What is a hot melt adhesive (HMA)?
Hot melt adhesives, or HMAs, are fully solid adhesives based on thermoplastic polymers. When heated to its softening point, usually somewhere between 80 °C and 150 °C, a hot melt adhesive becomes a liquid that can be applied to a substrate. The HMA flows across the substrate’s surface filling gaps and forming a bond as it cools and sets. While some HMAs remain tacky after they cool (known as pressure-sensitive adhesives, or PSAs), most form strong, solid bonds between surfaces until they are heated again.
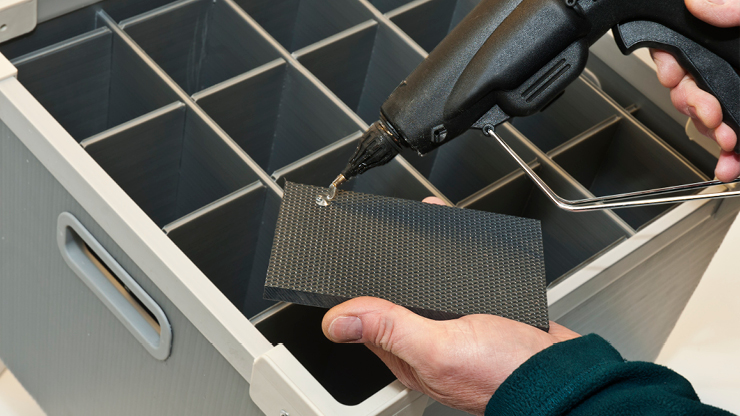
Advantages
Although solvent-based adhesives were once the preferred option due to their generally stronger bonding capabilities, hot melt adhesives are growing increasingly popular for many applications thanks to their low cost, ease of use, and great properties in a range of temperatures.
One significant advantage of hot melt adhesives is their fully solid formulation. Unlike solvent-based options which rely on volatile and often dangerous solvents to carry their adhesives, HMAs are solid and include few or no volatile organic compounds (VOCs). This makes them less expensive, easier to transport and store, safer and more convenient to work with while being more environmentally friendly.
Since they solidify quickly as they cool, HMAs offer shorter set times that can be adjusted to fit the needs of an application with no need for a curing step. This speed means faster production times for goods manufactured with the HMA and a more cost-effective adhesive overall.
HMAs are extremely versatile, bonding readily to all kinds of substrates including plastic, metal, glass, rubber, ceramics, wood, cardboard, and foam. The long shelf life, ability to bond to both porous and non-porous substrates, and variety of use cases make it possible for some facilities to use just a single hot melt adhesive for all of their needs further reducing costs.

Disadvantages
Although hot melt adhesives are becoming the preferred choice for many substrates, there are still a few applications for which solvent-based adhesives are preferable.
The largest disadvantage of hot melt adhesives is their temperature sensitivity. If the substrate would be damaged by the heat of a molten HMA being applied or if the product must survive exposure to high temperatures at which the HMA used would soften or melt, a solvent-based adhesive may be a better solution. These downsides can be mitigated using reactive HMAs with an extra curing process through exposure to moisture or UV light.
Some hot melt adhesive formulations are less resistant to chemical attack and weathering. The average HMA tends to form weaker bonds between substrates than a solvent-based adhesive. The short open and set times of HMAs can also make them difficult to work with in some cases. Although all of these disadvantages can be addressed through changes to the formulation, solvent-based options may be less expensive solutions in specific applications.
