます。
プロセスの特性
射出成形のプロセスサイクルは非常に短く、部品の大きさにもよりますが、数秒から2分程度です。そのプロセスは主に以下の4つのステップに分けられます。型締、射出、冷却、排出。
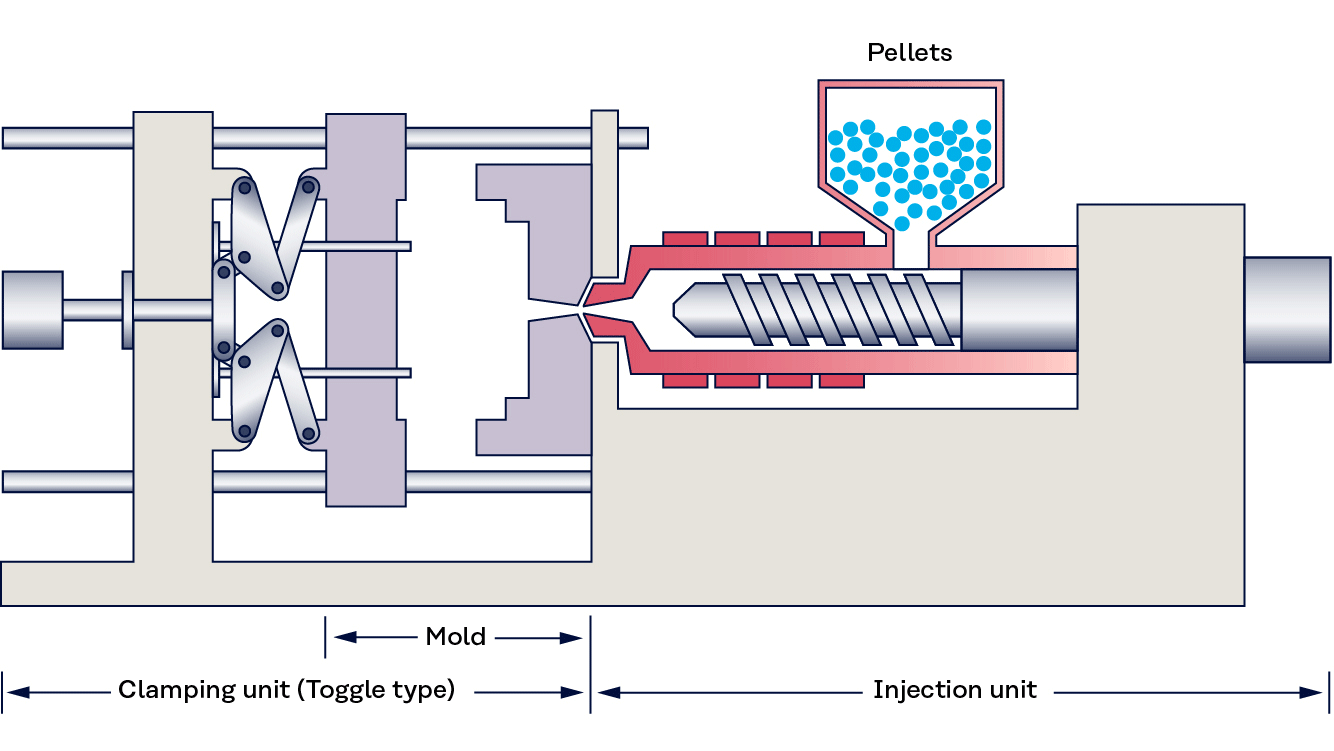
ステップ1:型締
材料が金型に注入される前に、金型の2つの半分が型締ユニットによってしっかりと閉じられる必要があります。型締ユニットは、材料が射出される間、金型の半分をしっかりと押し付けます。型締力の大きい大型機は、閉じるのに時間がかかります
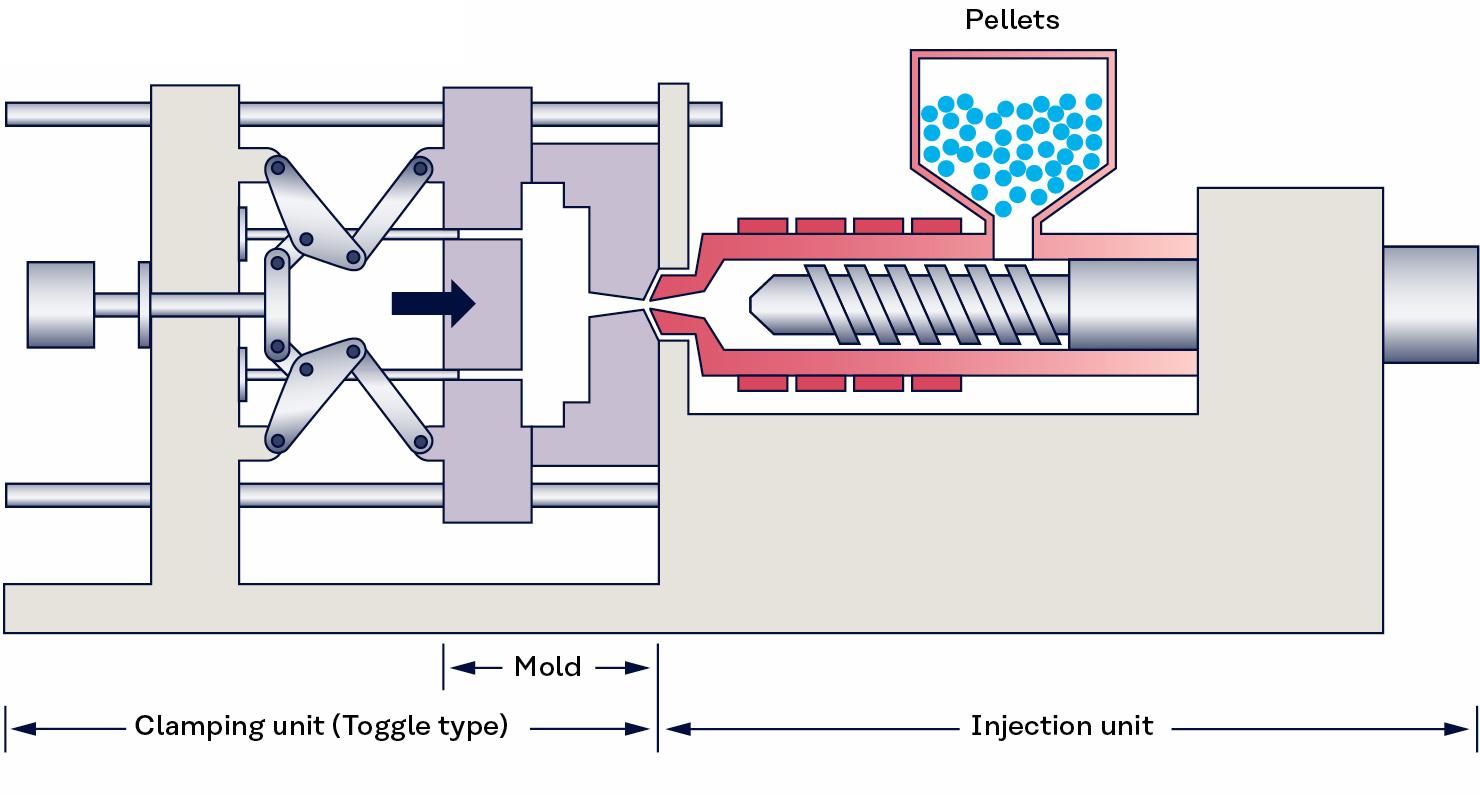
ステップ2:射出
原料(通常はプラスチック顆粒)は射出装置から金型に運ばれ、そこで熱と圧力によって溶解されます。溶融プラスチック(ショット)は、スプルーシステムを通って金型に注入され、キャビティ全体を満たします。
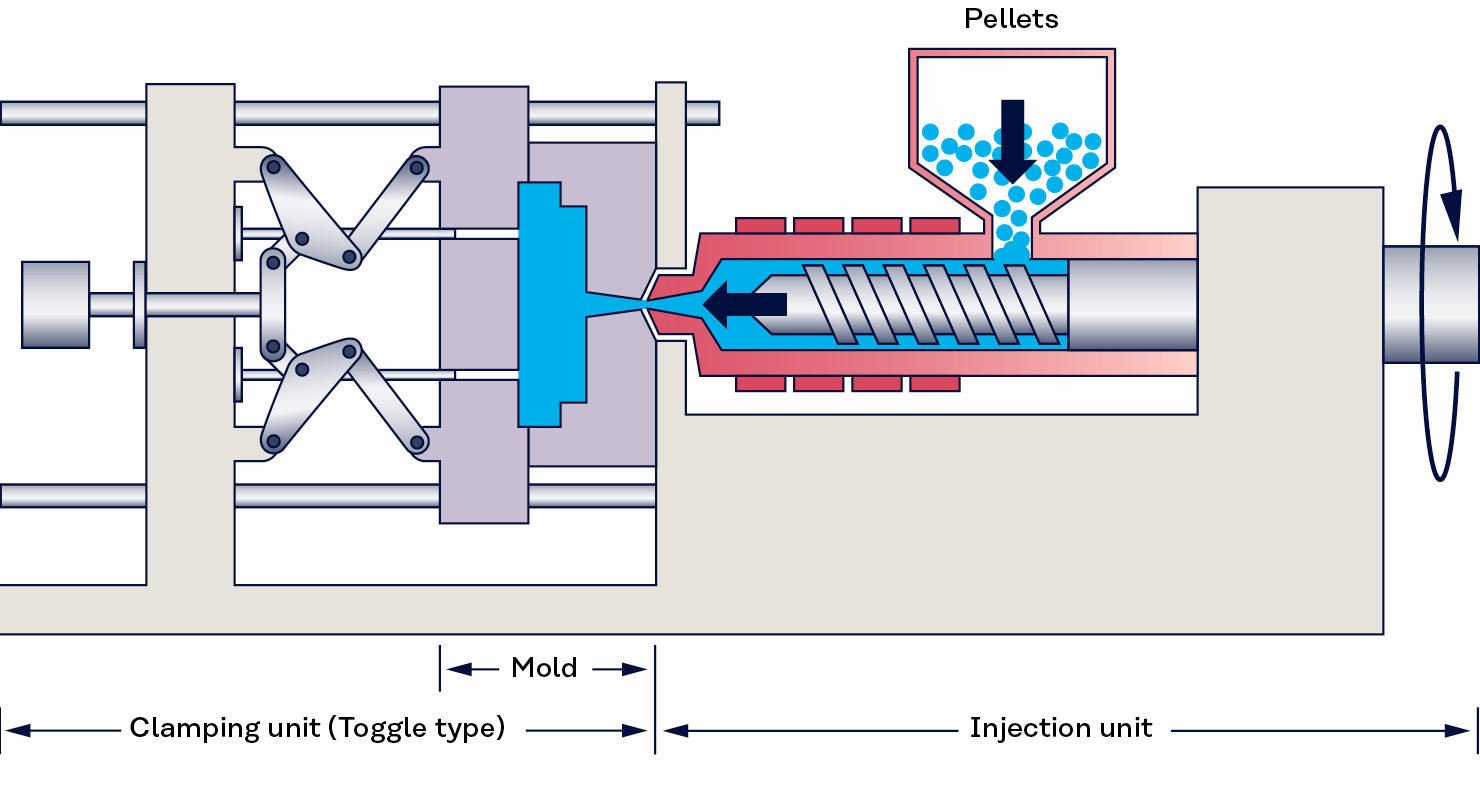
ステップ3:冷却
金型内では、溶融プラスチックが金型内面に接触すると同時に冷え始めます。材料が冷えると、再び固まって、形ができます。必要な冷却時間が経過するまで、金型は閉じたままです。
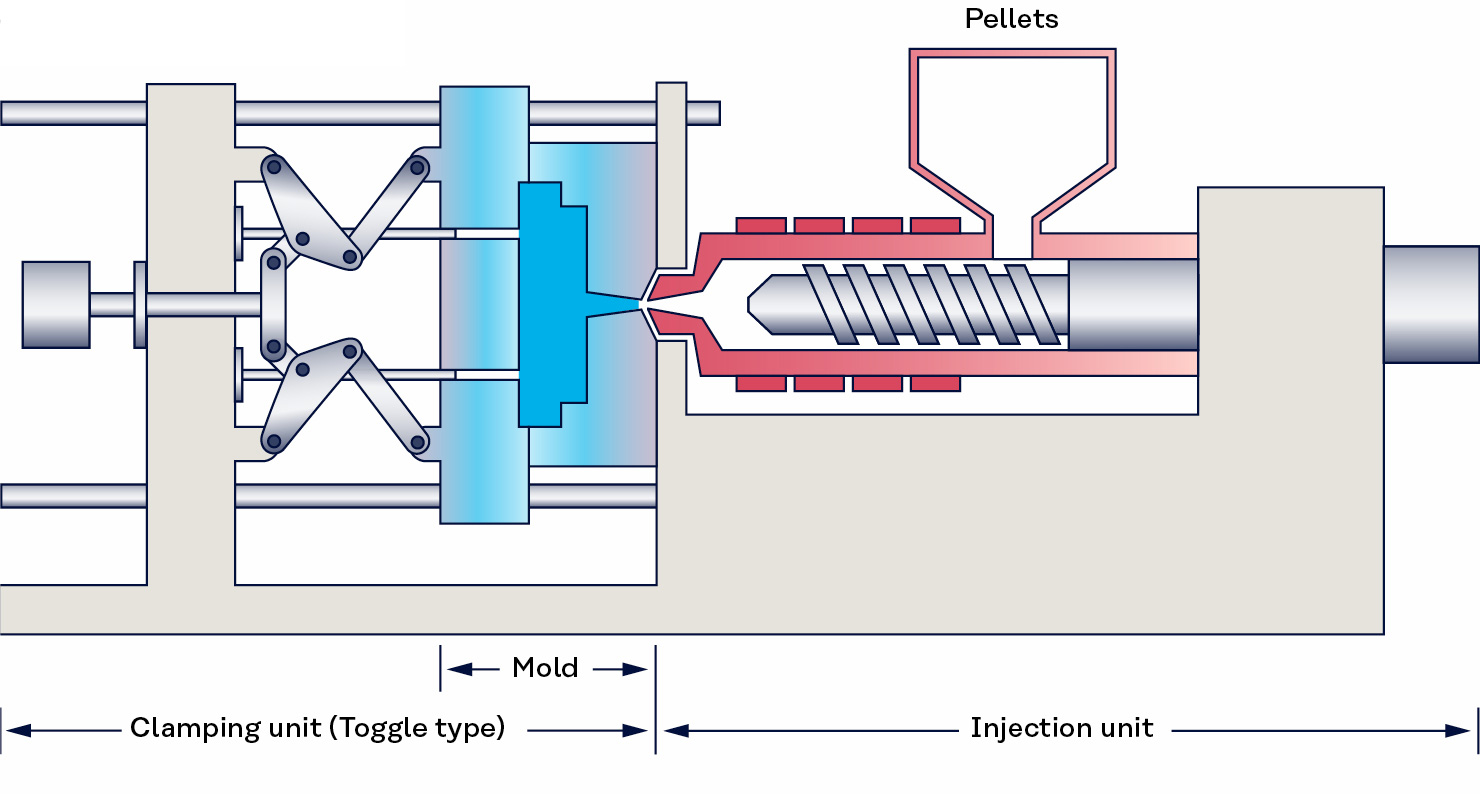
ステップ4:排出
冷却された部品は、排出システムを使って金型から排出されます。金型を開くと、成形品は機構によって金型から押し出されます。ゲートの設計によって、部品は成形品の他の部分から自動的に分離されるか、切断することで分離されます。
排出後、ベルトコンベアーで成形品を保管、組立、または後処理するため移動させます。同時に、金型は次のショットのために再度閉じられ、射出成形プロセスが繰り返されます。射出成形された部品は、すぐに使用できる場合もあれば、さまざまな後処理が必要な場合もあります。
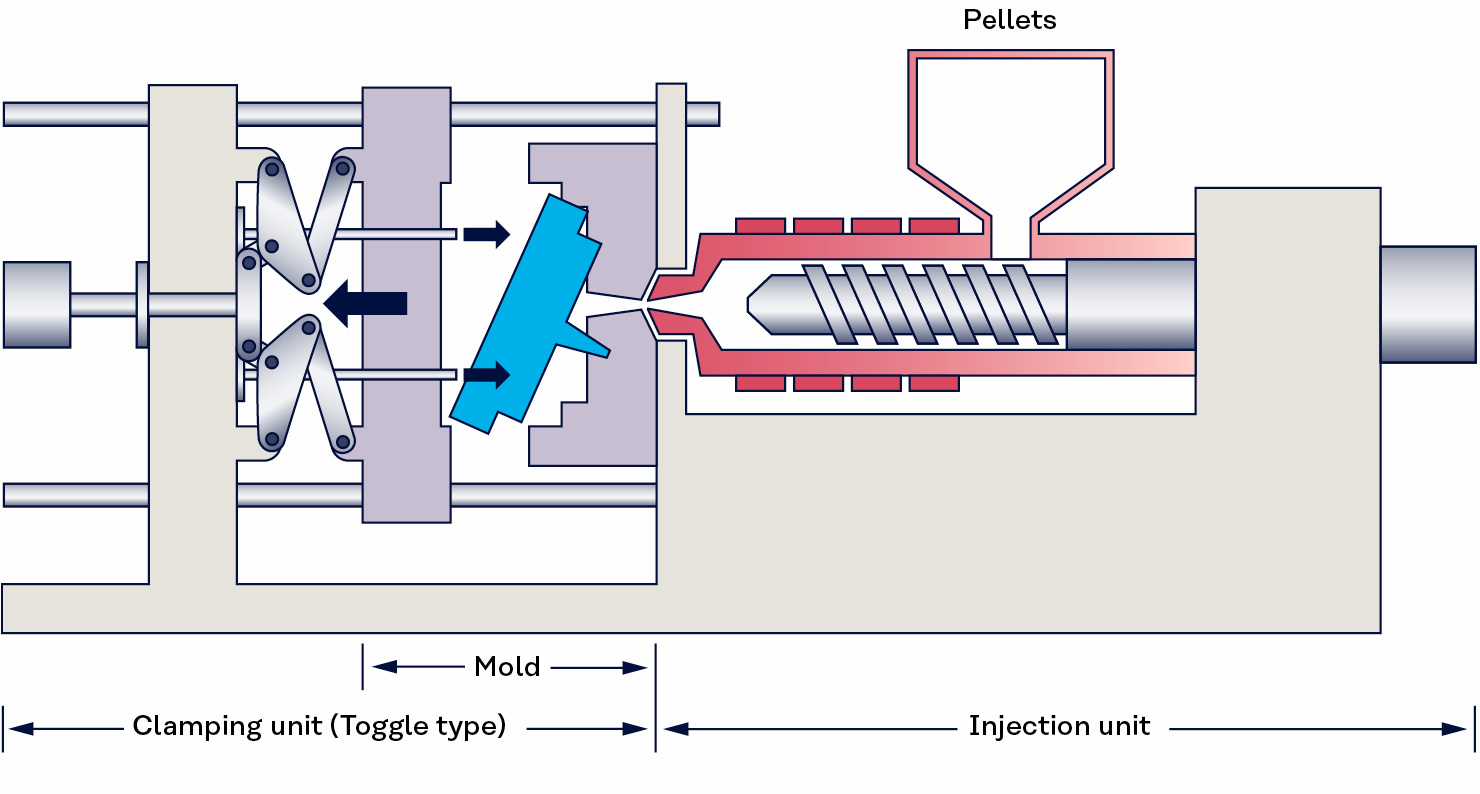
射出成形の種類
従来型射出成形と非連続型射出成形
従来型の射出成形では、射出は一定の圧力で行われ、金型のキャビティに充填され圧縮されます。 しかし、その結果、成形品の寸法がサイクルごとに大きく変わってしまう可能性があります。
非連続型射出成形では、射出プロセスを2つの段階に分離することで、部品の寸法とショット間の一貫性の制御を高めています。
