What are polymer adhesives?
Polymer adhesives are bonding agents made up of polymers. Polymers are large molecules composed of repeating subunits called “monomers”.
These adhesives can form strong bonds with various substrates such as metals, plastics, wood, glass, ceramics and composite materials.
Most polymer adhesives are synthetic, i.e. man-made materials. They can be formulated to have specific properties such as flexibility, thermal resistance, chemical resistance, or electrical conductivity to meet the requirements of their intended application.
How do polymer adhesives work?
Polymer adhesives make use of the two forces that are at play in any bonding process: Adhesion and cohesion.
Adhesion and cohesion
Adhesion is the force that sticks the molecules of two different substances together. For example, when a water droplet sticks to the surface of a glass, that is caused by the adhesive forces between the water molecules and the glass molecules.
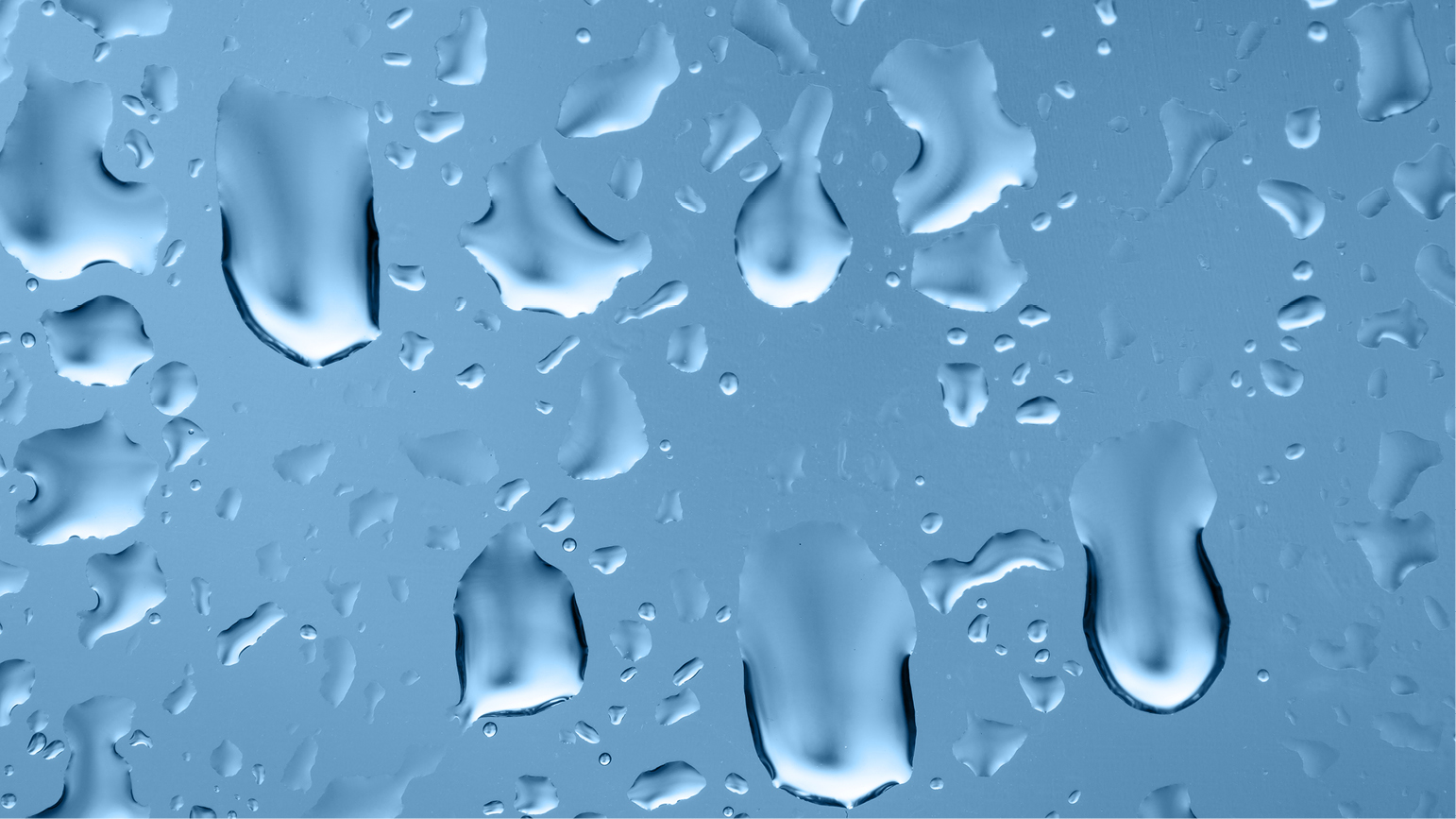
Cohesion is the force that keeps the same type of molecules together. For example, when you fill a glass of water all the way to the top and carefully add a few more drops, you can observe the water forming a dome-like structure above the rim of the glass. This phenomenon is called surface tension and caused by the cohesive forces of the hydrogen bonds between the water molecules. Due to these cohesive forces, light objects with a large surface area can stay afloat on the surface of the water such as water striders or this paperclip. Cohesion also explains why rain takes the shape of droplets rather than a fine mist.
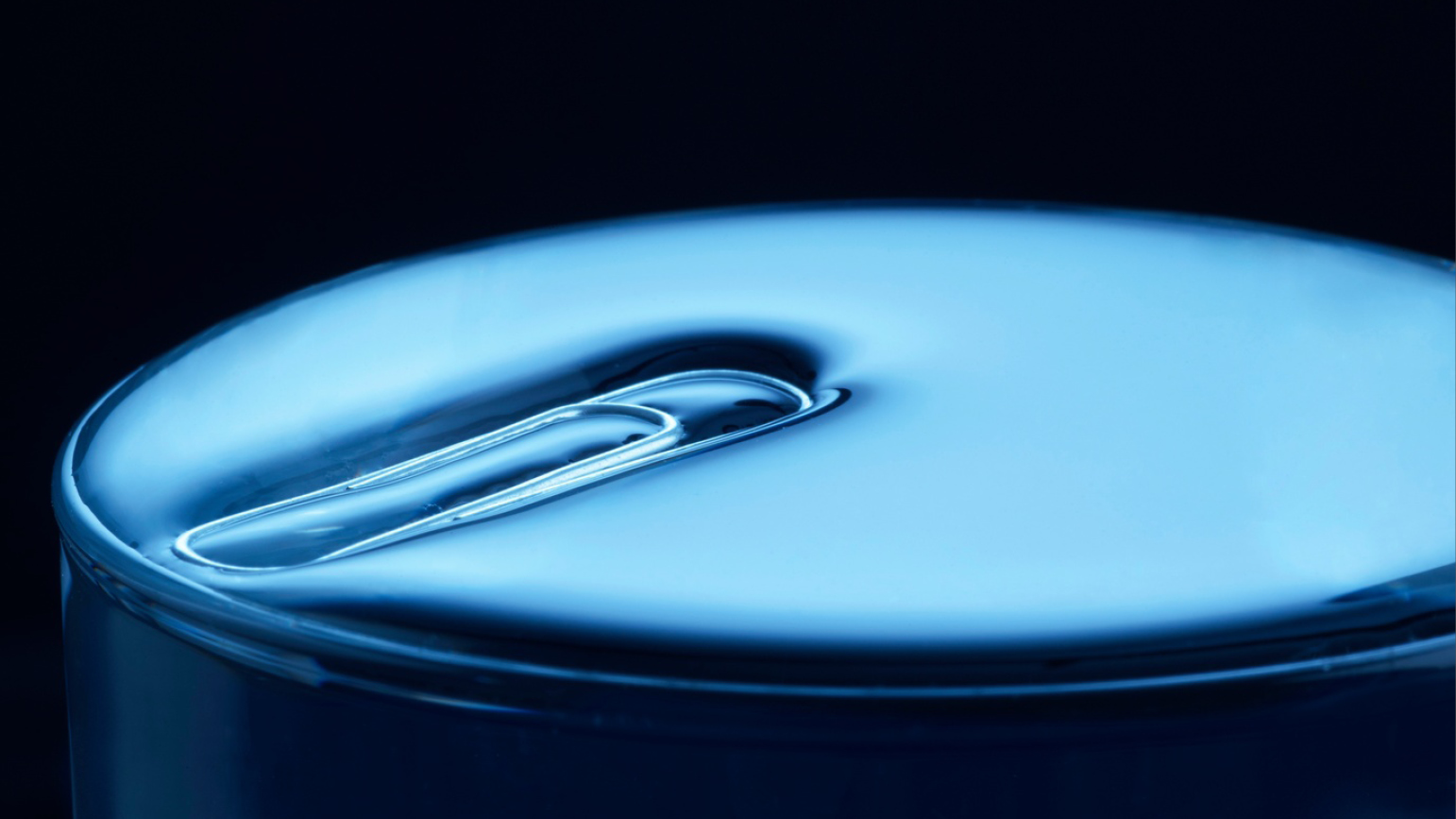
Polymer adhesives need both adhesion and cohesion to work: If the adhesive forces are too weak the glue won’t stick to the substrate in place (adhesive failure). If the cohesive forces are too weak the glue won’t hold itself (cohesive failure).
