What are elastomers?
Did you know that elastomers are true hidden champions of our everyday lives? We would like to introduce them to you:
Elastomers are polymers with viscoelasticity (meaning both viscosity and elasticity), generally amorphous polymers with cross-linked network structure. They deform with low stress, and when the stress is removed, return to their original shape.
The term ‘elastomer’ is a portmanteau of ‘elastic’ and ‘polymer’, and it is often used synonymously with rubber. However, the latter term is more commonly applied to vulcanized elastomers.
The loosely cross-linked polymers generally have a low modulus of elasticity and high extensibility compared to other materials. The polymer chains are held together in the elastomers by relatively weak intermolecular bonds that allow the polymers to stretch under stress. Elastomers owe their elasticity to the ability of the long chain molecules to realign themselves to distribute an applied stress.
Under normal conditions, the long molecules of elastomeric material are irregularly coiled. When a force is applied, they align themselves in the direction they are pulled, returning to their normal arrangement when the force or tension is released. Because of this extreme flexibility, individual elastomers can expand reversibly by up several hundred percent.
Properties
What is important about them to professional buyers, chemists and material scientists? From the wide range of commercially available elastomers, they select the one whose properties best match the requirements of their application. Depending on the application, their attention is focused on the following:
- Mechanical properties
- Thermal properties
- Chemical resistance
- Economical properties
- Socio-ecological properties
Mechanical properties
The mechanical properties of an elastomer are the physical properties it exhibits when forces act on it. These include, for example, parameters such as hardness, elongation at break, abrasion resistance, and tear resistance.
Hardness
The hardness of the elastomer is an important selection criterion. A key figure in this context is the Shore hardness. To determine it, the resistance of the elastomer to a deformation force is measured over a defined period of time. While harder elastomers have a high resistance to deformation, the opposite is true for soft elastomers.
Elongation at break
Elongation at break is a measure of how far an elastomer can be stretched before it breaks. The elongation at break is usually given as a percentage of the original length.
Abrasion resistance and tear resistance
Abrasion resistance is an important parameter for elastomers, especially for dynamic sealing and tire applications. Good tear resistance of elastomers is important where they may be subjected to cuts, tears and nicks. Elastomers with good abrasion resistance usually also have good tear strength. Elastomers with poor abrasion resistance, on the other hand, usually also have poor tear resistance.
Most sealants and adhesives, for example, have low abrasion and tear resistance requirements (exceptions apply). Applications such as tires, shoe soles or industrial conveyor belts, on the other hand, require high abrasion resistance and tear resistance.
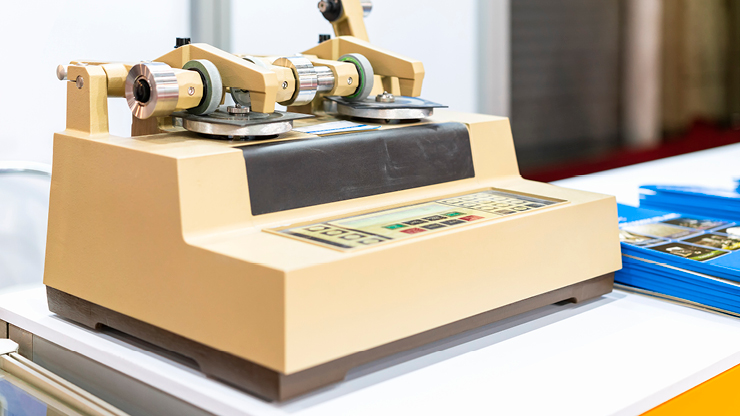
Thermal properties / heat resistance
The application temperature deserves special attention. This is because it can have a direct effect on the performance of elastomers. The maximum operating temperature can vary greatly from elastomer to elastomer. Elastomers become harder and lose flexibility as temperatures drop or fall below its glass transition temperature. This can go so far that they lose their rubber-like properties or even break. These changes are mostly reversible, as they are physically induced. More critical are high temperatures, because here the elastomers may undergo irreversible chemical changes.