- 速度制御でキャビティに約98%まで充填し、次に
- 残りの2%を圧力制御で充填します。
非連続型射出成形は科学的射出成形とも呼ばれます。
単成分射出成形と多成分射出成形
プラスチックの射出成形は、単成分射出成形と多成分射出成形に区別されます。多成分射出成形は、使用する材料の数によって、2K射出成形、3K射出成形などに区別されます。
2Kとは2液射出成形のことで、硬い材料(PPなど)の周りに柔らかい材料(TPEなど)を成形します。3Kは2Kに似ていますが、レイヤーやコンポーネントが追加されます。
欠陥の可能性
射出成形プロセスでは、機械に依存する欠陥、材料に依存する欠陥、または機械と材料の両方に依存する欠陥など、さまざまな欠陥が発生する可能性があります。
以下のセクションでは、欠陥をある程度分類し、その例を紹介します。実際には、成形部品の欠陥の原因には非常に多くの可能性があり、そのすべてを文章で説明することは非現実的です。
機器に依存する欠陥
機器に依存する欠陥は、技術的な理由によるものです。例えば、射出圧力が高すぎたり、金型の型締力が低すぎたりすると、余分な溶融材料が金型から逃げてしまうことがあります。これはフラッシュまたはフラッシングと呼ばれる欠陥です。
冷却にムラがあると、部品に反りが生じることがあります。金型設計や成形プロセスが、冷却中に通常発生する収縮を正しく考慮していない場合、部品に反りが生じることがあります。
成形品に気泡ができるのは、金型や材料が熱すぎる場合です。この欠陥は通常、機械に関連したもので、金型周辺の冷却不足や、ヒーターが意図したとおりに作動していないことが原因です。
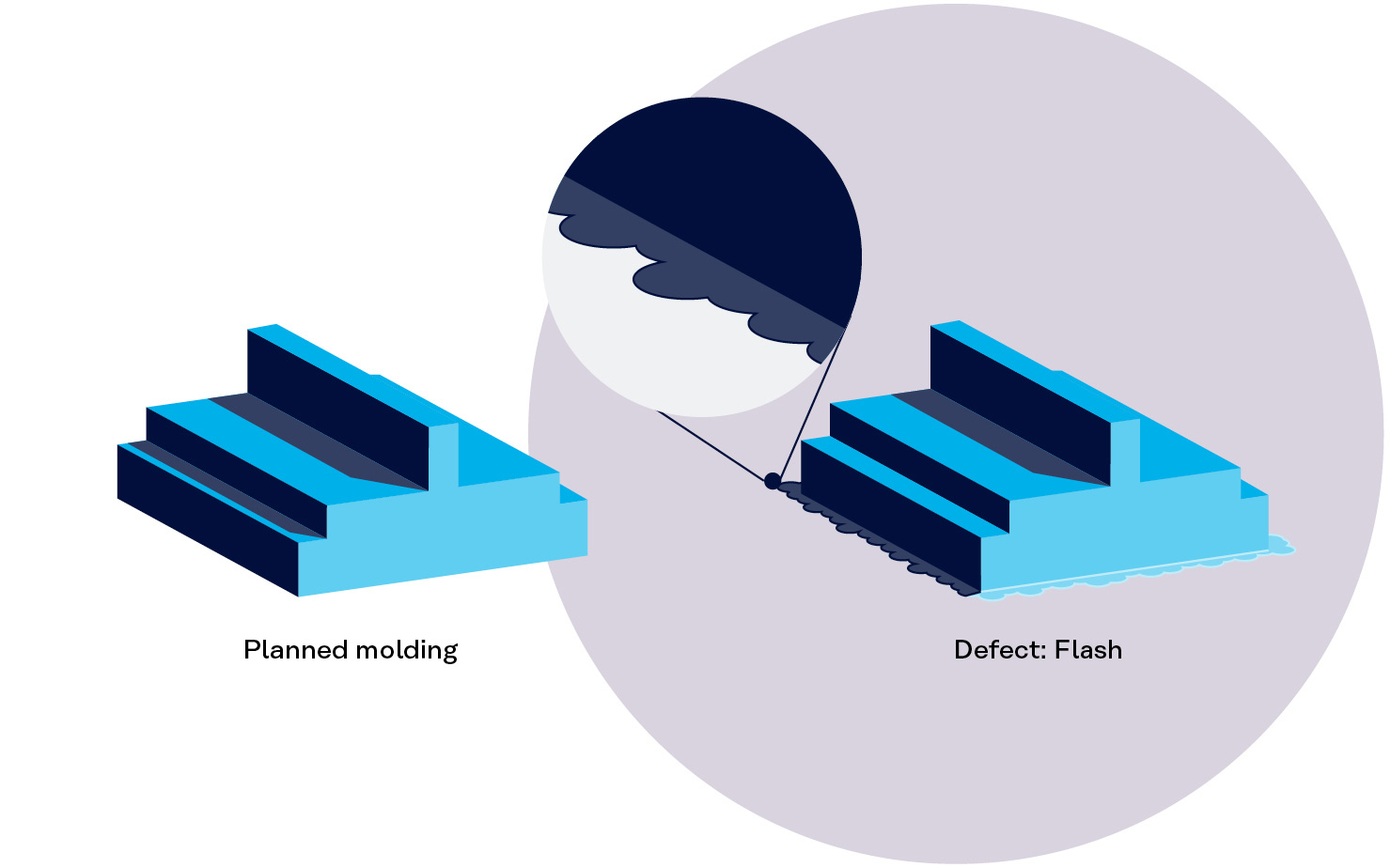
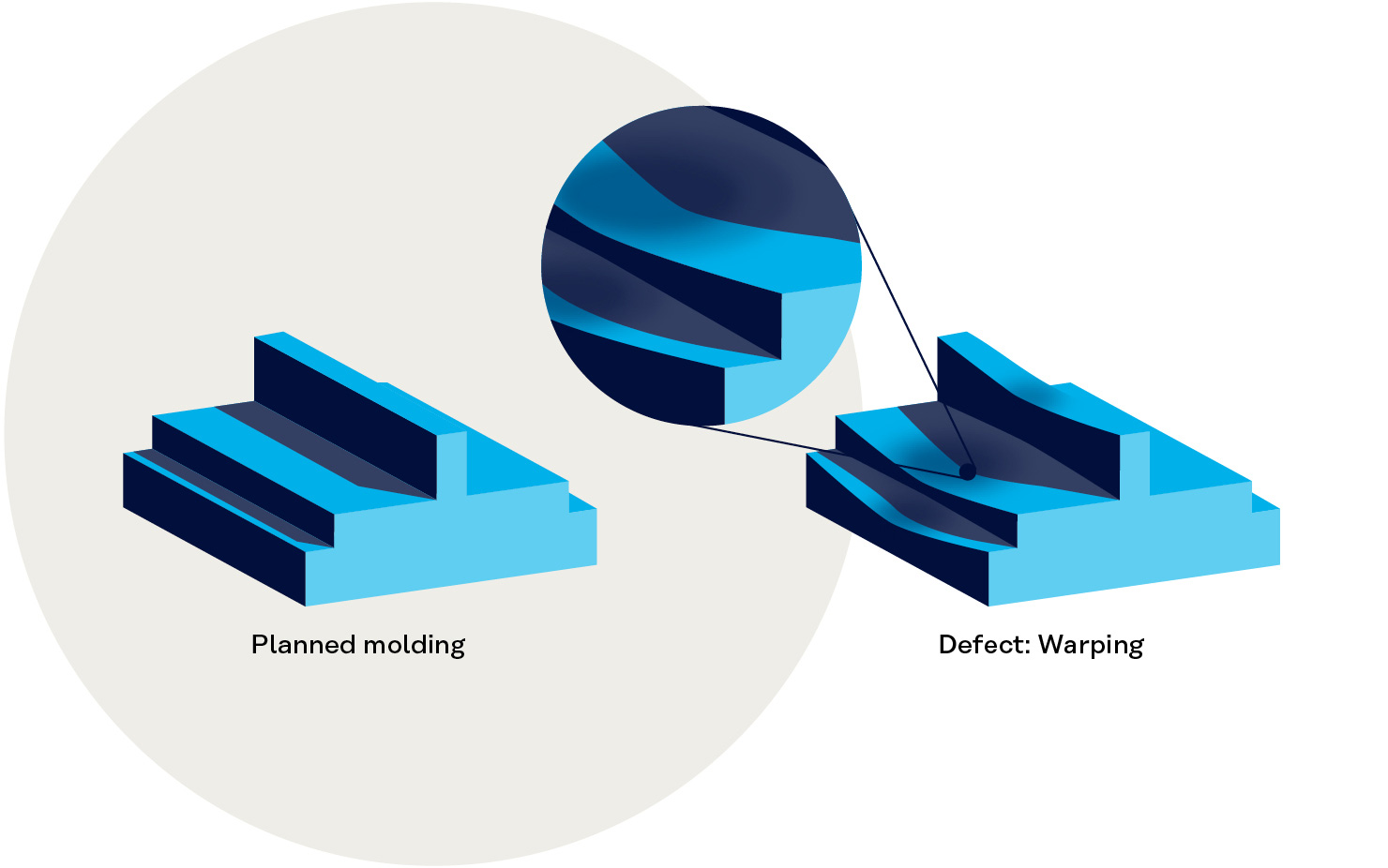
材料に依存する欠陥
ポリマーの劣化は、材料に依存する欠陥の一例です。材料の加水分解、酸化、またはその他のポリマー劣化が原因となり、成形品にひび割れ、変色、または同様の欠陥が生じます。
材料に依存するもう一つの欠陥が、ショートショットです。射出成形機内に十分な材料がない場合、成形品には未充填部分が生じてしまいます。あるいは、流量不足が原因の場合もあります。
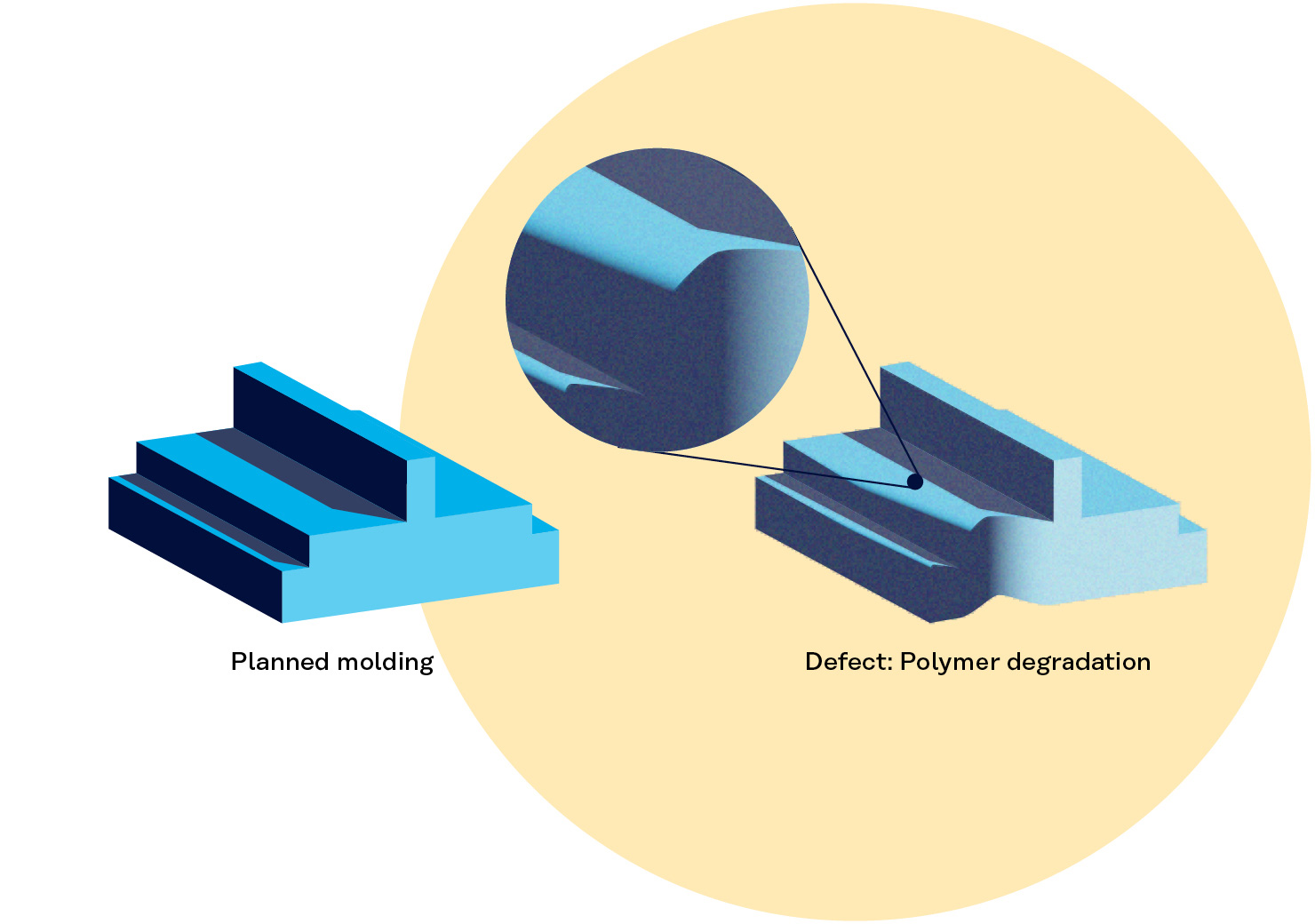
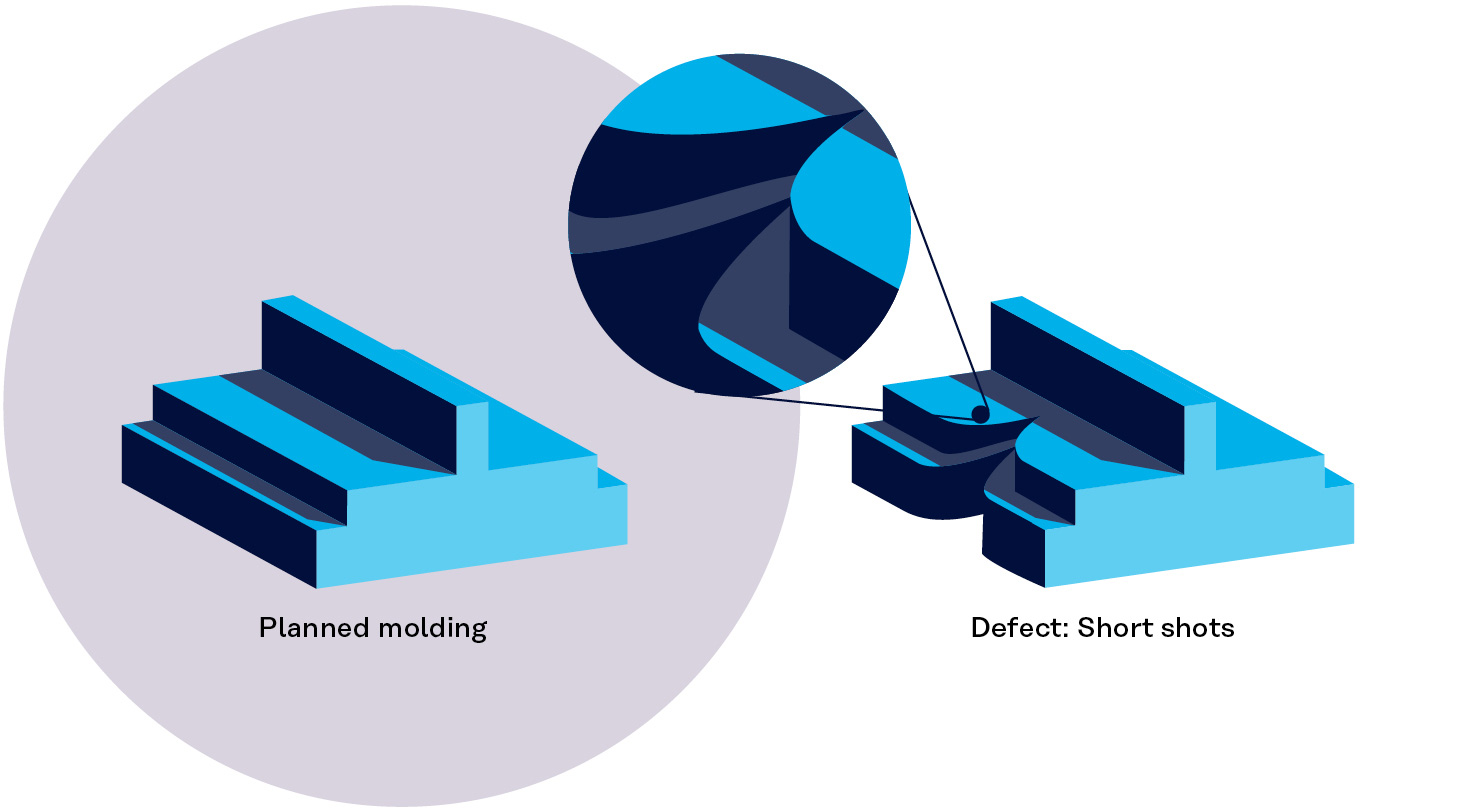