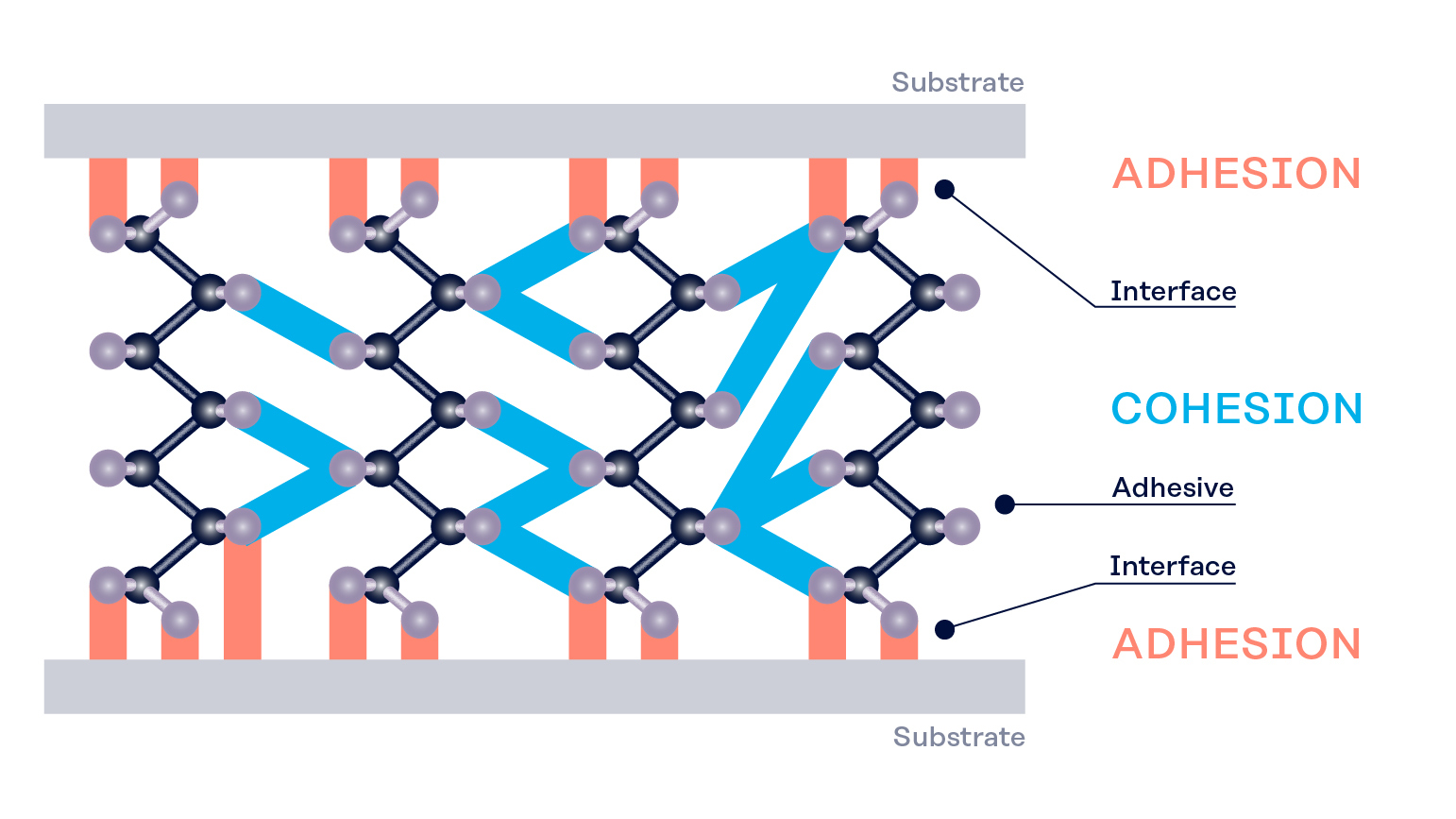
Bonds
There are three types of bonds: Electrostatic bonds, mechanical bonds and chemical bonds.
Electrostatic bonds
Electrostatic bonds rely on “adsorption” forces between ions, i.e. charged molecules of the glue and inversely charged molecules of the substrate that attract each other like magnets. These forces are also called “van der Waals” forces after the researcher who discovered them.
Electrostatic bonds are relatively weak. The adhesion will only work if the glue is spread over the substrate with good surface wetting and the surfaces are very close to each other.