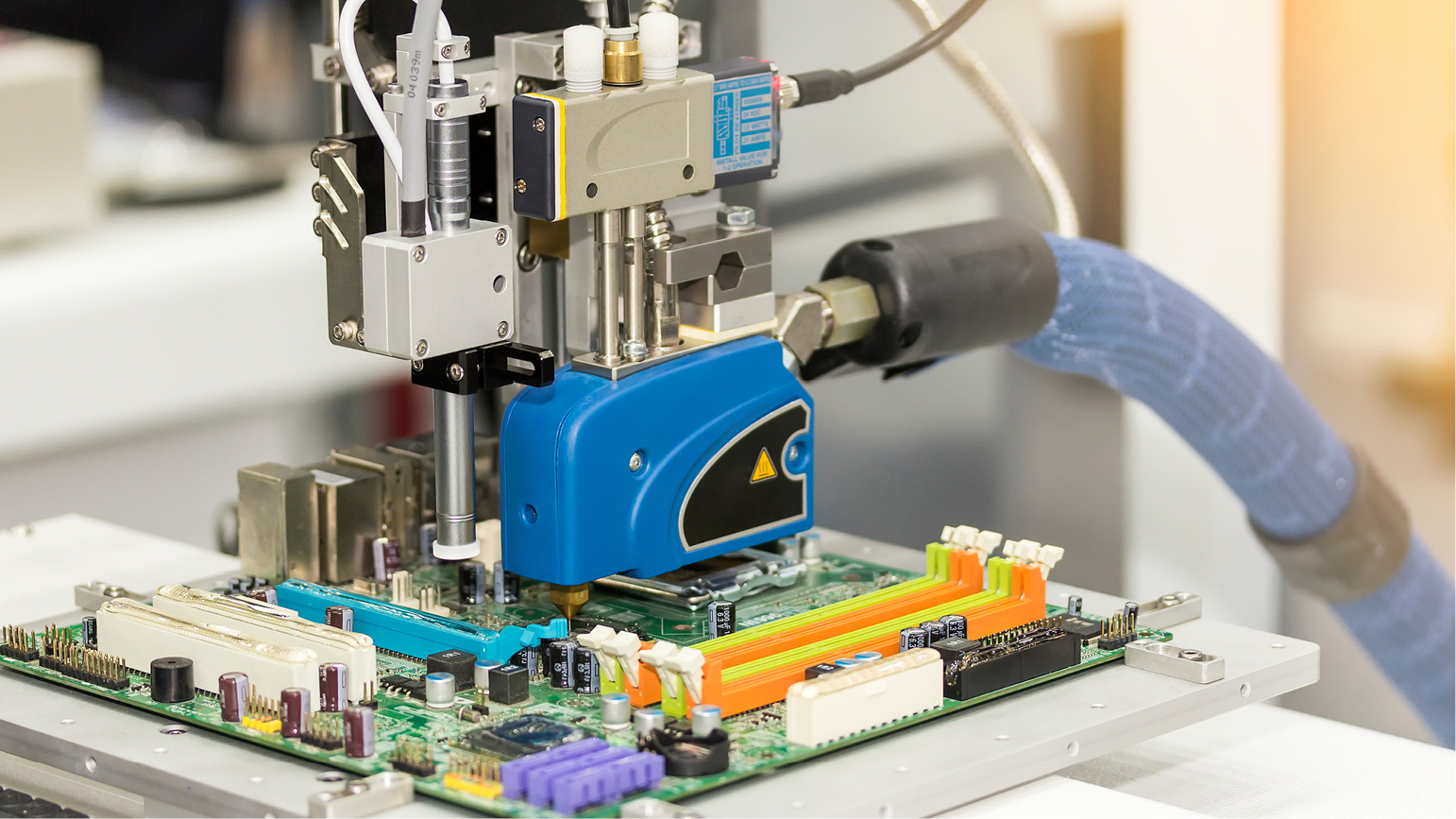
Properties
Hot melt adhesives come in a variety of formulations to fit applications ranging from bookbinding to automotive manufacturing. To identify the HMA that’s right for you, it’s important to consider properties such as viscosity, open and set times, adhesive strength, application temperature and more.
Viscosity
An HMA’s viscosity is an important factor in determining the type of hot melt applicator and application temperature. The viscosity is measured using a Type B rotational viscometer at 180 °C or the usage temperature. Shear rate is also often considered when measuring viscosity.
Open and set times
An open time measures the length of time between application of a HMA to the first substrate and compressing the second substrate at which adhesion occurs. Many HMAs feature shorter open times making them harder to work with but more efficient while some pressure-sensitive HMAs have effectively unlimited open times.
Set time measures the length of time it takes a HMA to cool and form an acceptable bond. Shorter set times increase production speed and are one of the major advantages HMAs have over some slow-setting solvent-based adhesives.
Key working temperatures
The temperatures at which a HMA softens and melts are two of the most important factors in choosing an adhesive. The softening point is the temperature at which a HMA begins to flow and is mainly determined by the base polymer and wax additives in the formulation. The softening point is an important consideration for workflow and the heat-resistance temperature of the final product.
The bond-formation temperature of a HMA is the temperature at which the molten adhesive cools and forms the bond to the substrate. A hot-melt adhesive is applied to a substrate, bonded to another substrate, and then forms the bond during cooling. When the adhesive cools below the temperature at which it has sufficient wettability to spread over the substrate, it reaches the bond formation temperature.