機器と材料に依存する欠陥
機器と材料は互いに影響し合うため、双方に起因する欠陥が発生することはよくあることです。例えば、冷却速度が速すぎる場合、機器に依存した欠陥としてヒケが発生することがあります。このため、中心部の材料が所定の位置に流れる前に、部品の表面が固まってしまうことがあります。あるいは、充填樹脂や強化樹脂のように、収縮やヒケが発生しやすい材料もあるため、材料に起因する欠陥である可能性もあります。
蹴子痕の原因となる機器関連の欠陥の例としては、金型の設計不良(特にゲート)、突き出しピンの設計不良、金型のメンテナンス不良などがあります。一方、脆さや耐衝撃性の低さなど、材料に起因する欠陥も蹴子痕につながる可能性があります。
繰り返しとなりますが、この欠陥とその理由の羅列は不完全なものです。私たちはいくつかの例を紹介しているに過ぎません。
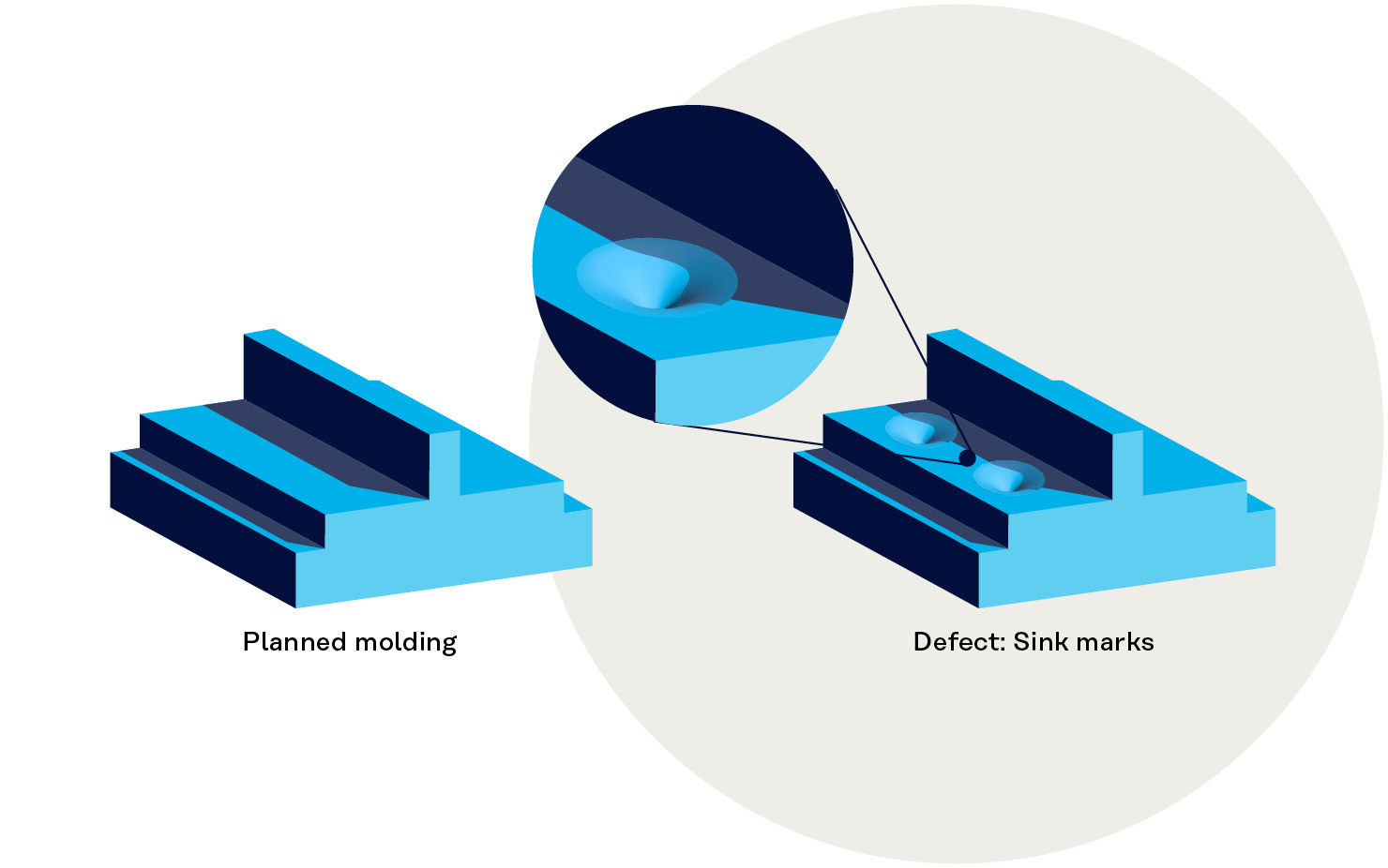
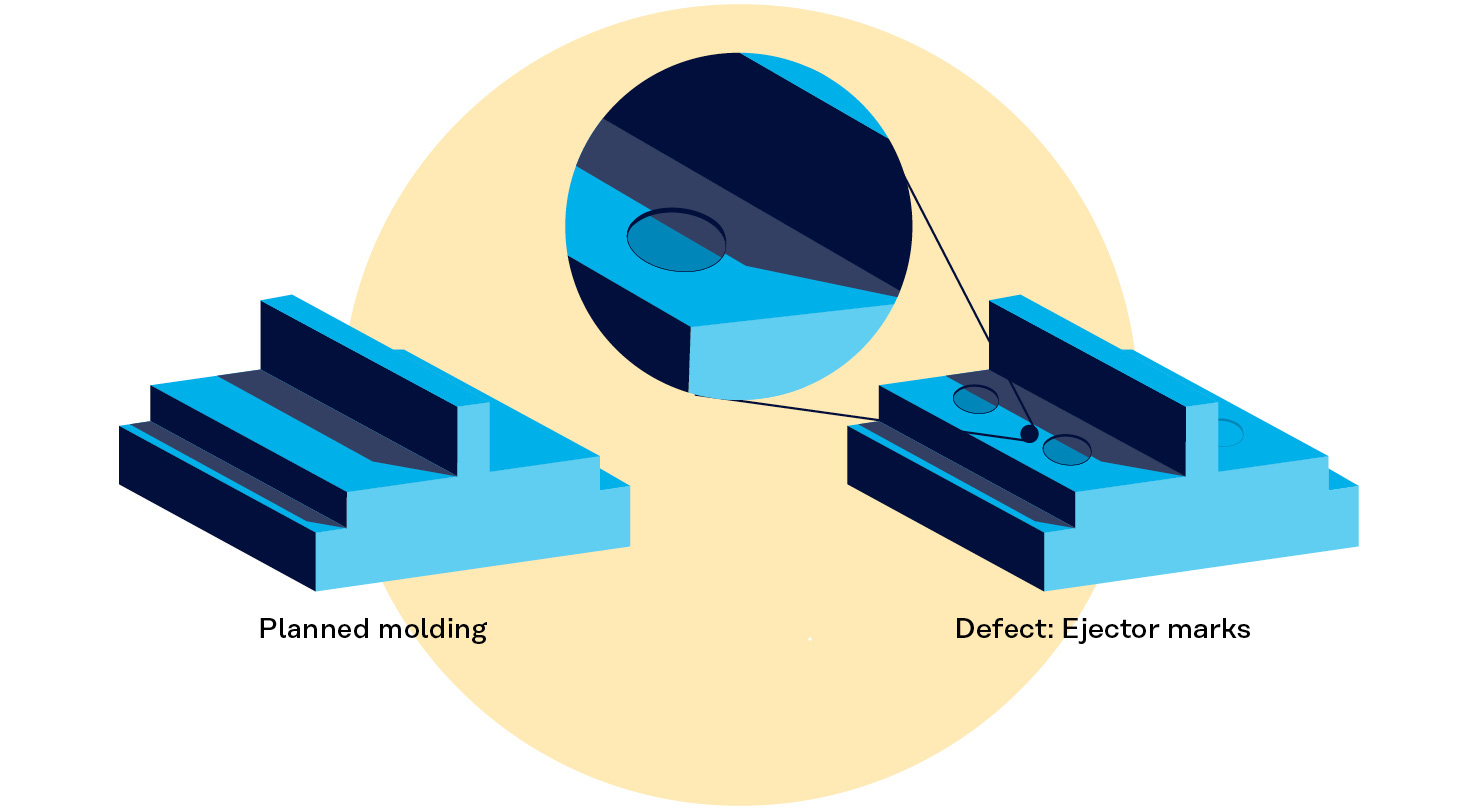
参考情報
クラレの原料は、射出成形における成形品の欠陥低減に役立つ優れた添加剤です。流動性や収縮といった重要な材料特性を改善することができます。
射出成形材料
すべての熱可塑性プラスチック、および一部の熱硬化性プラスチックとエラストマーは、射出成形に適した材料です。
射出成形で最も頻繁に使用される熱可塑性プラスチックは、ポリプロピレン(PP)、アクリロニトリル・ブタジエン・スチレン(ABS)、ポリエチレン(PE)、ポリスチレン(PS)です。
2Kおよび3K射出成形用の「柔らかい」材料としては、熱可塑性エラストマー(TPE)が最も多く加工されています。
射出成形に熱硬化性樹脂が使われるのは、かなり珍しいことです。その理由は、架橋密度が高いこと、再溶融して形を変えることができないこと、などです。しかし、一部の熱硬化性樹脂は、熱可塑性樹脂部品の特性を向上させるなど、特定の用途で添加剤として使用されています。
その材料は通常、小さなペレットまたは微粉末として入手することができます。液体の場合もあります。さまざまな添加剤を添加することで、成形品の特性や材料の加工性を向上させることができます。添加物の例としては、色をつけるための着色剤や、硬さを増すためのガラス繊維などが挙げられます。しかし、クラレの特殊エラストマーなど、さらに高度な添加剤もあります。