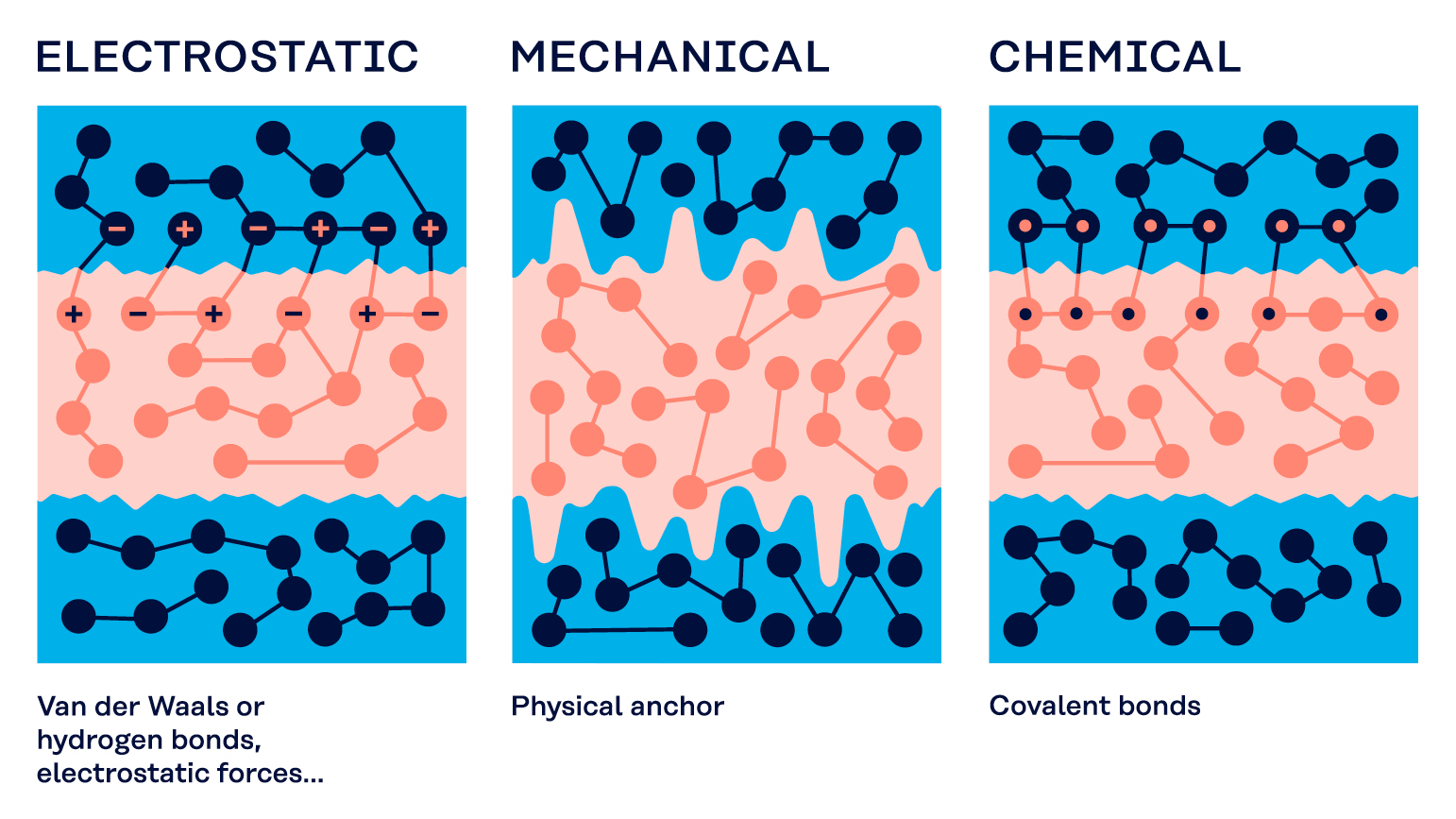
Mechanical bonds
Mechanical bonds rely on the adhesive entering holes in the surface of the substrate to flow in or protrusions to cling onto. Such bonds are more effective if the substrate has a particularly textured or porous surface.
Chemical bonds
Chemical bonds rely on a chemical reaction between the molecules of the adhesive and the molecules of the substrate. This requires the adhesive and the substrate to be chemically compatible with each other, or else no reaction will occur.
If the substances are compatible, they will form a very strong chemical bond compared to the much weaker electrostatic bonds.
In some cases, otherwise incompatible chemicals can still chemically bond indirectly through the use of a coupling agent.
Good to know
Coupling agents have a similar role as compatibilizers in the sense that both improve the interactions between two different substances. However, coupling agents improve the bond ability while compatibilizers improve the miscibility.
Thermoplastic adhesives vs. thermoset adhesives
There are many ways to categorize adhesives. An important distinction to be made is between thermoplastic adhesives and thermoset adhesives based on their molecular structure.
Thermoplastic adhesives
Thermoplastic adhesives provide strong adhesion at normal temperatures and can be melted and reworked without degradation.
Examples include:
- PVA / PVAc (polyvinyl acetate, also known as wood glue)
- EVA (ethylene-vinyl acetate copolymer)
- PE (polyethylene)
- PP (polypropylene)
- PA (polyamides)
- Polyesters
- Acrylics
- Nitrocellulose (cellulose nitrate)
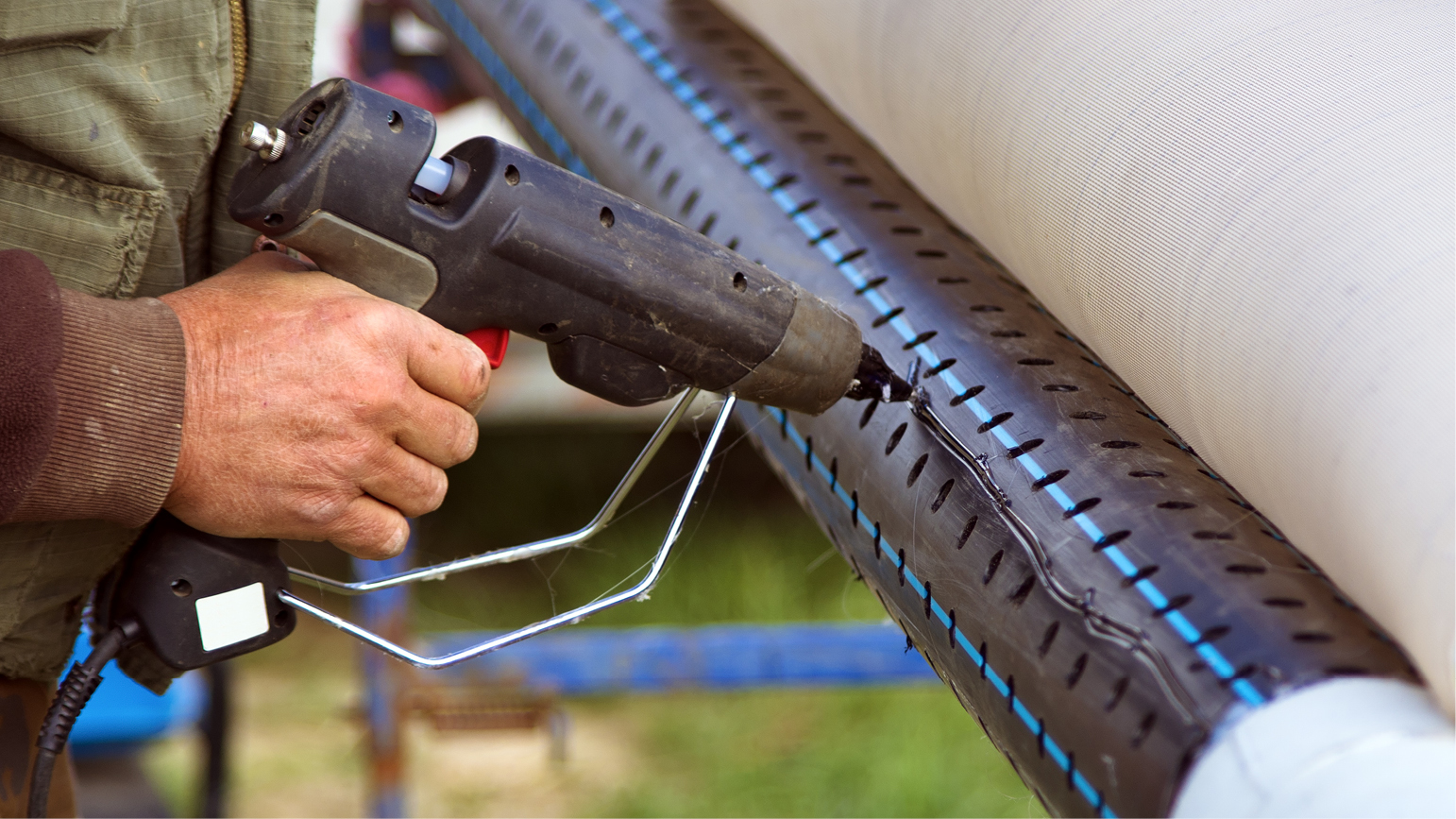
Thermosetting adhesives
Thermosetting adhesives form strong, permanent crosslinks upon curing. This leads to the creation of permanent, heat-resistant, and insoluble bonds that cannot be modified without degradation.