Adhesive failure temperatures
A HMA’s failure temperature measures the greatest heat it can withstand by identifying the temperature at which the adhesive is no longer strong enough to hold two substrates together. This is typically lower than the softening point as the HMA begins weakening before it fully melts. Failure temperatures are usually measured as either peel adhesion (whether the HMA can resist a peeling force) or shear adhesion (whether the HMA can resist a shearing force).
A HMA’s cold crack temperature measures the lowest temperature it can withstand without failing by identifying the temperature at which the adhesive becomes brittle enough to crack. Cold crack temperature is identified by exposing an HMA to successively lower temperatures while applying a bending force.
Pot life stability
This metric assesses the stability of a HMA when it is kept in a molten state over prolonged periods and is particularly relevant in industrial applications. The HMA is heated and is observed for charring, decomposition, gelling, changes in viscosity or color, and formation of edge rings or skins.
Mechanical properties
A HMA’s mechanical properties will vary widely depending on its formulation and intended use. Important properties include tensile strength, elongation at break, elastic modulus, and more.
Peel strength and substrate-specific adhesion
Peel strength measures the amount of force applied at various angles required to break an adhesive bond between two surfaces without the application of heat. This is usually a direct measurement of how strong the adhesive will be in the typical conditions the product will be exposed to.
Substrate-specific adhesion measures the amount of force required to peel apart two specific substrates joined by a HMA. Adhesion between two substrates is also often tested at a variety of temperatures.
Loop tack strength
A loop tack test assesses the stickiness or tackiness of a pressure-sensitive adhesive by measuring the force required to pull a loop of material coated with the adhesive free of another substrate. This value is only relevant for the hot melt adhesives that are pressure-sensitive.
Raw materials and additives
A hot melt adhesive is usually composed of a base polymer and additives including tackifier resins, waxes, and antioxidants that give it the desired properties.
Polymers
An adhesive’s polymer is the base material that influences many of its physical properties including its strength and viscosity. Polymers with higher molecular weight tend to provide stronger bonds, greater heat resistance, and slower wetting, but all of these properties can be fine-tuned through other additives.
Tackifier resins
These resins, which must be compatible with the main polymer, often make up a significant percentage of the HMA and determine its stickiness and adhesive power. They work by reducing the modulus and increasing the glass transition temperature of the HMA. They can also lower the viscosity of the HMA. Most tackifier resins are either hydrocarbon, rosin, or terpene resins.
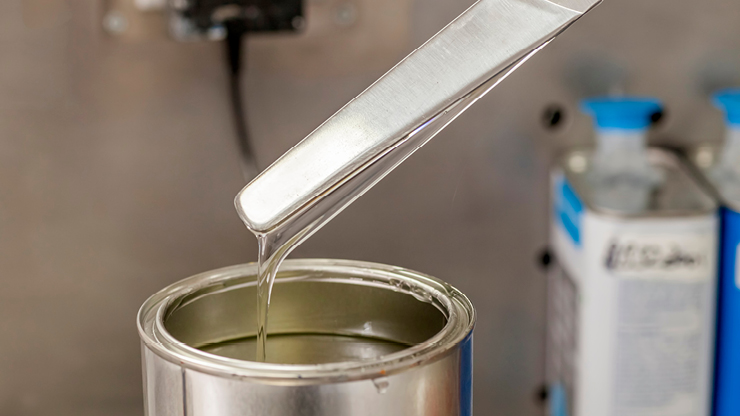
Waxes
Waxes are additives that lower the viscosity of the melted HMA and increase how quickly the adhesive sets. By adjusting wax content, the open and set times of an adhesive can be increased or decreased. Waxes can also be used to influence the heat resistance of a HMA.
Antioxidants
These compounds, which include various phenols and phosphates, are added in small amounts to improve the shelf life of the HMA and any product manufactured with it. They also protect against oxidation while the HMA is molten, improving its pot life stability.
Plasticizers
Many HMAs include plasticizers which can lower viscosity and improve wetting, flexibility, and toughness.
Other additives
Additives are often included in HMA formulations for specific applications. These include fillers, pigments, UV stabilizers, flame retardants, antibacterials, and more.
Types of hot melt adhesives
Although most hot melt adhesives use ethylene-vinyl acetate or polyolefin polymer, there are many other types of HMA’s that excel in specific applications.
Ethylene-vinyl acetate (EVA)
EVA hot melts are commonly used thanks to their low cost, broad temperature range, and ability to bond to a wide variety of substrates. When the concentration of ethylene or vinyl acetate is increased, the resulting HMA bonds better to either nonpolar or polar substrates. EVA hot melts are widely used in the paper and packaging industries.