それぞれの材料は、目的の成形品を得るために、加工時に異なるパラメータを必要とします。これらは、射出温度、射出圧力、金型温度、排出温度、およびサイクルタイムなどを含みます。これらのパラメータをどのように設定するかによって、成形品の外観、寸法、機械的特性が大きく変化します。適切な技術に加えて、多くの経験が必要とされます。
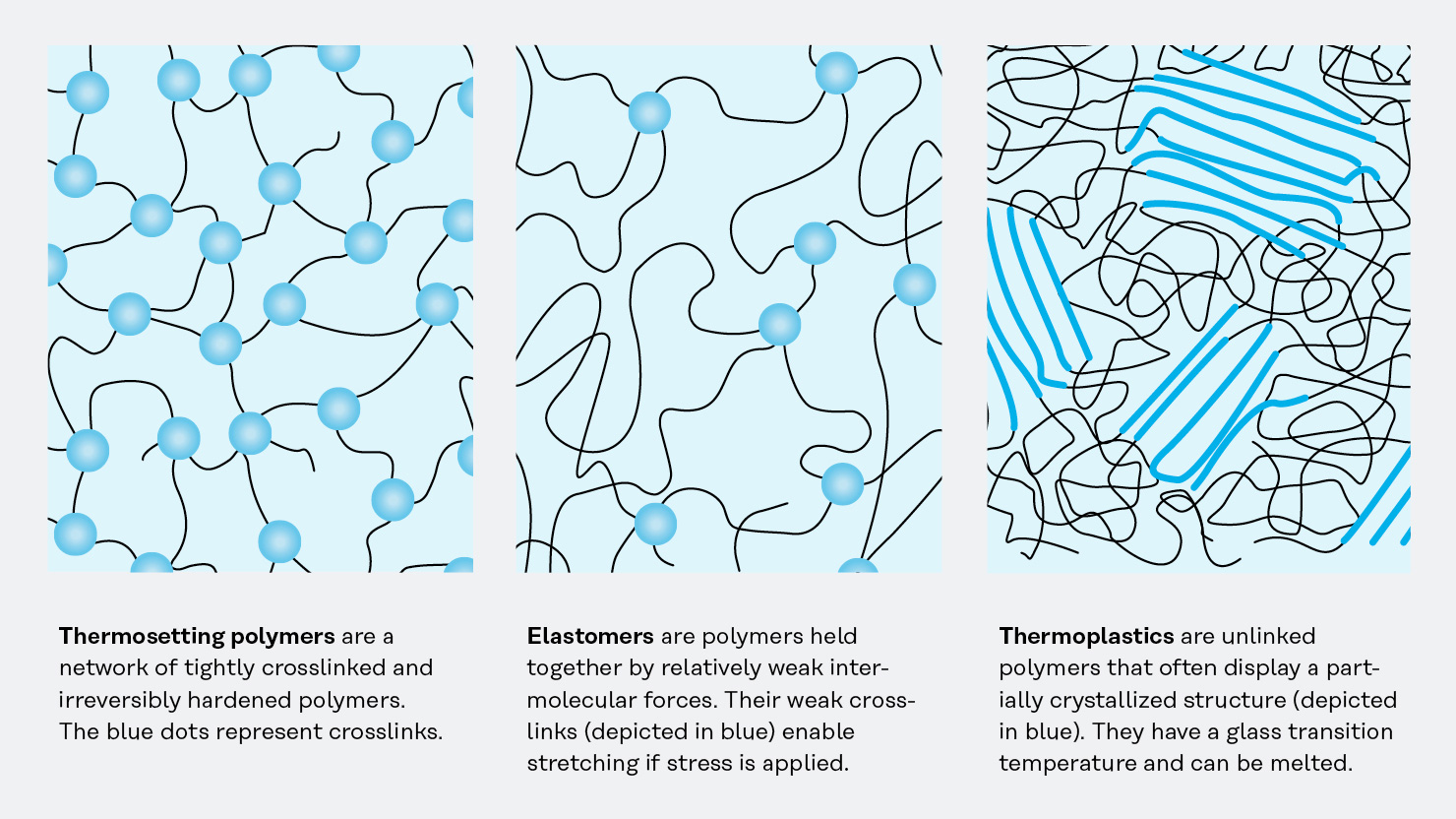
熱可塑性エラストマー
熱可塑性エラストマー(TPE)は、ゴムのような弾性と熱可塑性プラスチックの加工性を有する材料です。つまり、輪ゴムのように伸ばしたり、溶かしてさまざまな形や大きさに成形したりすることができるのです。冷めても弾力性は保たれます。必要であれば、後で再溶融し、再度成形することができ、加工時の材料廃棄物の削減にもなります。
TPEは加工しやすいため、射出成形に適した優れた材料です。ゴムとは異なり、加硫という時間のかかるゴムの加工方法は不要です。多様な用途があるため、多くの産業や目的に適した素材です。
さまざまな種類のTPEの材料特性の詳細については、以下の表を参照してください。
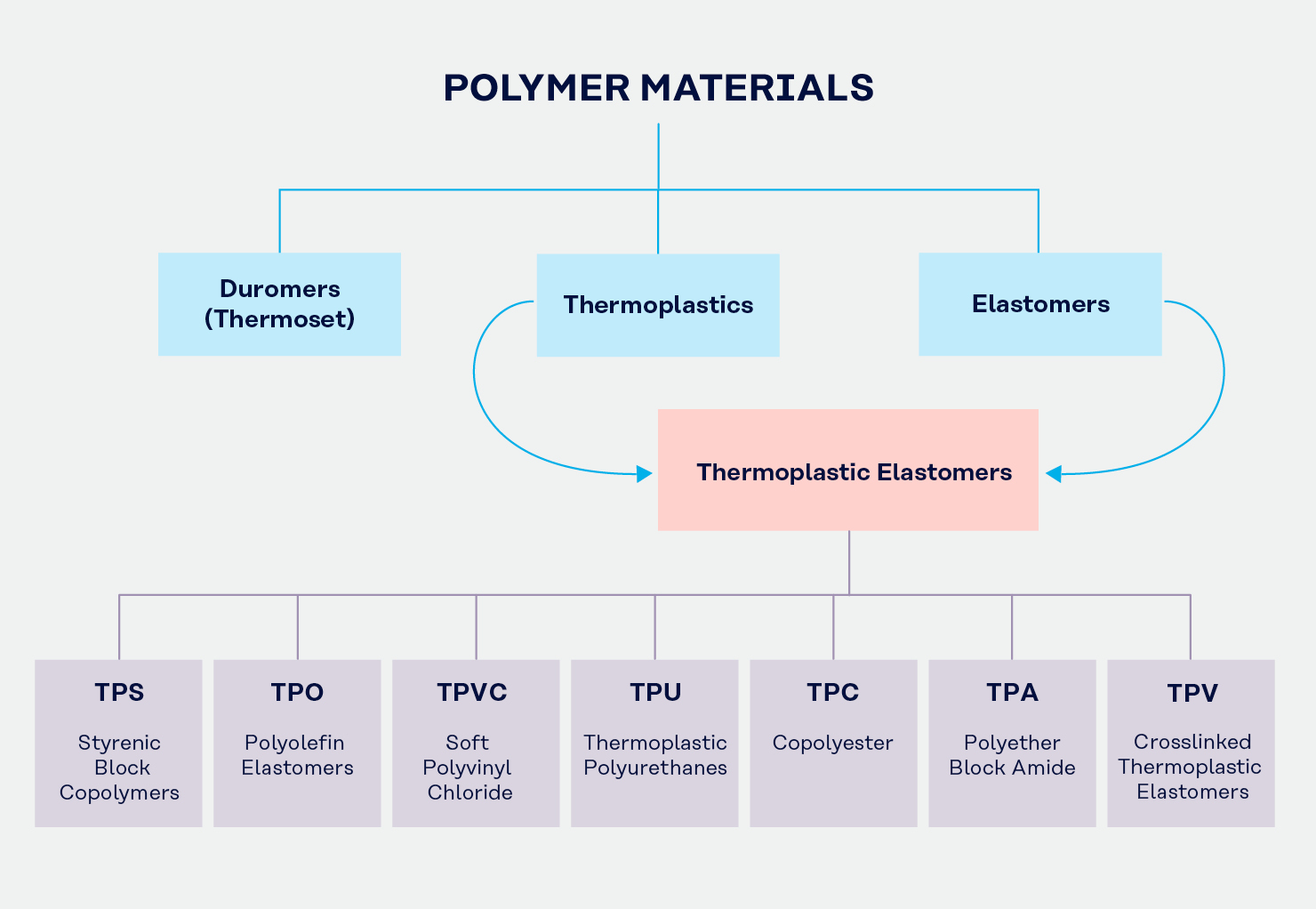
特性/材料 | TPS | TPO | TPVC | TPU | TPC | TPA |
ショア硬度 | 30A 〜 70A | 60A 〜 95A | 40A 〜 70A | 80A 〜 80D | 90A 〜 70D | 40D 〜 65D |
引張強度(MPa) | 9.8 〜 34.3 | 2.9 〜 18.6 | 9.8 〜 19.6 | 29.4 〜 49 | 25.5 〜 39.2 | 11.8 〜 34.3 |
伸び(%) | 500 〜 1,200 | 200 〜 600 | 400 〜 500 | 300 〜 800 | 350 〜 450 | 200 〜 400 |
反発弾性(%) | 45 〜 75 | 40 〜 60 | 30 〜 70 | 30 〜 70 | 60 〜 70 | 60 〜 70 |
密度(g/cm³) | 0.91 〜 0.95 | 0.88 | 1.2 〜 1.3 | 1.1 〜 1.25 | 1.17 〜 1.25 | 1.01 |
耐摩耗性 | △ | ⨯ | △ | ⦾ | △ | ○ |
室温での曲げ抵抗 | ○ | △ | ○ | ○ | ⦾ | ⦾ |