Consumer goods (e.g. toys, personal care) or sporting goods (e.g. handles, swimming equipment) usually place low demands on the temperature resistance of elastomers. The situation is quite different for mobility applications such as tires or engine compartments, in the aerospace industry or for heat-resistant adhesives. Here, high requirements must be met.
Chemical resistance
Chemical resistance can also be important, because some applications of elastomers involve contact with other chemicals. The chemical resistance refers to the property of a material that is exhibited during or after a chemical reaction. If a material undergoes a chemical reaction, it can sometimes exhibit different properties as a result of a changed internal structure.
Examples of chemical properties of elastomers include liquid compatibility as well as heat resistance and flammability. While toys, sporting goods and stationeries, for example, have low requirements for the chemical resistance of elastomers, the opposite is true for tires, automotive parts and hydraulic parts.

Fluid compatibility
Elastomers have varying degrees of compatibility with fluids. In the event of poor compatibility, the properties of an elastomer part can rapidly deteriorate to the point of total failure. Temperature and pressure as well as the concentration of a chemical are common influencing factors here. In critical applications, it therefore makes sense to subject elastomers to a functional test.
In numerous applications, elastomer parts come into contact with hydrocarbon oils. Certain elastomer parts, such as seals, are classified according to their resistance to heat and oil. One example is the ASTM D2000 system, which classifies elastomers according to heat resistance (type) and oil resistance (class).
Economical properties
That should be clear: Cost is an important decision criterion when selecting a plastic. Elastomers can be an efficient and cost-effective alternative to other materials, and at the same time can improve the comfort and properties of the end product. Due to varying raw material and compounding costs, as well as varying processing costs, prices can fluctuate widely.
Socio-ecological properties
How important is the sustainability of an elastomer to you? For more and more trade buyers and users, this aspect is high up on the agenda. It is therefore worth considering elastomers from this point of view as well.
Natural rubber is obtained from natural rubber trees and has been used by people for thousands of years. Today, it is one of the most important materials that is not derived from petroleum.
Does this make natural rubber sustainable? You should keep in mind that tropical forests are being cleared for rubber plantations to meet the increasing demand. In addition, pesticides and herbicides are used to protect the rubber trees from pests and weeds.
What many also don’t know: Kneading natural rubber is energy intensive, and at the end of its life, it is difficult to recycle.
Synthetic rubber is a product of the petroleum industry. Numerous synthetic rubber compounds are in widespread use today. The negative environmental impacts of their production and use are detrimental to sustainability. These include the use of fossil raw materials, energy-intensive production, and emissions that are harmful to the climate and water. Moreover, like natural rubber, crosslinked polymers are difficult to recycle. On the positive side, however, they can be used in applications that reduce vibrations and noise that are harmful to health.
And what about TPEs? TPEs are made from a variety of synthetic materials. There are now also some that are bio-based materials. As a thermoplastic, TPE can also theoretically be recycled. However, since it is not a major type of plastic, the options are limited. Shredded, it can serve as a filler material for other products, or it can be melted down and new TPEs produced from it. Also positive is the lower environmental impact of the product manufacture using TPEs compared to natural rubber.
To put it in a nutshell: Natural rubber, synthetic rubber and TPEs all have their advantages and disadvantages when it comes to sustainability. The decision ultimately lies with the customer.