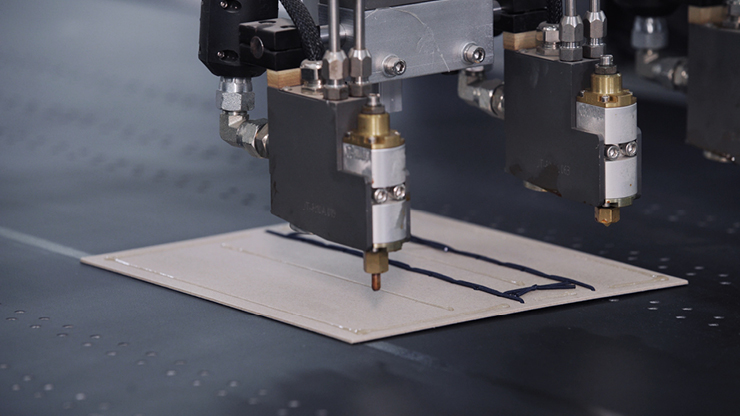
Polyolefin (PO)
Polyolefin hot melts excel at bonding to nonpolar substrates such as plastics. They provide excellent pot life stability, thermal and UV stability, and chemical stability against many common solvents, making them useful in industries from product assembly to woodworking.
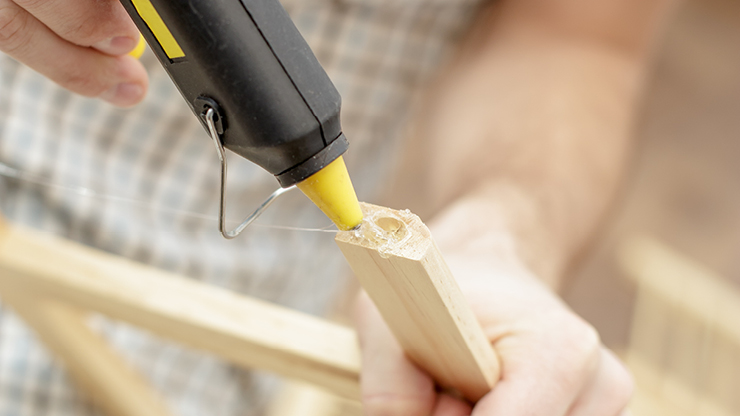
Polyamide (PA) and polyester
Polyamide and polyester hot melts can maintain their full peel strength above 100 °C in many formulations, are useful for high-temperature applications, resistant to oils and solvents, and are excellent at bonding to metals. They are commonly used in automotive assembly, electronics, and aerospace applications.
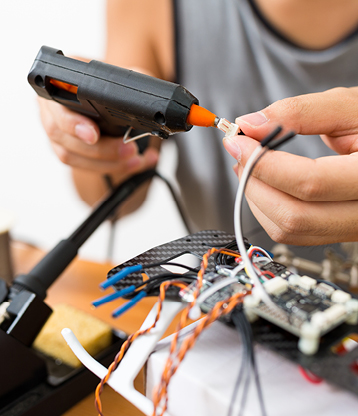

Polyurethane (PUR)
These HMAs are excellent in high-temperature applications and can be formulated to cross-link after a secondary curing leaving them stronger after they’re applied. Although more expensive, these strong and flexible HMAs are used in many industries.
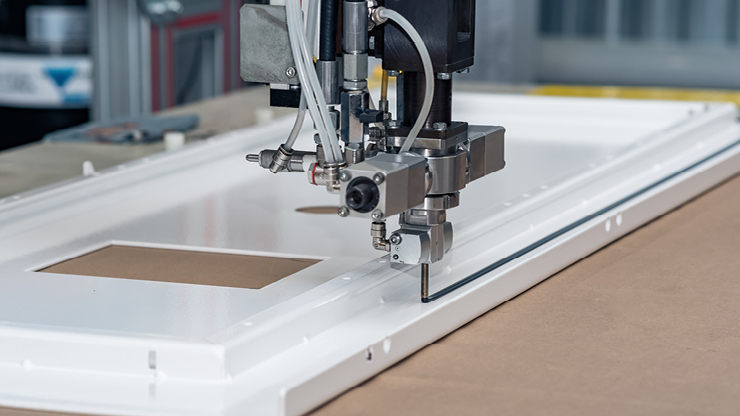
Styrenic block copolymer (SBC)
These thermoplastic elastomers provide less strength but excellent elasticity and flexibility at low temperatures. HMAs based on styrenic block copolymers are most commonly used in pressure-sensitive adhesives.