耐熱性 | 〜 80°C | 〜 120°C | 〜 100°C | 〜 100°C | 〜 140°C | 〜 100°C |
耐油性 | ⨯ | △ | ○ | ⦾ | ⦾ | ⦾ |
耐候性 | ⨯ 〜 ○ | ○ | △ 〜 ○ | △ 〜 ○ | △ | ○ |
脆化温度 | < -70°C | < -70°C | -50°C 〜 -30°C | < -70°C | < -70°C | < -70°C |
用途 | フットウエア、樹脂ブレンド、接着剤、アスファルト改質剤 | 自動車用ホース/チューブ、日用品 | 自動車用ワイヤ・ケーブル、土木・建築 | フットウエア、工業製品、日用品、医療製品 | 自動車、エレクトロニクス、工業製品 | スポーツ用品、工業用品 |
クラレの熱可塑性エラストマー
クラレは、より優れた材料特性を実現するために、射出成形用の高機能プラスチックを提供しています。完成部品であれ、柔軟なPVC/ゴム代替品であれ、これらのプラスチックの主要な特性は、製品に真の付加価値を与え、プロセスの効率化に役立ちます。
クラレの素材は、大規模なプラスチック部品の効率的な生産を促進します。クラレは、2K射出成形用として、柔軟な機能部品としての高機能TPEを提供しています。
セプトン™
セプトン™は、クラレが開発したスチレン系熱可塑性エラストマーです。水素添加スチレン系ブロック共重合体(HSBC)は、スチレン系硬質ブロックと水添ジエン系軟質ブロックで構成されます。HSBCは、硬質ブロックがポリスチレンのガラス転移温度以下の架橋点として働き、軟質ブロックが弾性を与えるため、ゴムのような弾性を示します。水素化により、優れた耐熱性と耐候性を実現します。
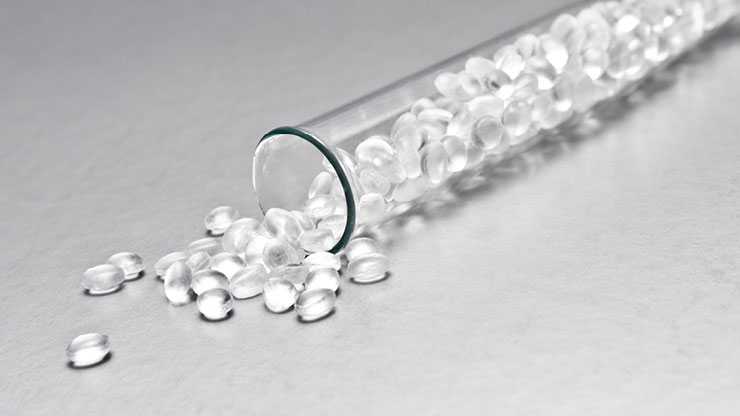
メリット
ポリオレフィンにセプトン™と可塑剤を添加することにより、良好な射出成形性と柔軟な成形品を得ることができます。
セプトン™のSEEPSグレードを使用することで、エンボス転写性が向上し、インサート成形における接着性も改善されます。
セプトン™ BIOシリーズ
セプトン®バイオシリーズは、クラレ独自の水素添加スチレン-ファルネセン系ブロック共重合体(HSFC)であり、クラレはバイオベースのHSBC材料市場で最初かつ唯一のメーカーです。セプトン™ BIOシリーズの熱可塑性エラストマーは、バイオ由来成分を多く含む新しい化合物や最終用途を可能にし、既存の市場分野を拡大し、新しい市場分野を開拓する、メーカーにとっての新しいソリューションです。