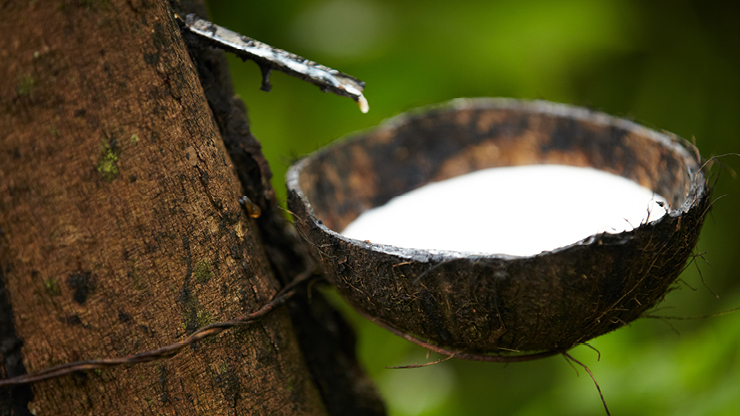
Types of elastomers
Elastomers can be divided into two groups: thermoset and thermoplastic elastomers. The two groups differ greatly in their properties. This relates in particular to the formability.
Thermoset elastomers
Here’s what you should know: Elastomers are not only highly deformable, but also essentially fully recoverable. Polymer chains with high flexibility and mobility and a cross-linked network structure ensure this elasticity. In contrast, thermoset elastomers cannot be remolded after curing. The reason for this is that thermosets have a network structure that is firmly crosslinked in three dimensions by thermally induced chemical bonds. While unsaturated elastomers are vulcanized with sulfur, saturated elastomers are vulcanized using other cross-linking agents, as they cannot be vulcanized with sulfur.
Unsaturated elastomers
A characteristic of unsaturated elastomers is that they contain carbon-carbon double bonds. They can be vulcanized with and without sulfur.
Natural rubber
Let’s take a look at natural rubber. Its basic material is the milky sap of the tropical rubber tree. Initially, experimental attempts were made to use it for the manufacture of bags, valves and other products. However, its low temperature resistance as well as its cracking and stickiness prevented this.
It was not until Charles Goodyear, who was researching ways to improve the material properties of natural rubber, that the breakthrough came. In the vulcanization process he developed, raw rubber is mixed with sulfur and heated. The elastic rubber obtained was initially used to make shoe soles, hoses, tires and other products. The boom in natural rubber came decades later with the emergence of the automotive industry in the early 20th century and the associated huge demand for car tires.
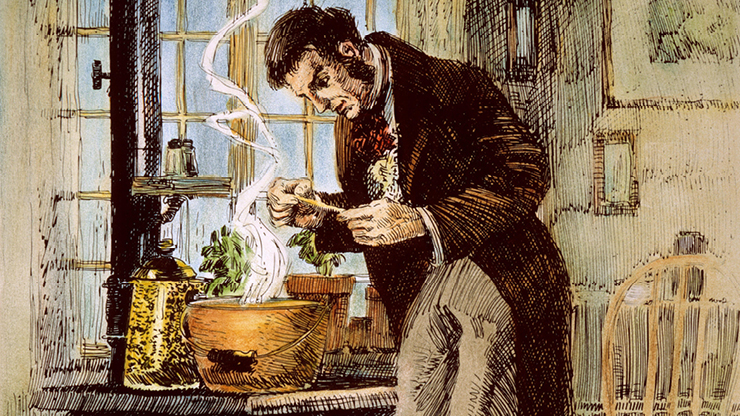
Gutta-percha
Are you familiar with gutta-percha? This elastomer is chemically similar to natural rubber, but has a different molecular structure (natural rubber: amorphous, gutta-percha: crystalline). This also results in other properties, such as higher stiffness of the material produced from it. The basis of the natural polymer is the milky liquid of the gutta-percha tree. This is evaporated and the resulting latex is then coagulated.
In the past, gutta-percha was used, among other things, for golf balls and to insulate submarine cables. Today, there are hardly any applications in which it is still used.