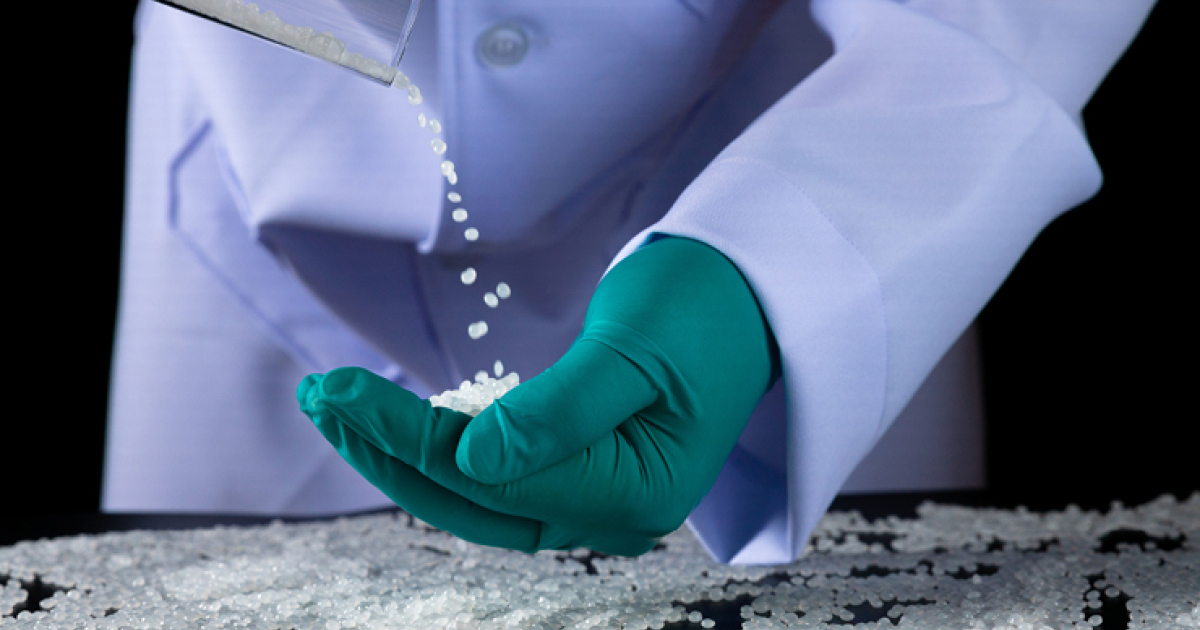
SEPTON™ and HYBRAR™ are styrene-based block copolymers (SBCs) manufactured by Kuraray. They combine the benefits of rubber-like elasticity and thermoplastic properties. When used as the base polymer for HMA, or as a modifier for polyolefin-based HMA, their flexibility, stretchability, and cohesion enhance adhesive durability, tackiness (pressure-sensitive adhesion), low-temperature performance, and impact resistance. Additionally, their excellent compatibility with polyolefins allows for HMA’s suitable for bonding and adhering to polyolefin materials. SEPTON™ and HYBRAR™ find applications in tapes and labels, hygiene products (such as diapers and sanitary napkins), sealants and protective films.