その他のメリットについては、セプトン™に関する前セクションを参照いただくか、営業部にお問い合わせください。
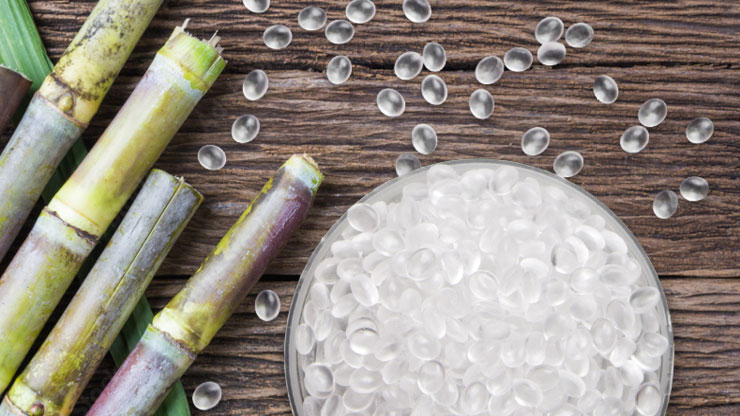
ハイブラー™
ハイブラー™は、ポリスチレンの末端ブロックとビニル結合リッチポリジエン中間ブロックで構成される、実にユニークなトリブロック共重合体です。室温付近でtanδのピークを示すため、ハイブラー™は、可塑剤が配合されていなくても、高い振動減衰特性と衝撃吸収特性を示します。これらのTPEは、耐久性のある水添系銘柄と未水添系銘柄があります。
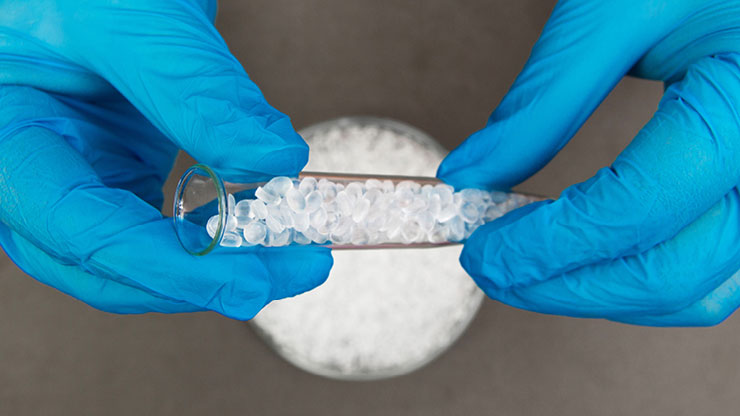
メリット
ポリプロピレンに少量のハイブラー™を添加することで、結晶化度を下げ、透明性を向上させることができます。
透明なTPE、クラリティ™
クラリティ™は、クラレ独自のリビングアニオン重合技術により、各種(メタ)アクリレートをA-B型またはA-B-A型のブロック共重合体に結合させたアクリル系ブロック共重合体の新シリーズです。熱可塑性エラストマークラリティ™は、その構造上、優れた透明性、耐候性、自己接着性、他の極性材料との良好な相溶性など様々な特性を発揮します。
クラリティ™単独でも射出成形が可能です。ただし、クラリティ™はPC、PC/ABS、PLA、HSBC、PVCなどの極性プラスチック樹脂への添加剤としても使用でき、柔軟性とメルトフローを向上させることができます。クラリティ™を使用した混合物は、低分子量樹脂に比べて高い耐衝撃性を特徴としています。可塑剤に比べ、ブリードアウトが少ないです。
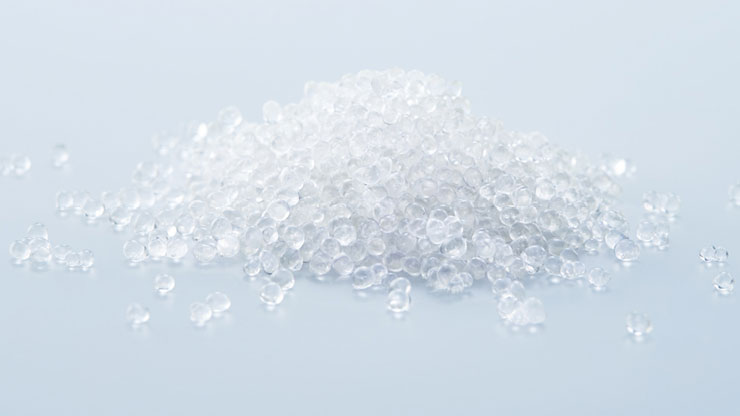
コアシェル・ゴムと比較した利点
- 成形部品は優れた表面外観と高い光沢が得られます
- 薄肉成形性と大型成形性の向上
- フローマーク欠陥の低減
- 成形部品の残留応力低減
- 耐ソルベントクラック性の向上
液状ゴム
液状ゴムは、ゴムやプラスチックの「反応性可塑剤」または改質剤として広く使用されており、射出成形にも使用できます。液状ゴムは低分子量の液状ポリマーで、固形ゴムと同じ化学構造を持ちます。