Synthetic polyisoprene
Synthetic polyisoprene rubber differs from natural rubber in its microstructure. While the latter consists almost entirely of cis-1,4 polymer, synthetic polyisoprene is a mixture of cis-1,4, trans-1,4 and 3,4-vinyl polymer. This also causes differences in the properties. For example, synthetic rubber generally has slightly lower tear resistance and tensile strength than natural rubber. Both have good resistance to rubber fatigue and, over a wide temperature range, an excellent compression set, elasticity as well as abrasion and creep resistance. However, they have poor resistance to gasoline, ozone and a variety of organic solvents. An important area of use for synthetic rubber is in technical applications, where its very good mechanical properties and favorable price-performance ratio are an advantage.
Polybutadiene
Would you have known that? Polybutadiene (PBD) accounts for a good quarter of global consumption of synthetic rubbers. This very elastic rubber features an extremely low glass transition temperature and good abrasion and tear resistance. Heat generation is low, making PBD ideal for tire applications. PDB has lower rolling resistance than SBR, but also lower friction on wet surfaces. Therefore, PBD is usually blended with SBR and natural rubber to improve performance of the tires.
Styrene-butadiene rubber
Styrene-butadiene rubber (SBR) is produced from styrene and butadiene. The mixture of the two monomers is polymerized either in solution (S-SBR) or as an emulsion (E-SBR), whereby the latter manufacturing process is still the most commonly used to date. The properties of the polymer depend on the ratio of the two monomers. For example, a high styrene content results in harder rubbers.
SBR is characterized by a relatively low price, good wear and adhesion properties, and good aging resistance (with the help of additives). About half of all car tires are produced from various types of SBR. Other applications include drive clutches, shoe soles, conveyor belts, adhesives and various other molded rubber parts.
However, you must not confuse SBR with the TPS, styrene-butadiene-styrene block copolymer. The latter is also obtained from the same monomers, but: In styrene-butadiene-styrene block copolymer, each monomer of styrene and butadiene form a block and these are combined with each other. In contrast, in SBR, the two monomers are combined randomly.
Other unsaturated elastomers
Other unsaturated elastomers of importance are chloroprene rubber, butyl rubber and nitrile rubber.
Saturated elastomers
What constitutes saturated elastomers? These are characterized by high stability to environmental factors such as heat, radiation, ozone and oxygen. A reaction to these factors only takes place under certain conditions and situations. Important types include polyacrylic and silicone rubber, ethylene vinyl acetate copolymer and EPM/EPDM rubber.
EPM / EPDM rubber
What you should know: The basis of EPM rubber are ethylene and propylene monomers without unsaturated carbon-carbon double bonds. The long-chain polymers each consist of one or more monomers that are crosslinked together end-to-end. While a copolymer consists of the two monomers ethylene and propylene, a third monomer is added in a terpolymer with diene.
The two ethylene-propylene rubbers EPM(EPR) and EPDM are an EP copolymer and an EP terpolymer, respectively. EPM and EPDM differ only very little in performance. Significant differences in performance exist only in extremely demanding applications, such as with concentrated acetic acid. Here, some EPDM compounds offer better performance than most EPMs.
To produce an elastic rubber material, essentially the polymer chains have to be bonded together by vulcanization. Due to the chemical properties of these chains, the curing process for EPM can only be peroxide-based. This is different with EPDM, where the additional diene monomer provides a vulcanization site that allows the polymer to be vulcanized on a peroxide or sulfur basis. Because of this increased flexibility, the sealing industry prefers EPDM over EPM for most EP-based rubber compounds. However, there are still industries, such as the automotive industry, where EPM continues to be widely used.
Polyacrylic rubber (ACM)
Polyacrylic rubbers, also known by the chemical name alkyl acrylate copolymer (ACM), are synthetic elastomers composed of ethyl acrylate or other acrylates and a small amount of a monomer that facilitates vulcanization. The manufacturing process is usually emulsion or suspension polymerization. The combination of a saturated backbone with polar side groups results in products that have excellent resistance to heat and oxidation. Their resistance to hydraulic oils is also excellent. Ozone and weathering resistance is also good.
