Bio-based polymers and plastics
In the past, almost all plastics and polymers were fossil-based. For some years now, there have also been bio-based polymers on the market. These are produced using renewable raw materials (biomass). Bio-based polymers are products where at least part of the polymer is made from materials derived from renewable raw materials such as sugar cane or corn. The remainder of the polymer may comprise carbon obtained from fossil resources. Greater use of bio-based materials could help reduce the climate impact of polymer production, making it more sustainable. As a supplier of bio-based polymers, Kuraray has put together the following information on the present situation in this small but promising future-oriented segment of the plastics industry.
Petroleum-based plastics
vs. bio-based plastics
Bio-based polymers are sustainable polymers synthesized from renewable resources such as biomass rather than conventional petroleum feedstocks such as oil and gas. In most cases, synthesis is based on biological or biochemical processes. These bio-based products are carbon-neutral or offset carbon emissions. In other words, combustion does not increase the carbon dioxide concentration in the atmosphere.
Intensive use of fossil resources such as oil, coal and gas adversely affects climate change. There is a direct correlation between climate change and the greenhouse gas effect, which is caused by an increase in the concentration of greenhouse gases in the atmosphere. The most common greenhouse gas is carbon dioxide (CO₂), which is released in the combustion of fossil-based resources. Using more renewable resources would reduce the greenhouse effect and CO₂ emissions into the atmosphere.
When humans introduce fossil-based resources into the carbon cycle, they disturb the natural balance. Increasing the release of carbon dioxide from fossil-based products (fuels, chemicals, plastics, etc.) increases the carbon concentration in the atmosphere, because most carbon emissions cannot be offset by photosynthesis or other natural processes. Consequently, the carbon dioxide concentration in the atmosphere rises, leading to the greenhouse effect. The result is global climate change.
Conventional plastics and polymers are produced almost entirely from fossil-based raw materials. Making greater use of renewable resources such as biomass in the production of polymers would help reduce the greenhouse effect.
Benefits of bio-based polymers
Bio-based polymers are produced using renewable resources (biomass) as a substitute for fossil-based feedstocks. Using bio-based raw materials in the production chain increases the proportion of biological substances in end-products and leverages their “green selling proposition“.
Bio-based does not always mean biodegradable
Many people, including stakeholders in the plastics industry, assume that bio-based means biodegradable. However, bio-based and biodegradable are not necessarily identical. Bio-based polymers may be biodegradable, but often they are not.
Bio-based refers to the origin of a material. In the case of bio-based polymers, it means that the polymers are based on renewable raw materials. By contrast, biodegradable is a functional attribute: it means that the material can be broken down by microorganisms, as it serves as a nutrient to them.
The 14C method can be used to check whether materials are bio-based and therefore eligible for certification as conforming to the ASTM D6866 standard developed by the American Society of Testing and Materials (ASTM). Certification is awarded by DIN CERTCO (in Germany) or Vinçotte (Belgium). End products may be awarded different certification logos, depending on the percentage of the carbon in the bio-based polymer that comes from “green” sources.
Biodegradability can be determined using standardized tests that meet the requirements of the European standards DIN EN 13432 and DIN EN 14995 and the US standard ASTM D6400. In the future, research will aim to identify whether polymers are biodegradable and find ways of making non-degradable polymers biodegradable.
Testing for biodegradability
The biodegradability of a polymer is determined by its chemical structure, not by the raw material from which it is produced. More than half of bio-based polymers are biodegradable in the right conditions, offering a solution for plastics that end up in the environment because they cannot be collected and recycled. Moreover, if such plastics are biodegradable, they do not cause pollution by microplastics.
Among the polymers that are not biodegradable on their own, some can be modified by additives to facilitate their biodegradation.

The key role of the 14C isotope
Scientists have developed a special process to identify the bio-based content of polymers. This method is based on measuring the concentration of the natural carbon isotope 14C in the polymer. A very low concentration of this isotope is present in the tissue of all living organisms. Although the 14C isotope is unstable, its concentration remains constant as a result of continuous interaction between the organism and the environment.
When an organism dies, it no longer absorbs 14C atoms from the atmosphere, so the concentration of the isotope in its tissue starts to drop. The half-life of the 14C isotope is 5,700 years. After 50,000 years, its concentration in a material is so low that it is no longer detectable. Therefore, fossil fuels (oil, gas, coal) no longer contain detectable amounts of the 14C isotope. Nor do products manufactured from them. By contrast, products manufactured using renewable raw materials have a measurable 14C concentration. In this way, it is possible to distinguish between fossil-based plastics and bio-based plastics and to determine the biomass concentration in a plastic such as polyethylene.
Standard test methods
Properties such as biodegradability and compostability are defined in various international standards. To ensure conformity with these standards, a product must be fully biodegradable by micro-organisms that occur naturally.