液状ゴムは、室温では液状ですが、鎖の伸長と架橋によりゴムのような性質を示します。液状ゴムの例としては、以下のようなものが挙げられます。
- 液状ブタジエンゴム、液状イソプレンゴム、液状スチレンブタジエンゴムなどの液状ジエン系ゴム
- 液状シリコーンゴム
- 液状オレフィンゴム
- 液体ウレタンゴム
クラレ液状ゴム
クラレ液状ゴムは架橋可能な液状ゴムです。液状ブタジエンゴム(L-BR)、液状イソプレンゴム(L-IR)、液状スチレンブタジエンゴム(L-SBR)で構成されます。液状ゴムは無色透明でほとんど無臭で、VOC値も低いです。ブタジエン、イソプレン、スチレンのポリマーは分子量が低く、固形ゴムと可塑剤の中間に位置します。
クラレ液状ゴム製品は「反応性可塑剤」として設計されています。時間と手間のかかるゴム混合プロセスにおいて、ムーニー粘度を下げ、混合プロセスを容易にします。その結果、化合物の流動性が向上し、所要時間が短縮され、処理コストが削減されます。
また、クラレ液状ゴム製品はベースゴムとの共加硫が可能で、移行性を抑制します。移行性が大幅に減少したことで、製品の保存期間と耐久性が大幅に向上します。
クラレ液状ゴムはゴム配合物の射出成形に適しています。
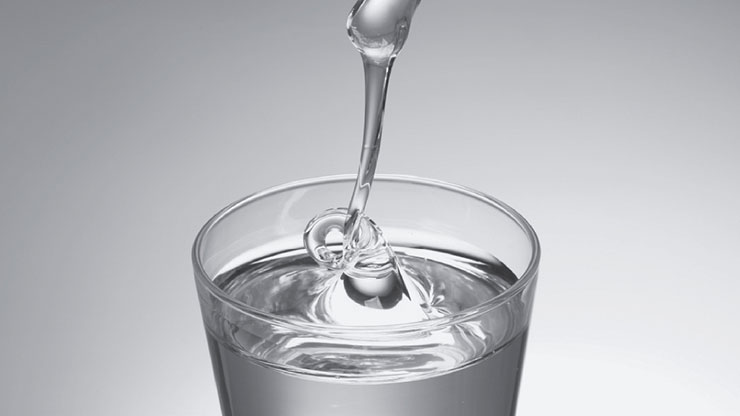
メリット
クラレ液状ゴムーは、ゴム配合物の射出成形プロセスをいくつかの方法で向上させることができます。
- 流動性: 加工助剤として、溶融粘度を下げ、ゴム配合物をより流動的にし、金型のキャビティに注入しやすくします。これにより、材料が金型の空洞の狭い隅々まで届き、表面が目に見えて改善され、その結果、金型がより正確に再現されます。
- エネルギー消費の削減: 配合物の流動性が向上することで、混合・成形プロセスの効率が大幅に向上します。クラレ液状ゴムは成形温度を下げることができ、エネルギー消費を抑えることができます。
- 特性と性能: クラレ液状ゴムは最終ゴム製品の特性や性能、すなわち耐摩耗性や低温での柔軟性を向上させることができます。さらに、クラレ液状ゴムは通常の可塑剤と比較して、移行性を低減し、最終ゴム製品の保存性や耐久性を向上させることができます。
参考情報
ゴム配合物に添加するクラレ液状ゴムの最適添加量はさまざまな要因によって異なります。お問い合わせクラレ液状ゴムが射出成形でどのような結果をもたらすかについて、詳しくはお問い合わせください!
液状ファルネセンゴム
持続可能性を重視しますか?