Examples include:
- Phenolics (phenol-formaldehyde resins)
- Urea formaldehyde (urea formaldehyde resin)
- Epoxies (epoxy resins, also known as polyepoxides)
- Unsaturated polyesters
- Polyurethanes
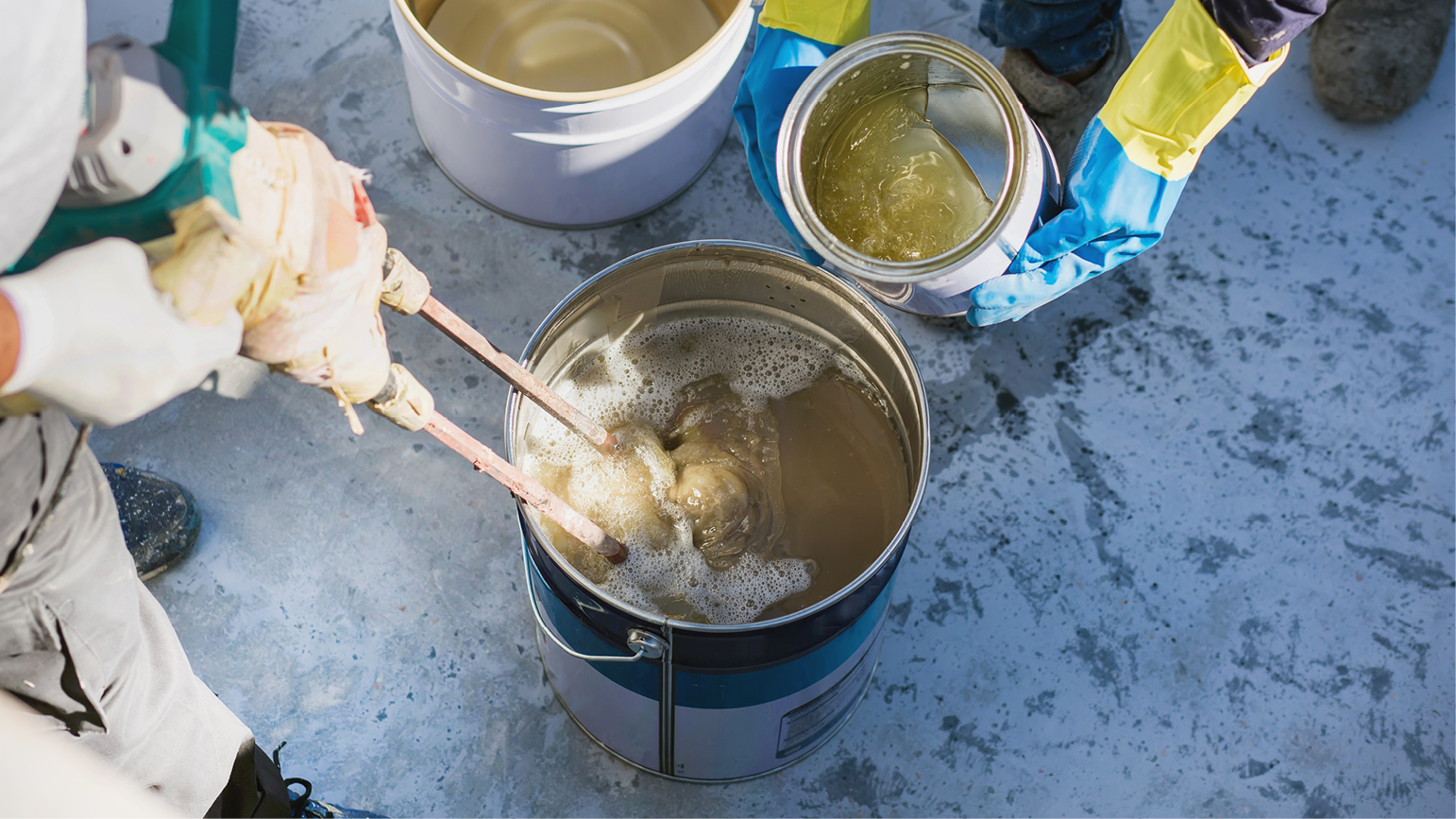
Major types of polymer adhesives
Polymer adhesives can also be classified based on their intended applications. The major types of adhesives are:
- Structural adhesives
- Engineering adhesives
- Hot-melt adhesives
- Pressure-sensitive adhesives
- UV-cured adhesives
Structural adhesives
Structural adhesives are designed to form strong bonds with various materials such as metals, composites, plastics, fiberglass, wood and stone.
They are used in applications that require high load-bearing capacity, long-term durability, as well as heat and solvent resistance. Among other things, structural adhesives can substitute or complement other joining methods involving nails, screws, rivets, bolts, or welding.
The main types of structural adhesives are:
- Epoxy adhesives, one or two-component adhesives that consist of an epoxy resin and a hardening agent. They are known for their high strength and excellent temperature and chemical resistance which makes them a popular choice for mobility, industrial and construction applications. However, they also exhibit good electrical insulation properties which makes them suitable for electronic components.
- Polyurethane adhesives display excellent flexibility, impact resistance and vibration dampening characteristics. They are commonly used in the mobility sector like automotive, marine and aerospace applications.
- Acrylic adhesives offer fast curing properties, good bonding strength, toughness and durability as well as excellent temperature and chemical resistance. They are often used in oily environments where other adhesives fail due to a lack of oil resistance. Example sectors include mobility, industrial and construction, electronics and packaging.
In summary, structural adhesives come in various types and are an attractive choice for various industries including mobility, electronics and industrial and construction.
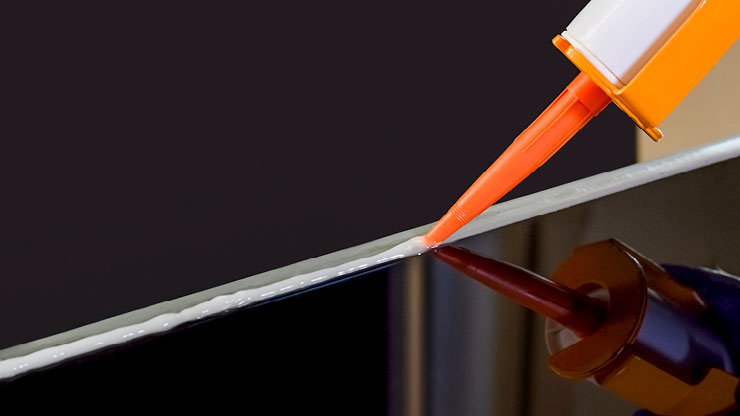
Engineering adhesives
There is no formal definition for engineering adhesives, but you can think of them as high-performance adhesives with less strict strength requirements compared to structural adhesives. They are developed to suit various needs in a broad range of adhesive applications for industrial products.