However, as long as their performance suits the intended use, even bio-based polymers that do not adhere to formal standards are attractive material choices: They replace fossil-based resources at least in part and increase the share of biological substances in the finished products.
Production of bio-based polymers
There are two different ways to produce bio-based polymers: direct production of polymers or production of bio-based monomers followed by (bio-)chemical polymerization.
The direct production route comprises biosynthesis of micro-organisms, algae, plants and a type of organism known as autotrophs. The most common plant-based biopolymer is cellulose, which is available in large quantities. Other common types are hemicellulose, starch, inulin and pectin. The principal polysaccharides are chitin and chitosan, which are produced by animals. These natural biopolymers are found in the exoskeleton of insects and crustaceans. They are also produced by some types of fungi. Micro-organisms are also important sources, especially of extracellular polysaccharides (EPS). The main sources of bio-based polymers also include bacteria, fungi and algae.
The second method of obtaining bio-based polymers is polymerization of bio-based monomers. The starting point here is 1,3-propanediol (PDO). This divalent alcohol is one of the oldest known products of anaerobic fermentation. It is produced from glycerine, a by-product of biodiesel, with the aid of bacteria. Although it had been assumed that widespread use of biodiesel could result in over-production of glycerine, it is still more expensive than glucose.
The success of PDO is regarded as an important milestone because it has led to research into other ways of coupling bio-based and conventional monomers, which could increase the use of bio-based materials in polymers. The development of PDO led to the synthesis of new polymers from bio-based monomers. Examples are the production of polylactide (PLA) from lactic acid, polybutylene succinate (PBS) from succinic acid, polyethylene from bio-based ethanol and hydrogenated styrene-farnesene-block-copolymers (HSFC) from styrene and beta-farnesene, a product developed by Kuraray.
Examples of bio-based polymers
The SEPTON™ BIO-series is polymerized from beta-farnesene – a bio-based monomer obtained from sugar cane – and styrene blocks (HSFC) with a biomass content of 50-80 percent. This versatile product has good grip performance, adhesive force and damping properties. Using SEPTON™ BIO-series can increase the biomass content of the end product.
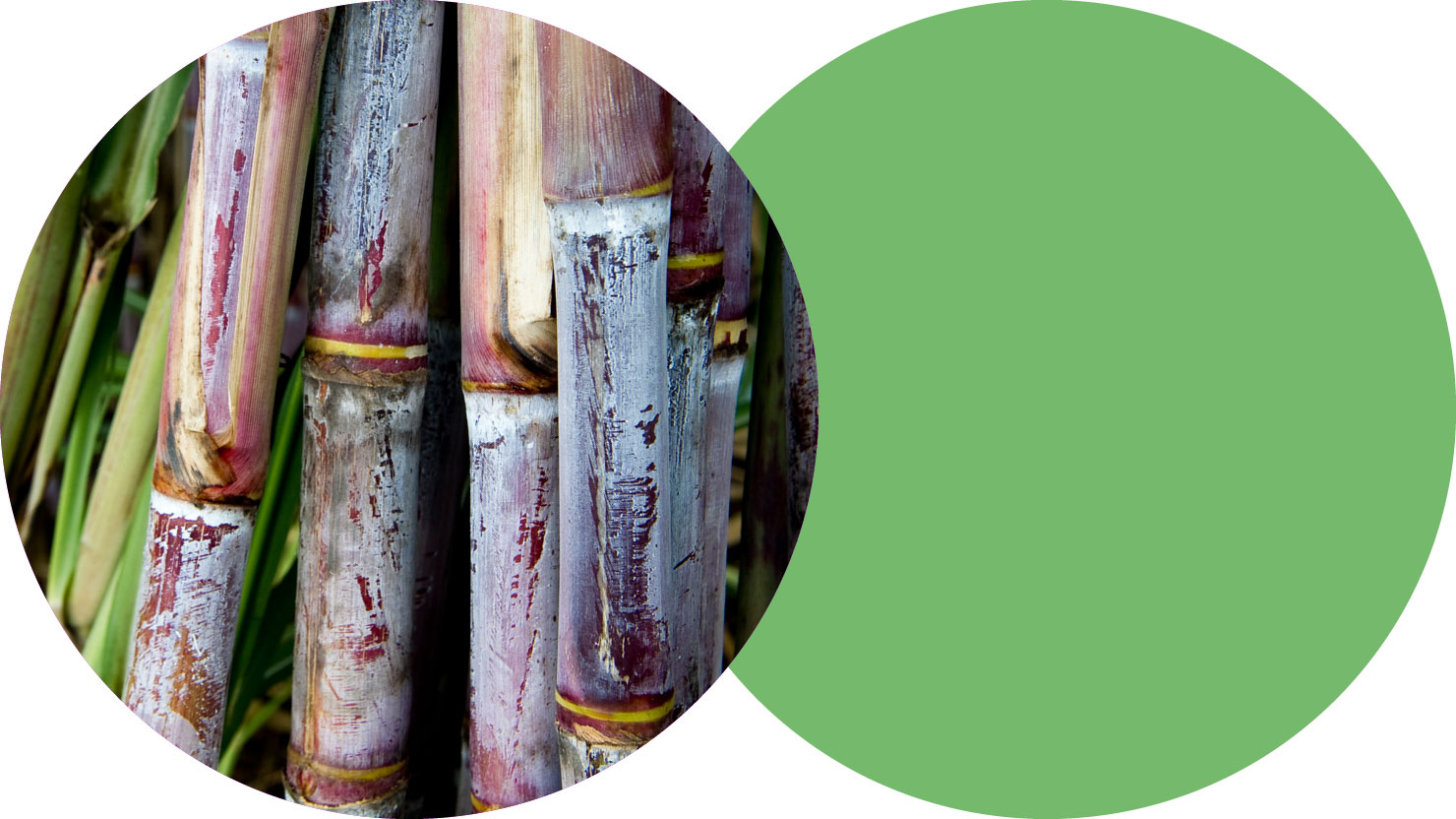
Liquid farnesene rubber from Kuraray is polymerized from beta-farnesene (homopolymer) or beta-farnesene and butadiene (farnesene-butadiene copolymer). It is mainly used in tires and other automotive components. In this way, it contributes to a more sustainable future.