液状ファルネーゼゴム(LFR)は、再生可能な天然原料をベースにしています:再生可能なモノマーであるβ-ファルネセンの重合体を含んでいます。確立された発酵プロセスにより、独自の酵母株がサトウキビなどの糖源をβ-ファルネセンに変換します。
液状ファルネセンゴムは、標準的な可塑剤よりも分子量が大きい反応性可塑剤として機能します。液状ファルネセンゴムは共加硫可能で、移行性を大幅に低減させることで、ゴム配合物の耐久性を向上させます。
当社の製品とその優れた加工能力について、さらに詳しくお知りになりたいですか?クラレ担当者までご連絡ください。
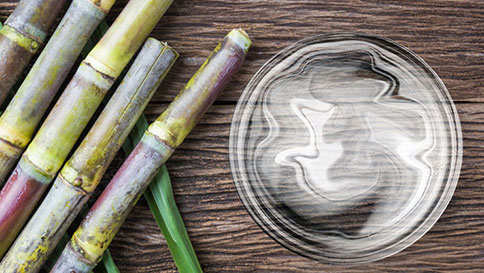
その他の材料
プラスチックだけでなく、金属などさまざまな材料を射出成形に使うことができます。しかし、金属の射出成形プロセスは、一般的にダイカストと呼ばれています。
射出成形:利点
射出成形の主な利点は、部品を大量に生産できることです。数百個の小ロットから数百万個の大量生産まで、幅広い用途に対応します。
初期投資が償却されれば、この製造方法では単価は極めて低くなります。ユニット数が増えれば、単価を大幅に下げることができます。これにより、このプロセスは非常に生産的なものとなります。
射出成形のその他の利点には、高い再現性と耐久性、幅広い材料、低いスクラップ率、成形品の魅力的な外観などがあります。
デメリット
射出成形の大きな欠点は、金型製作にかかるスタートアップ費用が高いことです。
また、プロセスに適合させるために金型の設計を変更する必要がある場合や、設計ミスが生じた場合にも、コストがかかる可能性があります。小さなミスでも、ここでは大きなコストにつながります。
その他の欠点としては、スタートアップに時間がかかること、大型の金型では制約を受ける可能性があることなどが挙げられます。
用途
射出成形は、消費財(歯ブラシ)、家具(椅子)、自動車(ダッシュボード)、電子機器(電動工具のハウジング)、玩具(プラスチック積み木)、ヘルスケア(注射器)、包装(スクリューキャップ)など、さまざまな業界で使用されています。
歴史
射出成形の発明者はアメリカのジョン・ウェスリー・ハイアットです。1871年、兄のアイザイアとともに最初の射出成形機の特許を取得しました。当時はまだ、加熱されたシリンダーからピストンを使ってプラスチックを金型に注入するという、かなり単純な機械でした。ボタン、櫛、ビリヤードのボールなどの製造に使われました。
1903年、ドイツの化学者アーサー・アイヒェングリューンとセオドア・ベッカーは、粉末状で容易に射出成形できる最初の可溶性酢酸セルロースを発明しました。1919年に初の射出成形用プレスを開発し、その20年後に可塑化酢酸セルロースの射出成形で特許を取得したのもアイヒェングリューンでした。
第二次世界大戦中、安価な大量生産品への受容の高まりから、この産業は力強く拡大しました。1946年、アメリカのジェームズ・ワトソン・ヘンドリーは、最初のスクリュー射出成形機で画期的な開発を行いました。射出速度と成形品の品質をより正確に制御できるだけでなく、射出前に材料を混合することも可能になりました。
1970年代にヘンドリーが開発したもうひとつの技術、ガスアシスト射出成形法は、複雑な中空成形品の製造を可能にし、射出成形部品の設計の柔軟性、強度、表面仕上げを大幅に改善しました。
今日、射出成形は年間数千億ドルを売り上げる世界市場です。世界では、毎年およそ5,500万トンのプラスチックがこの方法で加工されています。
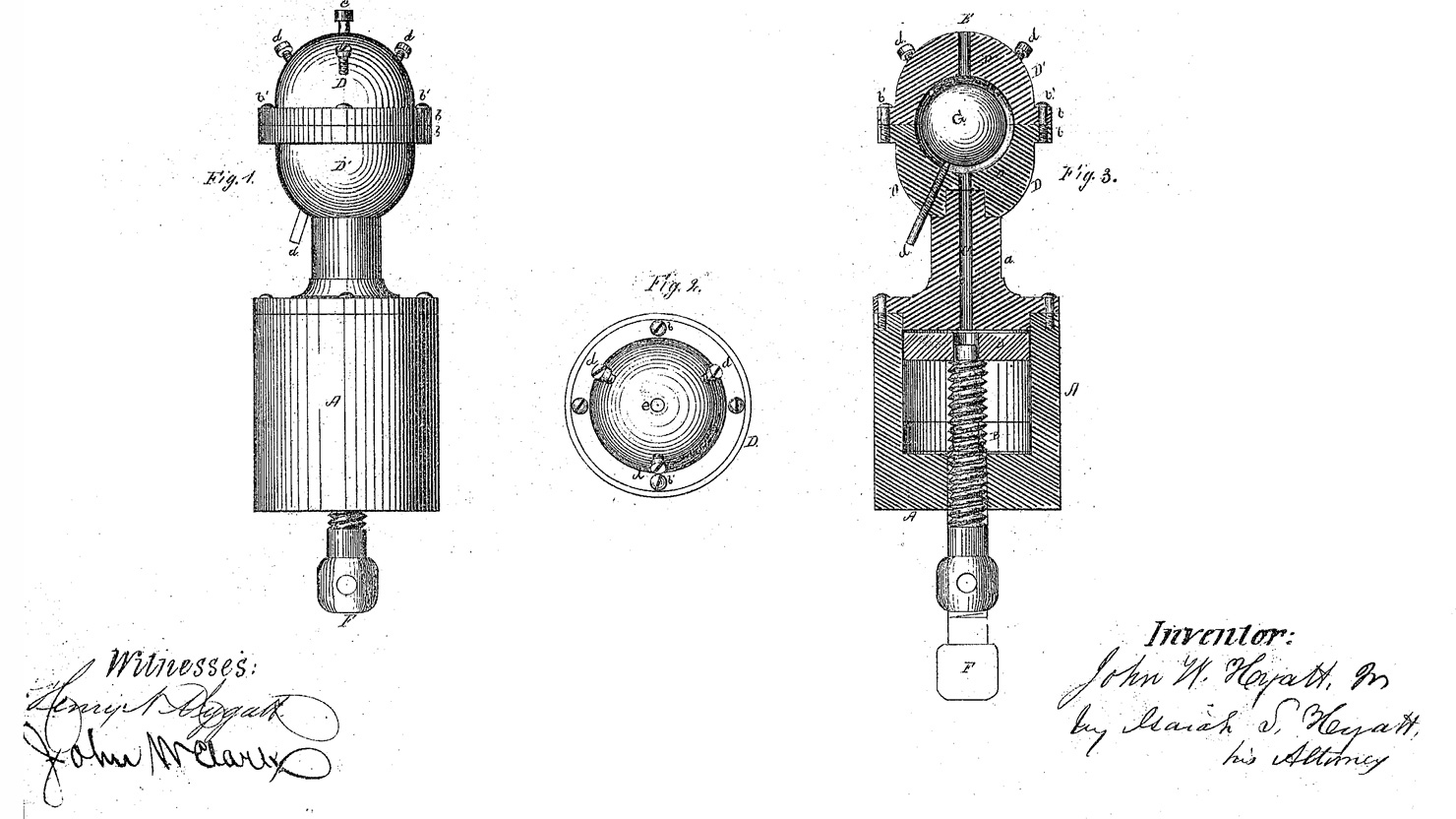
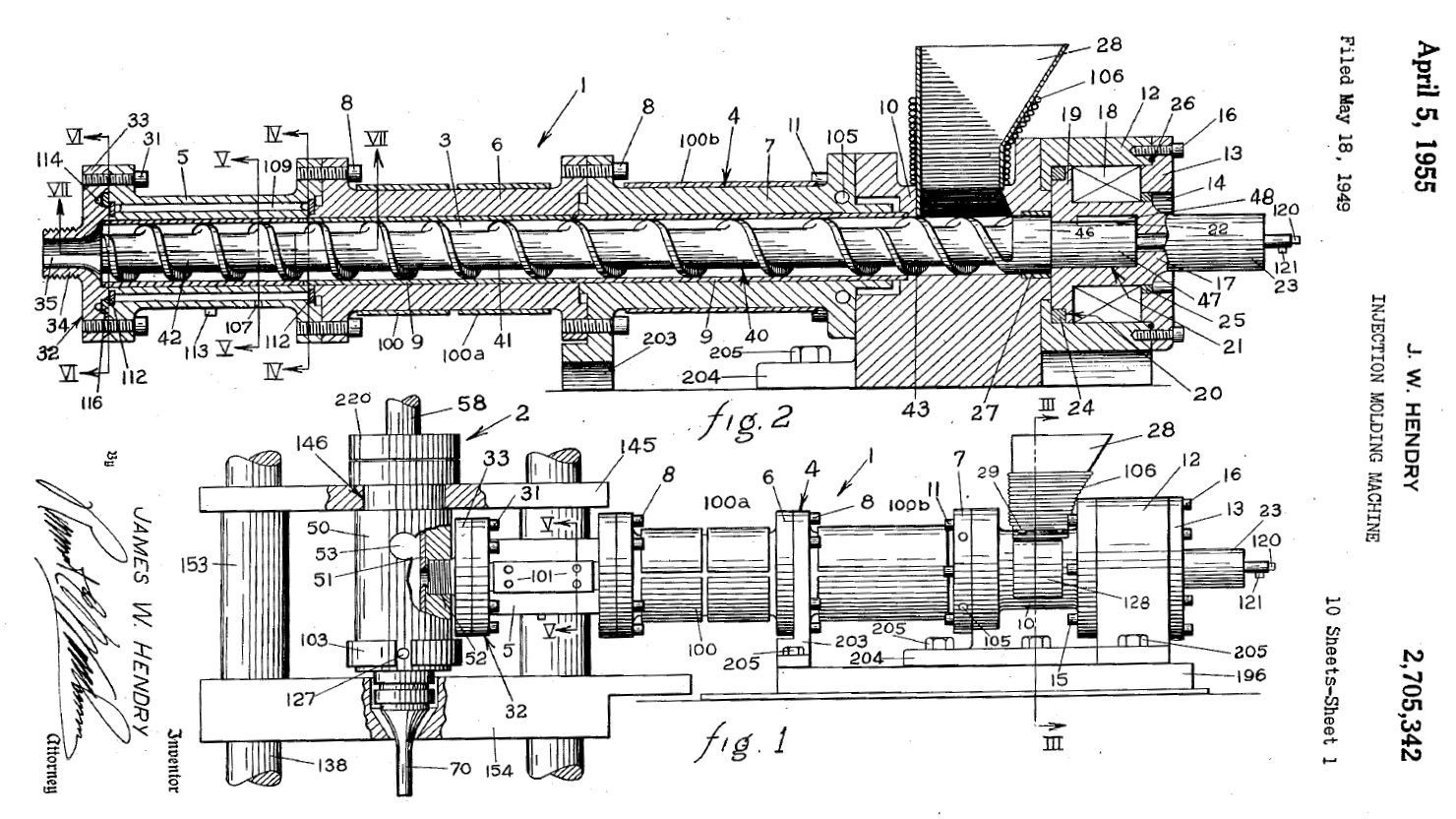
規格と認証
射出成形サービス業者の資格を確認できる認証は数多くあります。特に重要なのはISO9001認証です。
米国プラスチック工業会(SPI)は、さらに米国のプラスチック業界向けにプラスチックの光学的品質に関する基準を定めています。この規格は、射出成形プラスチック部品の表面品質を4つのカテゴリーに分け、12種類の表面品質を区別して定義しています。
コスト
射出成形は、成形部品を大量に生産する上で、大きな利点があります。しかし、このプロセスを選ぶ人は、スタートアップのコストにも注意する必要があります。初期投資が非常に高額になります。射出成形機に加え、金型にかかる費用は特に大きく、時には数百万円にもなります。
以下はあなたにとって興味深いかもしれません。クラレは、射出成形プロセスの可能な限り高い収益性を実現するために、サイクルタイムの短縮と生産の最適化を実現する配合物の開発をサポートします。
作りたい製品の明確なイメージはあるものの、材料の配合や構成に自信がないですか?それでしたら、クラレの担当者にご連絡ください。必要であれば、私たちのプロセスや材料に関する専門知識を駆使し、サプライチェーンの編成をサポートさせていただきます。
お問い合わせ
お問い合わせをお待ちしております!
お問い合わせ