Similar to structural adhesives, engineering adhesives come in 3 main types:
- Anaerobic adhesives (also known as surface-activated acrylics) cure in the absence of air and the presence of metal ions. This makes them well-suited to secure and seal threaded metal components such as bolts, screws and nuts. For this reason, they are also called “threadlockers”. They are useful when sealing, vibration resistance, chemical resistance, and custom torque values (controlled friction) are needed.
- Cyanoacrylate adhesives are also known as superglues or instant adhesives. They have a very short curing time ranging from mere seconds up to a few minutes. Their other benefits include strong bonding strength, good adhesion to various surface materials, good temperature and chemical resistance and excellent transparency. They are ideal for bonding small parts and surfaces in various industries such as electronics, woodworking, medical (certifications required) and crafts, but they are also commonly used by regular household consumers.
- Silicone adhesives feature excellent heat, chemical and weathering resistance. They are versatile, flexible, and capable of forming reliable seals. Their applications include mobility, electronics, industrial and construction, medical (certifications required) and household applications.
Engineering adhesives have unique curing mechanisms, functions and characteristics which explains their important role in many industries.
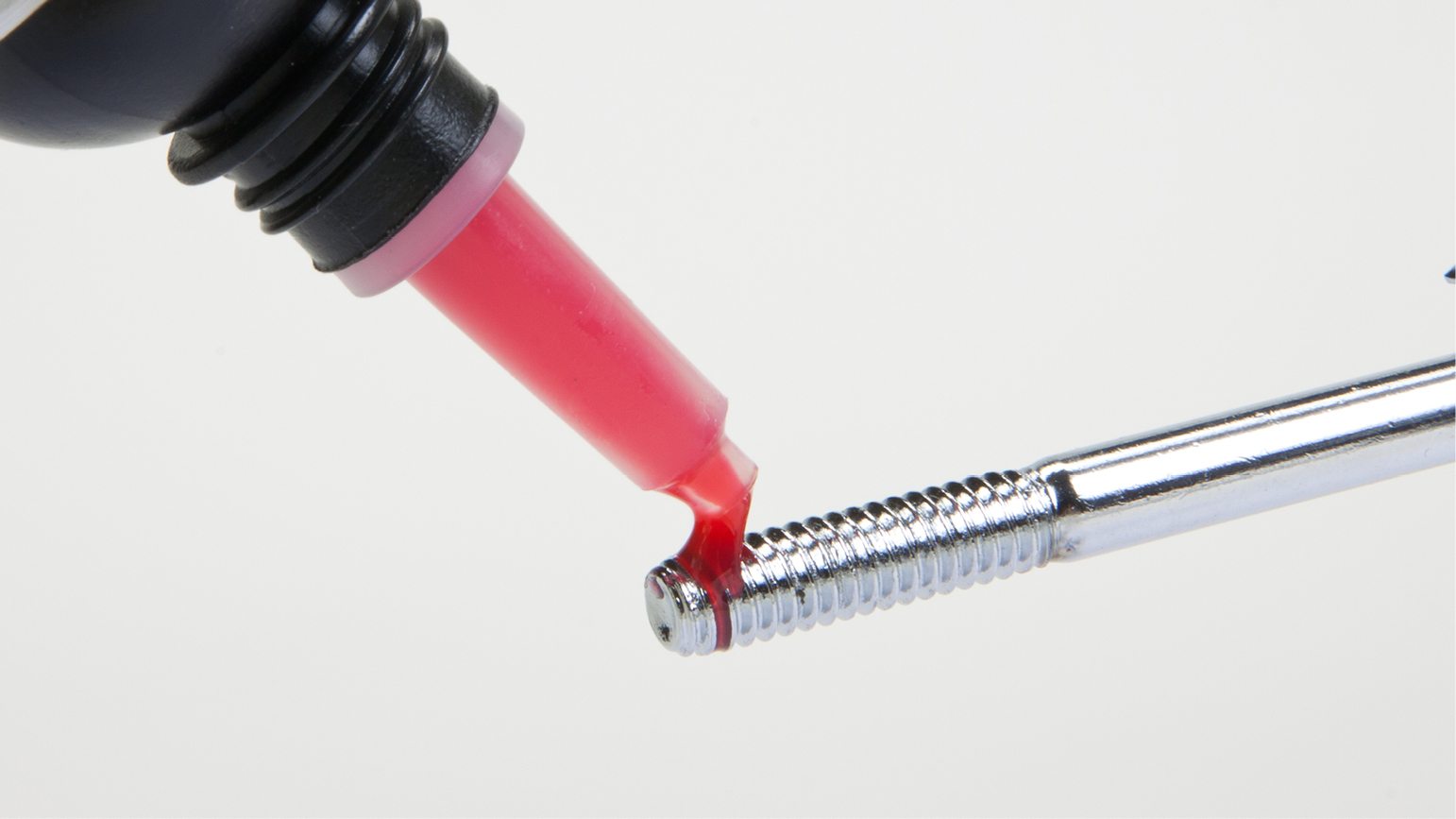
Hot-melt adhesives
Hot-melt adhesives are thermoplastic adhesives: They melt under the effect of heat without degrading and are applied in a molten state as hot liquids onto the surface to be bonded. Upon cooling, they solidify and form a strong bond.
Common examples of polymers used in hot-melt adhesives include:
- EVA (ethylene-vinyl acetate copolymer)
- Polyolefin: Atactic polypropylene (APP), amorphous poly alpha olefin (APAO), ethylene-ethyl acrylate copolymer (EEA), etc.
- PA (polyamides)
- Polyesters
- Polyurethanes
- Styrenic block copolymers
- Acrylic block copolymers
- Butyl rubber
- EPR (ethylene-propylene rubber)
- SBR (styrene-butadiene rubber)
These polymers can be formulated with additives to modify their adhesive properties or other performance characteristics. Examples of such additives include tackifiers, waxes, plasticizers, fillers and stabilizers such as antioxidants.
Hot-melt adhesives enable rapid bonding on a wide range of materials. They are easy to apply precisely with an applicator system or glue gun. As solvent-free adhesives, they are safer and more environmentally friendly than solvent-based adhesives as they do not contain any potentially dangerous VOCs (volatile organic compounds). Once they have cooled and solidified, they generally offer good temperature resistance as long as the environmental temperature stays below their melting point.