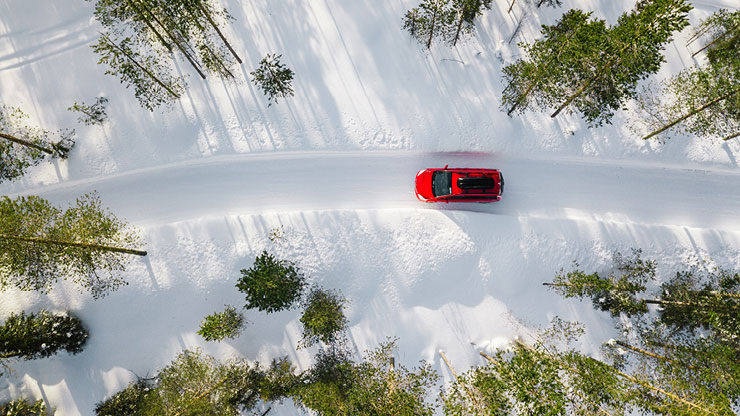
Present status of the bio-based polymer industry
Production of bio-based polymers has become far more professional and differentiated in recent years. Many producers and suppliers have started to produce bio-based alternatives for virtually all applications. Since there are already so many producers of bio-based polymers, it is difficult to monitor all planned and installed capacities and verify whether they are operational.
A realistic overview of the market is now possible thanks to detailed research by the nova-Institute in Germany, including interviews with international experts and people working with bio-based polymers. According to “Bio-based Building Blocks and Polymers – Global Capacities, Production and Trends 2019-2024”, a new market and trend report published by nova-Institute, bio-based polymers are still a small niche market. According to this report, total output of bio-based polymers was 3.8 million tonnes in 2019. That is just 1 percent of total production of fossil-based plastics, but about 3 percent higher than in 2018. However, the compound annual growth rate (CAGR) for production capacity and output of bio-based polymers is expected to be around 13.8% percent from 2020 to 2027.
Low political acceptance of bio-based polymers
At present, there is a lack of political support for bio-based polymers. Politicians have so far turned a blind eye to the two main benefits of bio-based polymers: First, the use of renewable carbon obtained from biomass instead of fossil-based carbon in the production process. Second, that many of them are biodegradable. Bio-based polymers are currently regarded as the lowest-level compromise between sustainability and economic efficiency.
In 2019, the European Union legislated to ban single-use plastics for which there are viable alternatives from summer 2021. No exception is made for products that are biodegradable and/or produced from bio-based materials. Almost all bio-based and biodegradable plastics have been given the same status as fossil-based plastics and banned. Only so-called “natural polymers”, in other words polymers produced by nature, are exempt from the ban.
In short, the market for bio-based polymers remains challenging at present due to low oil prices and a lack of political support.
Looking forward
The production of custom-tailored, fully bio-based biomaterials (polyhydroxyalkanoates [PHA], polysaccharides, etc.) is still not easy. This has led to research into partially bio-based versions of established petrochemical-based polymers (PET) and the development of new, partially bio-based polymers.
The development of genetic tools offers hope that further, fully bio-based plastics can be developed. Nevertheless, based on the present state of knowledge, these materials are still considered the lowest common denominator in the compromise between sustainability and cost-efficiency. In today’s rapidly changing, globalized market, neither price nor idealism can be seen as real driving forces for the future of bio-based polymers. Ultimately, the key to the success of these materials will be their performance and specific properties. In the mid-term, these aspects are likely to be the focus of research.
Contact