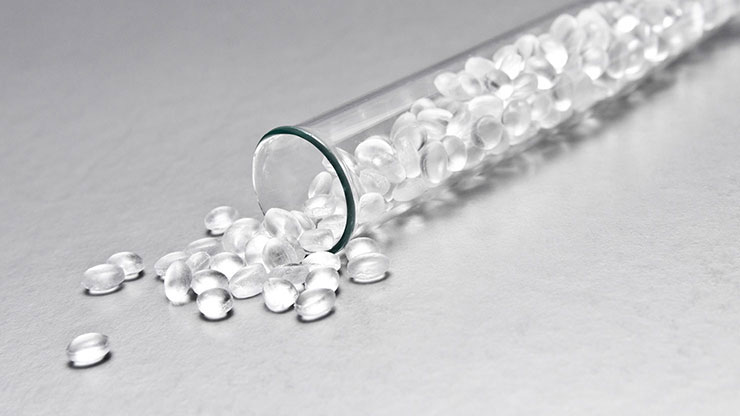
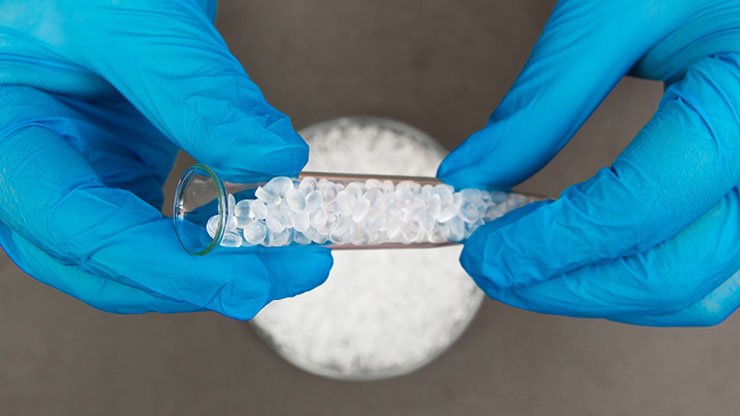
Acrylic block copolymer
KURARITY™ is an acrylic, adhesive polymer from Kuraray that can be used as a hot melt for solvent-free processing. Unlike most acrylics, KURARITY™ has a low melt viscosity suitable for hot melts and offers excellent weatherability and adhesive stability. As a self-adhesive polymer, HMAs based on KURARITY™ require lower concentrations of tackifier resins—an expensive component in a hot melt—to achieve strong adhesion. HMAs produced with KURARITY™ provide all the benefits of a solvent-free process including faster and simpler processing, lower energy consumption and greenhouse gas emissions, and fewer VOCs.
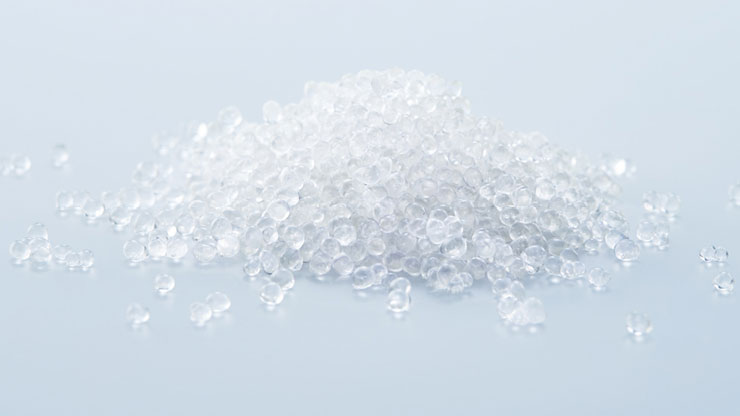
Bio-based hot melt adhesives
While the majority of HMAs are based on synthetic, non-renewable polymers, interest in plastics and adhesives that are bio-based or biodegradable is growing. Some companies have begun developing bio-based HMAs to deliver a greener material.
Hot melt application
While hot melt adhesives can be applied in many ways, industrial applications usually favor one of the three approaches below.
Spray application
This method uses compressed air to spray a continuous, uniform layer of specific thickness onto the substrate. It’s fast, effective, and often used over large surface areas.
Slot coating
This method, which is ideal for thin substrates or pressure-sensitive adhesives, directly applies a thin layer of hot melt adhesive to the substrate.
Bead and line application
In this method, a nozzle dispenses a specific amount of adhesive and is cut off. This process is then repeated, applying adhesive either to a specific location or in beads or lines as required.
Industries
As the capabilities of hot melt adhesives continue to expand, they are being adopted by a wider variety of industries. HMAs are used in applications including packaging, carton-making, tapes and labels, electronics, product assembly, automotive, apparel, hygiene products, and woodworking.
Cost
Although the price of HMAs may vary widely depending on the polymers and additives they contain, they are generally less expensive than their solvent-based counterparts.
The low cost of HMAs is mainly driven by a lower base material cost, increased production efficiency, lower maintenance costs, better elasticity, and longer shelf life. The versatility of HMAs even allows some production centers to use a single hot melt for all of their products, minimizing inventory costs. The main driver of increased HMA costs is the price of additives, especially tackifier resins.
Conclusion
Hot melt adhesives are a versatile option that provide excellent customization and many advantages over solvent-based adhesives. For an acrylic polymer HMA base with excellent weatherability, stability, and self-adhesion that reduces the need for expensive tackifier resins, get in touch with our experts at Kuraray and ask about KURARITY™, the transparent TPE.
Contact