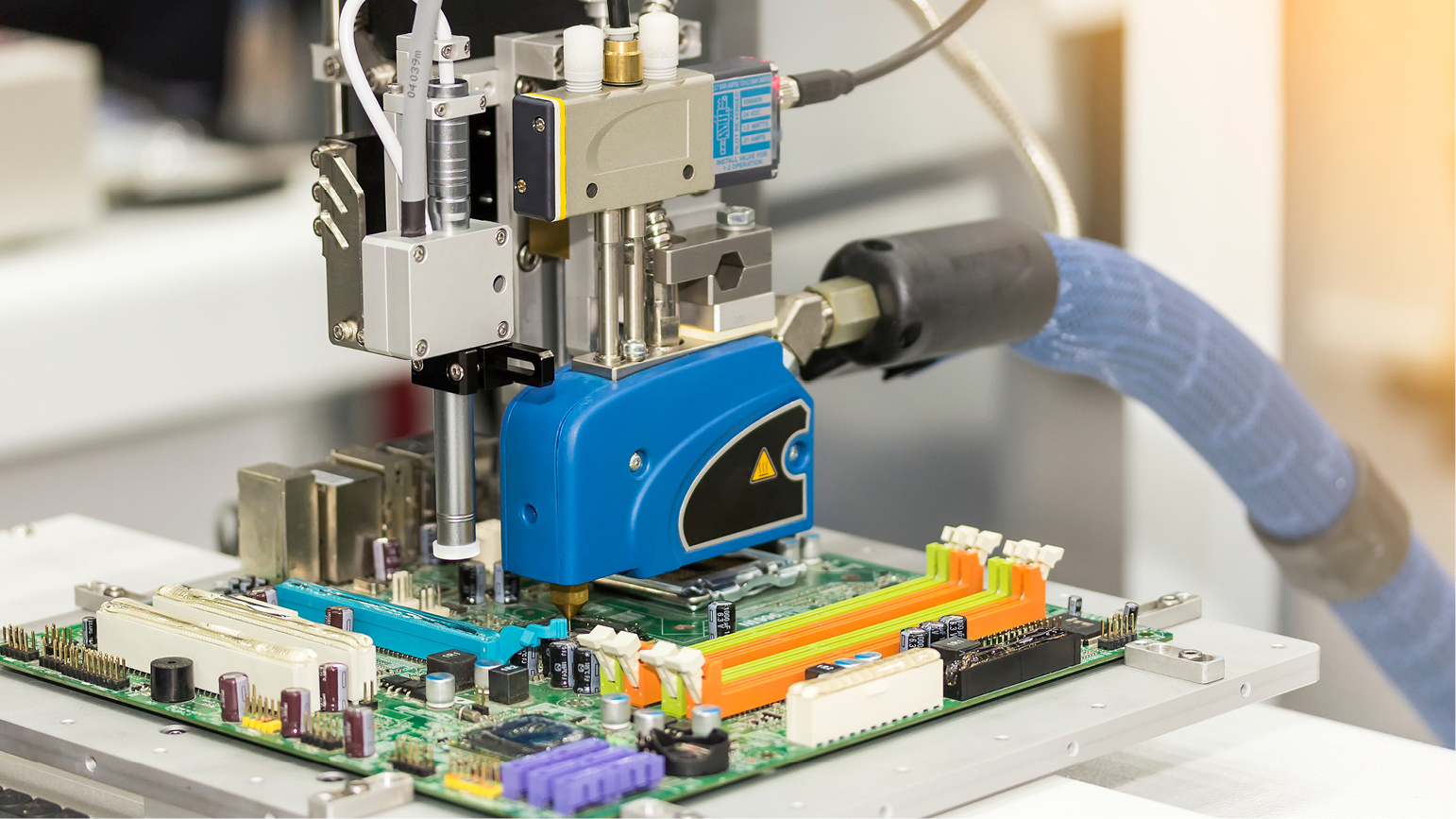
Pressure-sensitive adhesives (PSAs)
Pressure-sensitive adhesives (PSAs) activate when pressure is applied. Then, they start forming a bond with the substrate. In general, the strength of the bond depends on the amount of pressure applied.
Most PSAs work at common room temperature ranges, but fail at high or low temperatures. They activate when pressure is applied (they don’t require curing via heat, solvents or water – although some exceptions apply).
Tapes, labels, and stickers are common uses for PSAs. PSAs are also used with optical films, surface protective films, personal care and medical (certifications required) applications. To achieve the desired properties, chemical additives and modifiers can be used in their manufacture or application.
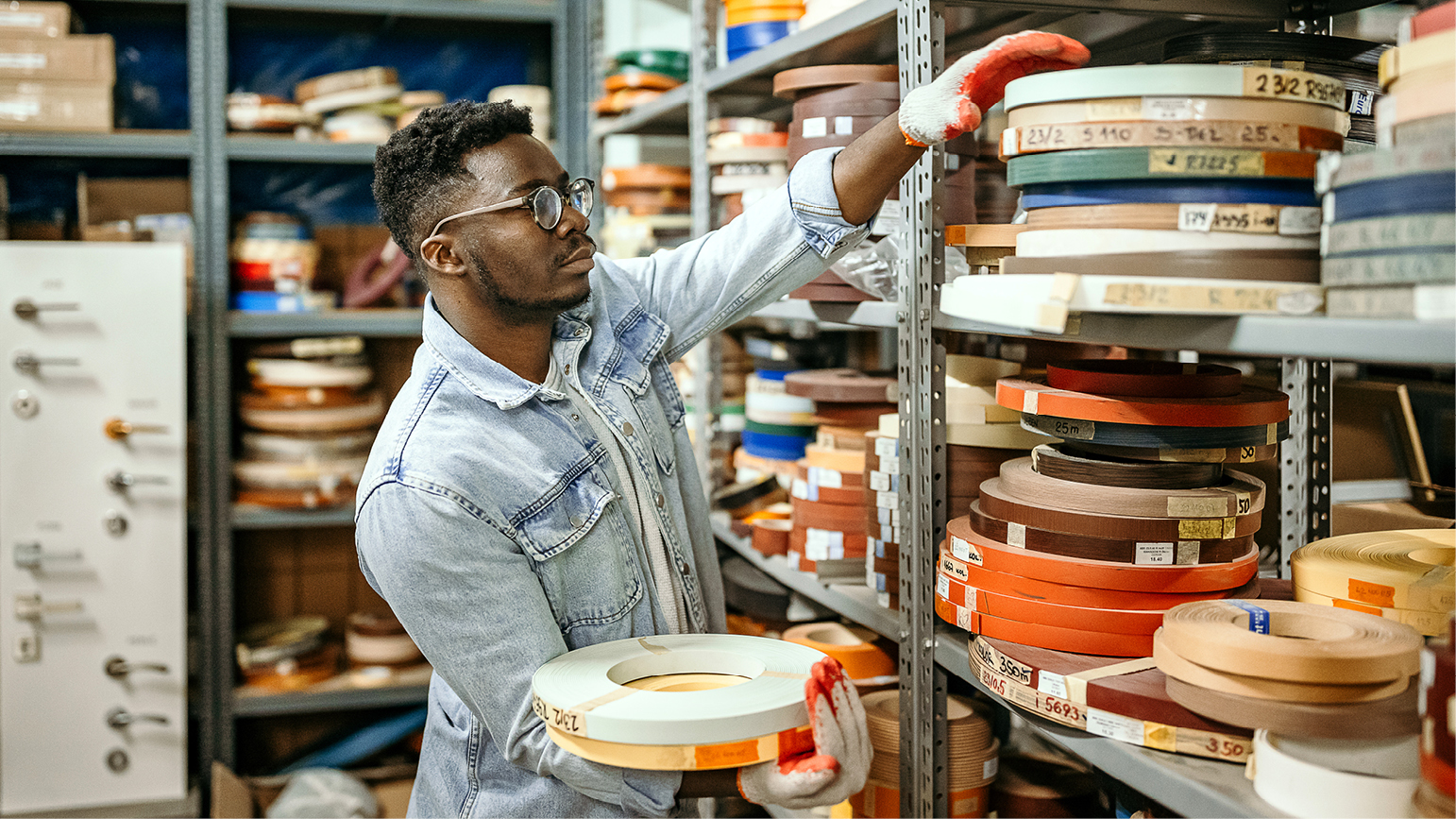
UV-cured adhesives
Ultraviolet-cured adhesives harden when they are exposed to ultraviolet (UV) light. Their curing relies on a chemical reaction called photopolymerization which uses UV light as the source of its activation energy. The energy is absorbed by photo initiators which turn the liquid polymer adhesive into a solid or highly crosslinked state.