ACM elastomers are used primarily in applications that require high heat and oil resistance. These include, in particular, transmission components such as hoses and seals as well as shaft seals. Due to their excellent elasticity, they are also widely used for damping vibrations, such as vibration-damping bearings.
Silicone rubber (SI, Q, VMQ)
Let’s take a closer look at silicone rubber. This high-performance elastomer contains silicon, carbon, hydrogen and oxygen. The elastomer is generally non-reactive. Because of the Si-O bond in its structure, silicone rubber has improved properties compared to natural rubber in terms of heat, weathering, ozone and wear resistance, chemical stability and electrical insulation. Its good stability and resistance to extreme temperatures should be emphasized.
Silicone rubber is increasingly used in industries where the end product must retain its mechanical strength and original shape even when exposed to intense heat or sub-zero temperatures. Because of their properties and the ease with which they can be manufactured and shaped, silicone rubbers are used in a wide variety of applications and products:
- Automotive
- Consumer Products
- Sportswear
- Electrical & Electronics
- Sealants
- Medical and Healthcare
- Industrial
- Aerospace
- Semiconductor industry
Other saturated elastomers
Other important saturated elastomers are listed below:
- Epichlorohydrin rubber (ECO)
- Fluorosilicone rubber (FVMQ)
- Fluoroelastomers (FKM, and FEPM)
- Perfluoroelastomers (FFKM)
- Chlorosulfonated polyethylene (CSM)
Thermoplastic elastomers
You want high flexibility in manufacturing and design? Then thermoplastic elastomers (TPEs) could be the material of choice for you, because they are the most versatile plastics of all. TPEs process well with thermoplastic processes such as extrusion and injection molding. Time-intensive processing methods for rubber, such as vulcanization, are not required.
Due to their molecular structure with hard and soft segments, TPEs have a high elasticity. They can be physical blends or alloys of crystalline and amorphous polymers. Another possibility is block copolymers, which have chemical mixtures of blocks of crystalline (or if not: with a strong cohesion) and amorphous domains in the polymer chain.
In the case of TPEs and blends, the hard blocks are responsible for the plastic properties of the end product. Among other things, they ensure easy processability and temperature resistance, as well as material properties such as tear and tensile strength, chemical resistance or good adhesion. The soft blocks are responsible for the elastomeric or elastic properties, in particular hardness and flexibility, as well as, the extent of permanent deformation.
Important applications of TPEs are:
- Adhesives, coatings & sealants
- Compounding
- Consumer goods
- Electronics
- Industrial & construction
- Medical
- Mobility
- Oil modification
- Sporting goods & footwear
- 3D printing
You want to learn more about TPE? We will be happy to inform you!
Processing of elastomers
Now you probably want to know how elastomers are processed? The most important processing methods are vulcanization and injection molding. In injection molding, the molten elastomer is injected into a mold. The end product is then an exact copy of the mold. Applications include the co- and insert-injection processes. In case of vulcanization, natural and synthetic rubbers are converted into elastomers. The produced rubber has permanently elastic properties compared with the starting product. In addition to classic sulfur vulcanization, the crosslinking of rubbers is often carried out with the aid of other processes, such as electron beams or free radicals.
Other processing methods include:
- Extrusion
- Extrusion blow molding
- 3D printing
- Mold calendaring etc.
Applications
Elastomer examples
A wide range of elastomers is available. Below we present elastomers with unique properties from Kuraray and other well-known examples.
Elastomers from Kuraray
Other popular examples
You’ll find rubber everywhere in our everyday lives. Tens of thousands of everyday articles function thanks to rubber – from the small rubber seal to the kilometer-long conveyor belt. Elastomers are also used as a material for a well-known everyday product whose stretching capability we are all familiar with: Rubber bands.
Contact for business
Do you have questions about our products? We will be happy to answer your questions! Please contact us to learn more about Kuraray’s high-performance elastomers.
Contact