UV-cured adhesives feature fast-cure times of mere seconds up to a few minutes. They can form strong bonds on various surfaces such as glass, plastics, metals and ceramics, and offer good chemical, heat and moisture resistance.
Applications include electronics, medical (certifications required), mobility, as well as sporting goods and footwear. Some UV-cured adhesives are applied directly in liquid form while others are part of the adhesive surface of tapes and labels.
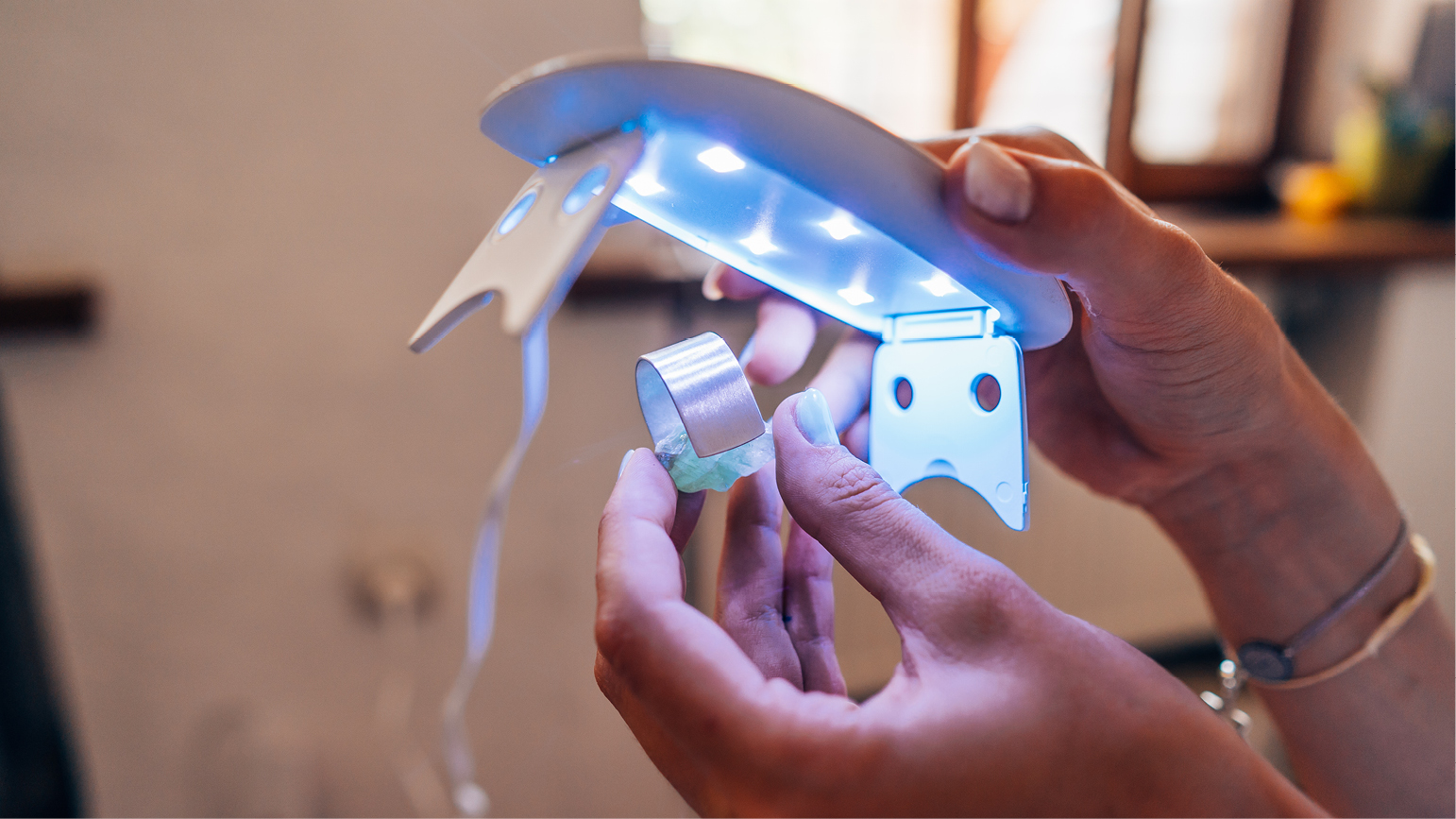
How to choose the best polymer adhesive for your application?
These are the steps you should follow to choose the best polymer adhesive for your application:
- Understand the bonding substrates
- Determine open time (how much time you have to complete the setup) and cure time (how much time you have until the bonded components must be ready for use) during application
- Assess application and curing method
- Define performance characteristics (e.g. strength, flexibility, hardness, viscosity, vibration dampening, color)
- Understand the environmental conditions (temperature, moisture, chemical exposure, UV light)
- Perform testing
- Consider health and environment
- Consider cost and availability
During these steps, you should consult technical data and get advice from experts to make sure you are choosing the most suitable polymer adhesive.
In many cases, you can add chemical additives and modifiers to customize an adhesive polymer to fit the precise needs of your applications. Our experts are happy to consult with you on this.
Kuraray’s polymer adhesive materials
Kuraray offers a wide range of specialty polymers for polymer adhesive applications. Some of them can be used as the base polymer of the adhesive, while others are additives to improve the performance characteristics of your adhesive.
SEPTON™ and HYBRAR™
SEPTON™ and HYBRAR™ are versatile high-performance TPEs. Its styrenic block copolymer (SBC) molecular structure combines the benefits of a rubber-like elasticity and thermoplastic processability.
SEPTON™ offers excellent performance characteristics over a wide temperature range as well as good resistance to chemicals, weathering, UV light and electrical insulation.
HYBRAR™ is available as durable hydrogenated grades (HYBRAR™ 7000-series) and non-hydrogenated grades (HYBRAR™ 5000-series). HYBRAR™ offers high damping performance. HYBRAR™ 7000-series has excellent compatibility with polypropylene.
SEPTON™ and HYBRAR™ can be used a base polymer for hot-melt adhesives or as an additive for polyolefin-based adhesives to customize their softness, stretchability, impact resistance, adhesion and cohesion.
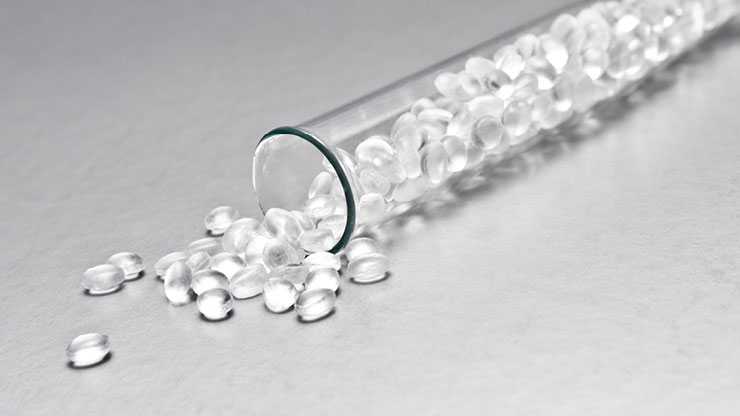
KURARAY LIQUID RUBBER
KURARAY LIQUID RUBBER works like a “reactive plasticizer” to improve flowability and reduce the viscosity of compounds. The product series are available as liquid butadiene rubbers (L-BR), liquid isoprene rubbers (L-IR) and liquid styrene-butadiene rubbers (L-SBR).
If KURARAY LIQUID RUBBER is applied as an additive to polymer adhesives, it will function as a modifier to increase adhesion strength and tackiness. The functional grade can improve the adhesion to substrates like metals, glass, and fibers. The UV-curable grades can be used as components of UV-cured adhesives.
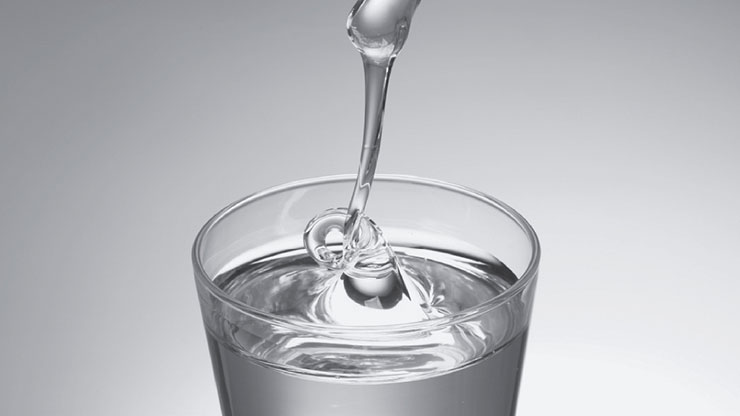
Liquid farnesene rubber
Liquid farnesene rubber is a liquid rubber based on beta-farnesene, a bio-based monomer gained from renewable sugar cane. Using liquid farnesene rubber can help manufacturers increase the bio-based material content in their products.
Due to its high reactiveness caused by its branched molecular structure, low viscosity and high molecular weight, liquid farnesene rubber can modify adhesive properties such as adhesion and cohesion.
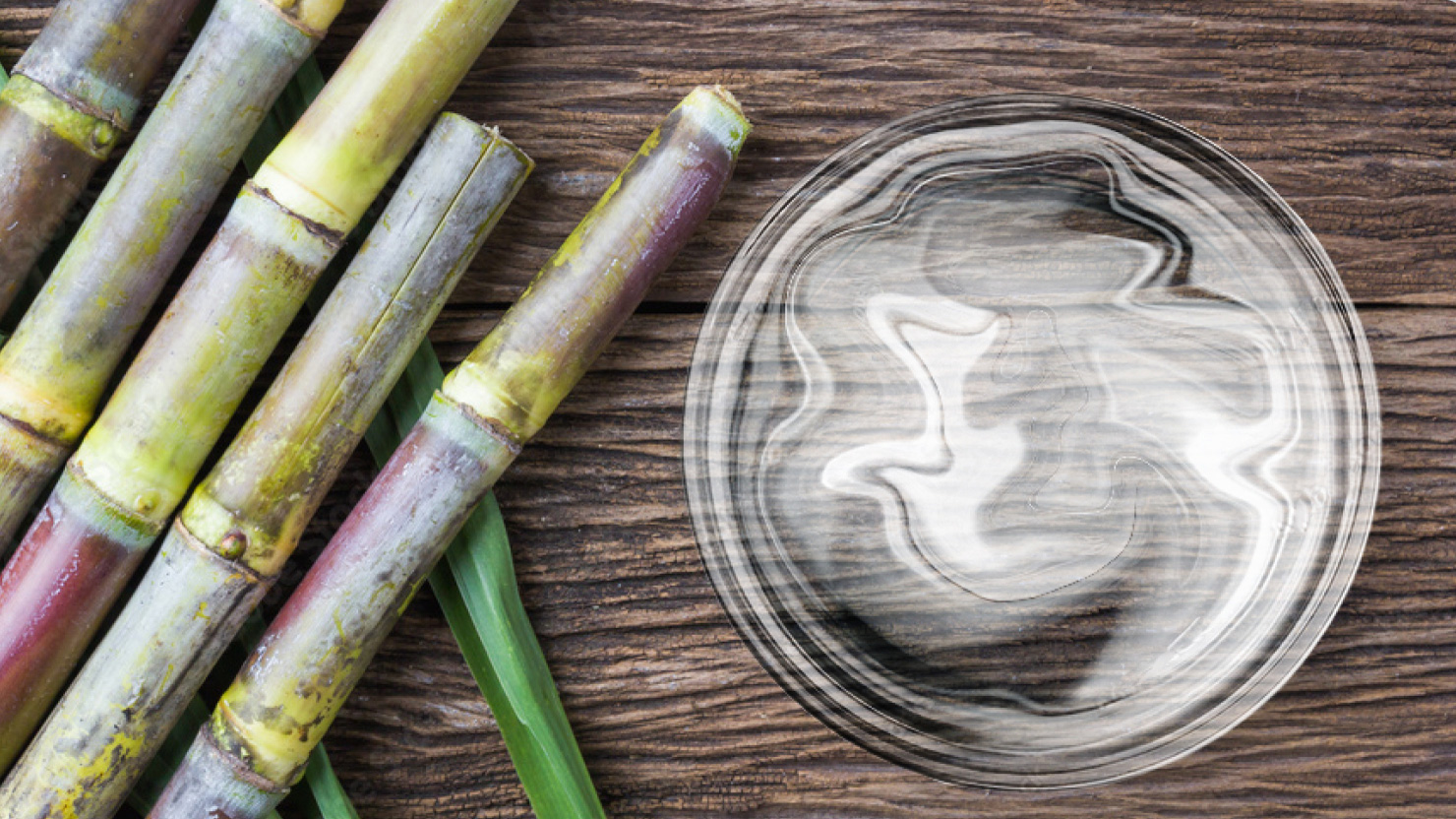
ISOBAM™
ISOBAM™ is an alkali water-soluble copolymer of isobutylene and maleic anhydride. ISOBAM™ can be used as an additive in emulsion adhesives of polyvinyl acetate for woodworking. ISOBAM™ can improve initial tack and heat resistance.
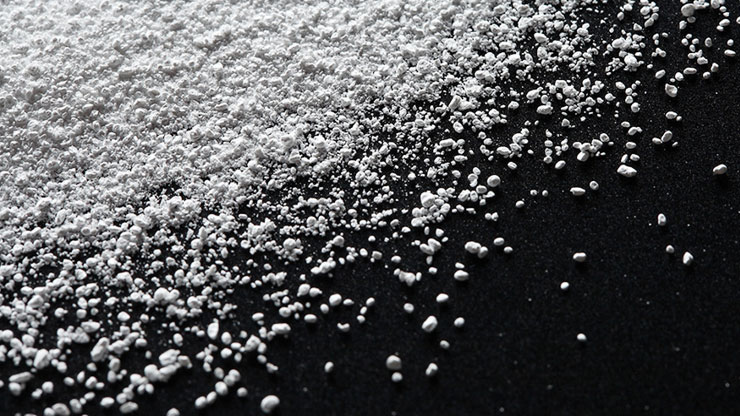
Contact